Three-color mixed glass is not a lost cause. Not only is it suitable for aggregate applications, Gallo Glass Co. is also making bottles out of it.
With commingled collections on the increase, material recovery facilities (MRFs) have a variety of options for recovering the glass portion of the recyclables stream. While each involves varying degrees of return on investment, each is successful at diverting glass from landfills, which for some recyclers is the foremost goal.
Possible Approaches
Cynthia Andela of Andela Products Ltd., Richfield Springs, N.Y., says that the decision to hand-sort glass by color is based primarily on the availability and cost of labor and the proximity of the MRF to the market for color-sorted glass. Mechanical recovery systems that screen the glass out of the commingled stream and pulverize it for use in aggregate applications are another option. Andela says that it doesn’t have to be an exclusive proposition; MRFs can color-sort as well as pulverize.
Felix Hottenstein of equipment maker MSS Inc., Nashville, Tenn., says that if MRFs try to market separate factions of glass, they might see a higher return.
Andela says, "Traditionally, recovering glass has always been associated with having to get it color-sorted to go back to the glass bottling companies. But there are other ways to recover the glass for alternative markets."
That’s where systems such as the Andela Commingled Separation System come in. With the "COSS," commingled containers pass below a magnetic separator and ferrous metals are extracted. The material then passes on to the breaker that reduces the glass in the stream. The material is then conveyed to a trommel screen that separates the glass from the aluminum and plastic. Plastics can be sorted manually or through the use of a screen, and an eddy current can remove the aluminum.
"You’ve got an increasing number of people looking at the glass market and saying that it’s too costly to pick and transport," Andela says. Pulverizing is a way to bring glass to a market without the labor and transportation costs. It’s also one possible adaptation for dealing with the variable quality of the glass portion of the commingled stream.
Adapting to Changes
"We’ve adapted ourselves to a changing market," Charles Porta, president of CRA-Recycle America, says. CRA, headquartered in Chicago, is the glass processing subsidiary of Waste Management Inc., Houston, with 10 processing plants throughout the U.S. "We made a very large investment over the last five or six years to prepare ourselves to be able to use the mixed glass coming out of MRFs or any other type of program."
CRA’s automated sorting equipment uses optical sorting technology to remove ceramics and metal from the glass stream and to identify and separate the material by color. "Because of the type of equipment we have at most of our facilities, we’re able to take the mixed glass from a single stream process and prepare that for use by the glass manufacturers," Porta says.
"Many of the curbside operators are going to the single stream, and we’ve seen an increase in color-mixed glass over the years. As a result of that, we recognized that the three-mixed glass was an excellent source of good material, but it couldn’t be used because it was all mixed together," Porta says. "Also, the contaminant level in three-mix glass is a lot higher than it normally is in color-separated glass. By putting in this new equipment and making the investment that we have, we’re able to take this material that at one time could only go to the landfill and convert it into a product that is not only acceptable, but actually preferred by [one manufacturer]."
Porta says the equipment CRA uses allows them to produce a cleaner, more consistent product. "You can put as many people in a line as you would like; you just can’t get it to the point where it’s a consistent, contaminant-free product."
In June, CRA opened their Union City, Calif., plant, which is set up to supply a three-color mixed product to Gallo Glass Co., a subsidiary of E & J Gallo Winery, also in Union City. Currently, Gallo is the only glass container manufacturer that uses a three-color mix to produce bottles.
"The state-of-the-art equipment that we use in this plant is absolutely exceptional," Porta says. "The material that we’re starting with in the three-color mixed stream that comes into us versus the product that we end up with to go to Gallo is like the difference between night and day. We’re really proud of the fact that we’re able to provide them with the product that they are looking for."
Porta says that the overall quality of cullet has declined in the last three or four years, whether it’s color-separated or three-color mix. "As a result of that, it’s even more difficult for glass manufacturers to use this material without it being processed in such a way that can improve the quality dramatically." Porta blames the deteriorated quality not on commingled collections, but on an attempt to keep costs down.
Joe Cattaneo, president of the Glass Packaging Institute, Alexandria, Va., says, "It’s known that the raw materials for glass are plentiful and it’s [cullet] got to really meet the same costs. You can’t really afford to pay more for lesser quality."
The Primary Market
Glass container manufacturers are the leading consumers of cullet. However, demand and pricing for the various colors varies by region. "There is a dislocation in demand based on the end product that the manufacturers are making in certain areas," says Cattaneo. "For instance, in the last few years in the Northeast, we’ve had difficulty moving green glass because there are not green glass furnaces. Now, in California because of the wine industry more than anything else, the demand for green is more than enough to offset the amount that is being collected."
Cattaneo says there are only about 50 glass container manufactures that use cullet, and they are primarily located in California, Pennsylvania, New Jersey, Indiana, Illinois and Oklahoma.
Hottenstein says that on the East Coast, clear glass remains the most desirable and therefore the most valuable.
Glass markets have remained relatively stable in the last twelve months. However, Porta says, "Any change in pricing to glass manufacturers for recycled glass is major, because the value of glass is not tremendously high to begin with. You can have some fluctuations in aluminum, and you still have a pretty high value commodity. But any fluctuations in glass, because of the processing that has to take place on it, definitely has an impact."
The relatively high transportation cost for glass and the uneven distribution of glass container manufacturers have led to the development of additional markets for recovered glass, which are collectively referred to by some recyclers as secondary markets.
Secondary Markets
Currently, the next largest market for cullet is in fiberglass manufacturing, although the quality standards for this application are also very high. Other applications include abrasives for use in sandblasting, water filtration, manufacturing of reflective beads for roadways and frictionators in matches and bullets. Additionally, landscaping and aggregate applications are increasing.
Andela says that Gardenville, a San Antonio company, is taking the pulverized sand from a local MRF and using it as parking lot cover and decorative landscaping. "They are selling it for, I believe, $22 per cubic yard, which is about as good a price as what people can get for it if they color sort it," Andela says. She says this kind of local landscaping application is one of the most promising secondary applications because it requires minimal additional processing and the price of the end product is comparable to what container manufacturers pay.
"It’s a matter of the recyclers interfacing with the landscapers. A lot of municipal recyclers actually make compost and sell it. So they already have material going out to landscapers," Andela says. "But they have to produce something and put it out where somebody can see it [and] feel it." Andela cites Ocean City, Md., where recyclers have gone to their local road department and had them mix the glass aggregate material in with the sand and gravel used for road base.
Diversion Sought
Although there is concern whether glass will continue to be included in some curbside programs, its weight could prove advantageous in this instance.
Tom Reik, vice president of CRA, says that most municipalities are ardent about keeping glass in their programs because its weight helps them considerably in meeting diversion goals.
John Davis, president of the California Resource Recovery Association, manages a public agency contract with a private recycler. "We’re driven by trying to maximize diversion rates. Glass is a pretty heavy material, so we’re going to get as much of it out of [the waste stream] as we can," he says.
The author is a Recycling Today staff member who can be contacted via e-mail at dtoto@RecyclingToday.com.
Get curated news on YOUR industry.
Enter your email to receive our newsletters.
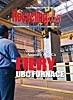
Explore the December 2001 Issue
Check out more from this issue and find your next story to read.
Latest from Recycling Today
- Returpack reports increased DRS activity in Sweden
- Trade groups align against European export restrictions
- Construction, auto sectors show mixed signals
- Politics in Turkey threaten recycled steel outlet
- Toppoint Holdings expands chassis fleet
- Lego creates miniature tire recycling market
- Lux Research webinar examines chemical recycling timetables
- Plastics producer tracks pulse of wire recycling market