
Spectro Alloys Corp., Rosemount, Minnesota, celebrated its 45th year in business in 2018. Company President Luke Palen credits the company’s success to providing better solutions to its customers through its innovative recycling processes.
The family-owned company sorts mixed nonferrous metals and produces die cast and foundry alloys from recycled aluminum at its single facility in Rosemount.
“The aluminum recycled at Spectro Alloys is shipped to regional die casters and foundries, where it is made into new products, like lawn mower engines, ATV (all-terrain vehicle) components, car parts and more,” Palen says. “We also work with large OEMs (original equipment manufacturers) to provide comprehensive solutions.”
Spectro does not focus on toll processing or closed loop recycling for these clients but on maximizing value and efficiency throughout the supply chain, Palen adds.
“Closed loop programs can be great at lowering the outright cost of recycling aluminum, but they don’t necessarily maximize value. Many times, there are higher value uses for a given scrap stream than simply tolling it back into what it came from.”
Always buying
Spectro purchases roughly 300 million pounds, or 150,000 tons, of aluminum scrap annually. However, Palen says he prefers to measure the company’s size in terms of environmental benefits. “Recycling aluminum uses over 90 percent less energy and emits 90 percent less CO2 than smelting virgin aluminum,” he says. “At Spectro, we recycle enough aluminum to power over 200,000* homes and take over 80,000 cars off the road.”
The company purchases a range of aluminum scrap, such as aluminum cast, sheet, extrusions, turnings, mixed low-copper clip (MLCC), rims and zorba. Spectro also purchases radiators, painted aluminum siding, twitch and tweak.
In 2015, Spectro installed a scrap sorting plant at its facility. The equipment allows the company “to better control chemistries and remove potentially hazardous material” before the scrap enters the furnace, Palen says.
“Before we put it in, typical secondary scrap grades like cast and sheet were just not available regionally in volumes needed to meet our customers’ needs for recycled aluminum, so we had to find a more creative way to meet customer demand,” he says. “We saw an opportunity to invest in a process that could allow us to recycle the largest volume of regionally generated aluminum. We are now able to process zorba and other shredded mixed nonferrous scrap and provide our customers a reliable supply of recycled aluminum alloys.”
Spectro operates two reverberatory (reverb) furnaces and employs continuous casting, which it has been using for more than 20 years. The company’s continuous casting process involves constantly adding scrap to the furnace while tapping out specification metal. “Our process allows us to ‘drive’ our furnaces efficiently through a broad range of customer specs without plugging or draining,” Palen says.
With continuous casting, Spectro achieves throughput and efficiency levels that are unattainable with batch casting.
Spectro also operates a delacquering kiln to remove coatings from the aluminum scrap it processes, a shredding system and a rotary furnace, which was its most recent investment and has been operating since November 2018.
Investing in growth
Spectro announced that it was investing $5.5 million to expand its operations in late 2017. The project included a new building to house a 21-ton rotary furnace capable of melting a wide range of aluminum scrap. The furnace included a filtration plant designed to reduce emissions from the recycling process.
At the time the investment was announced, the company said it would add jobs, expand its recycling capabilities and improve melting safety and efficiency by reducing gas and electricity needed in the recycling process. Spectro has since added five employees and now employs 155 people, Palen says.
"The rotary furnace allows us to efficiently process material like breakage and foundry dross that we could not process before. Being one of the largest rotary furnaces ever installed in North America, it also gives us a recovery and efficiency advantage.” – Luke Palen, Spectro Alloys Corp.
He adds that the company has been getting used to the rotary furnace’s new capabilities but is excited about its performance so far. “The rotary furnace allows us to efficiently process material like breakage and foundry dross that we could not process before. Being one of the largest rotary furnaces ever installed in North America, it also gives us a recovery and efficiency advantage.”
Spectro is planning to undertake yet another expansion that will involve adding billet and slab casting. The billet expansion is scheduled for 2020 and will involve securing land or a building nearby, Palen says. All of Spectro’s investments are designed to increase the company’s competitiveness by improving its efficiencies and capabilities given the market dynamics at play.
“Demand has been fairly strong and scrap is abundant, but competition has increased and prices are falling,” he says. “While many economists and OEMs are talking about the negative impact of primary aluminum price increases, recycled aluminum costs have been dropping.”
Strengthening the supply chain
The trade situation heading into 2019 shows how the cards have been stacked against the domestic aluminum industry for more than 20 years, Palen says. “It has also revealed the relative strength and opportunity presented by recycled aluminum alloys.”
As trade barriers are dismantled, the U.S. must create an environment that encourages domestic scrap consumption and the associated downstream benefits, Palen says. “Scrap dealers, recyclers and casters all will gain by promoting more domestic scrap aluminum consumption.”
He says Spectro cares about the future of the aluminum supply chain, which is why the company’s employees are involved in leadership roles with various trade associations, including the Institute of Scrap Recycling Industries (ISRI), the North American Die Casting Association (NADCA) and the American Foundry Society (AFS).
“We are proud to be founding members of the Aluminum Recyclers Council (ARC), which was created [in 2018] to give a voice to our industry and to address key issues together,” Palen says.
In addition to what he says is an “unlevel playing field” that favors primary aluminum, he says the aluminum recycling industry also is threatened by the transition to electronic vehicles (EVs).
“In an EV, the two largest aluminum castings, the engine and transmission, are gone,” Palen says. “EVs still contain plenty of aluminum, but they are initially being engineered for primary aluminum instead of recycled alloys.”
He says because primary aluminum producers compete with their own material whenever it’s recycled, “their solution is to engineer new applications to specs that aren’t conducive to using postconsumer recycled aluminum.”
However, he remains optimistic that OEMs will embrace recycled aluminum and that EVs eventually will present an opportunity for aluminum recyclers. “Smart OEMs will realize the enormous benefits of recycled aluminum, and more applications will be tailored for it,” Palen says.
With its recent and ongoing investments, Spectro Alloys should be well-positioned to meet the increasing demand that would result if Palen’s beliefs become reality.
Get curated news on YOUR industry.
Enter your email to receive our newsletters.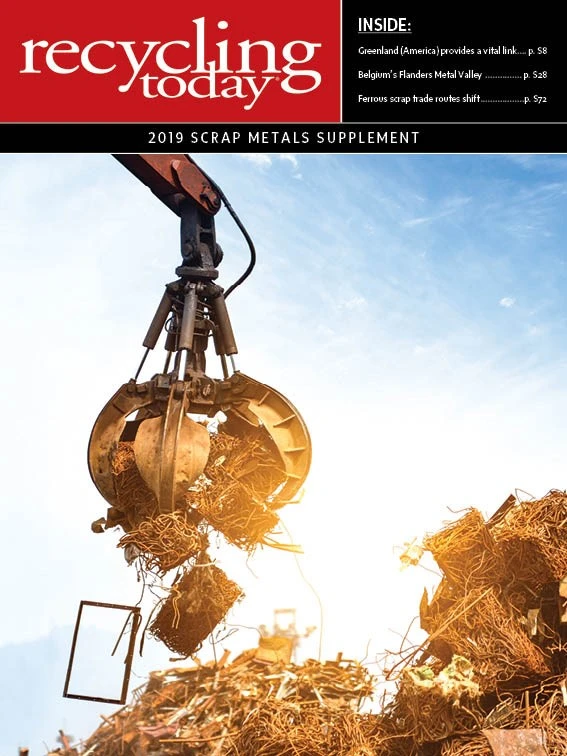
Explore the January 2019 Scrap Metals Supplement Issue
Check out more from this issue and find your next story to read.
Latest from Recycling Today
- Republic Services, Blue Polymers open Indianapolis recycling complex
- Altilium produces EV battery cells using recycled materials
- Brightmark enters subsidiaries of Indiana recycling facility into Chapter 11
- Freepoint Eco-Systems receives $50M loan for plastics recycling facility
- PET thermoform recycling the focus of new NAPCOR white paper
- Steel Dynamics cites favorable conditions in Q1
- Hydro starts up construction in Spain
- Green Cubes unveils forklift battery line