Recovering raw materials from obsolete electrical equipment and electronics is similar to panning for gold. It takes patience, sifting and sometimes a keen eye, though in this case, it’s in the form of optical sorting equipment.
Electronics recyclers are moving beyond the typical magnets and eddy currents and incorporating other separation and sorting technologies into their operations, including optical sorters; electrostatic, air and fluid-bed separators; and sieves, with the object of producing clean raw materials that can be reintroduced to the manufacturing process.
We look at the operations of three electronics recyclers to see how they handle the task of sorting a diverse stream of incoming electronics into saleable secondary commodities.
SHRED LIGHTLY.
"Our focus is to make a commodity for use in remanufacturing," says Tom Fellows, vice president of special projects for Global Electric Electronic Processing Inc. (GEEP), a division of Barrie Metals Group, based in Barrie, Ontario. "The higher the value, the easier it is to sell on the global market," he says of the material his company produces.
ERI CEO Addresses Investors |
John S. Shegerian, chairman and CEO of Fresno, Calif.-based Electronics Recyclers Inc. (ERI), discussed electronics recycling and "e-waste" at the Canaccord Adams "Ready, Set, Recycle" Investors Conference in Chicago April 19. Addressing an audience of investors and financial analysts looking for specific insights into the biggest trends of emerging recycling-related industries, Shegerian stressed the mounting environmental problems caused by the glut of the nation’s electronic scrap and outlined the long-range national and international potential of electronics recycling as a concept and as an emerging industry. The "Ready, Set, Recycle" Investor Conference is a new investors meeting designed by Canaccord Adams to offer investors an opportunity to learn about electronic recycling, green building, bioenergy and metal recycling from companies in the recycling sector. "The state of California passed landmark legislation, creating a regional infrastructure to mange this problem—and the entire country is moving in the direction of following suit," Shegarian says. "With a dozen states legislating a variation of the California model within the next five years and growing global concern about e-waste, the sky is the limit for this burgeoning industry." |
High value is synonymous with high purity, though most electronics recyclers say they are not yet capable of making grades that fit neatly into the specifications provided by the Institute of Scrap Recycling Industries Inc. (ISRI). However, there are exceptions, such as No. 2 copper.
GEEP’s goal is not to shred the electronics it processes to the point where sorting becomes difficult. "We use a series of steps to be able to harvest the commodities earlier before they are shredded into a mixture," Fellows says.
Electronics that have been though triage are sent through a chain shredder, which breaks down the material to recover large pieces of plastic, aluminum and steel. By using the chain shredder, Fellows says GEEP is able to pull out the steel early in its process. "We are able to get it out at the first stage without contaminating the rest of the fraction."
Next, the pre-shredded material is conveyed to a hammermill-style shredder, where it is further reduced in size to liberate plastics, aluminum, copper and circuit boards, according to Fellows.
The output is then conveyed to electrostatic and air separators, which separate the plastic fraction from the metals fraction. Circuit boards also are sorted out and sent to GEEP’s precious metal shredder.
"A lot of our commodity quality is driven by what is acceptable by the manufacturer’s criteria," Fellows says. Manufacturers can sometimes blend a secondary commodity of lesser purity and be able to use it in their various applications.
According to Fellows, GEEP tries to control the purity of its end products by batching its infeed material when possible. "We like to batch for efficiency," Fellows says. Electronics with a greater concentration of ferrous content can be processed more quickly because the magnets do most of the work, he adds.
In the coming months, the company will add to its separation equipment in an attempt to further purify its commodity streams, Fellows says. A water table will enable GEEP to sort plastics from metals based on density, while a new optical sorter will allow the company to sort plastics by type.
ERIEZ INTRODUCES AIRLESS OPTICAL SORTER Eriez Manufacturing Co., Erie, Pa., has introduced ProSort Airless Metal Recovery Systems, which, according to the company, offer "superior metal recovery at a fraction of the cost" of operating an air-driven sorter. The ProSort uses high sensitivity metal sensors aligned with low energy electromagnetically driven paddles to separate metals. According to Eriez, the unit’s modular design and alignment of sensors, paddles and controls can operate in different modes during a single cycle. Its dual mode sorts and separates ferrous metals, nonferrous metals and stainless steel in a single operation. The system requires less than 25 percent of the energy needed to operate air-powered sorters, according to Eriez. More information is available at www.eriez.com.
Fellows says, "Plastics are difficult to sell unless you have single types of plastics that you process as a batch, which people are interested in putting back into manufacturing." He adds, "We’re upgrading our plastics so we can expand our market base."
The company’s optical sorter will enable it to sort smaller pieces of plastic for sale as a secondary commodity. Currently, however, its ground plastics are processed through GEEP’s NanoFuel line, which converts all of the company’s commingled plastics into diesel fuel using a depolymerization process, according to Fellows.
GEEP is able to use the fuel in its generators to power its facilities, Fellows says. The fuel is also available for use in off-road applications.
Currently, GEEP’s operation also includes a wire chopping line and a CRT line that results in glass that is returned to the manufacturing process.
GEEP is not the only company that is looking to optical sorting as a way to produce material streams of higher value.
THE EYE OF THE BEHOLDER.
CTR Electronic Recycling Inc. is a new electronics recycling company that is ramping up production at its 150,000-square-foot facility in Galion, Ohio.Along with more traditional separation technology, the company has also installed an optical sorting line to sort plastics by color.
CTR’s Ron Spayde says the company began working through its 2 million pound inventory in December of 2006, fine tuning its processing line along the way. The company is capable of processing 20 million pounds of electronics per year.
Spayde says the CTR’s process is "just about horsepower" and raw material recovery. The company’s process begins with two in-line shredders. The first shredder reduces infeed material to a 3 inch by 3 inch by variable size, and the second shredder further reduces the material to a 1.5 inch by 1.5 inch by variable particle size.
Magnets follow each shredder and recover ferrous material from the stream. Further downstream is an eddy current separator that recovers nonferrous material while discharging plastics and residual metals into different directions.
Recovered plastics are then run through the company’s optical sorter, where they are sorted by color and type, including ABS, polystyrene and polycarbonate. The optical scanner cannot scan black plastics because it works by reading the wavelength of reflected light, so that material passes through the sorter and forms a color-sorted stream of mixed plastics, according to Spayde.
The commodity streams CTR produces are classified as steel, copper, aluminum, plastics, circuit boards and wire, which is send on to a chopping line in Indiana.
"Our products are raw material ready," Spayde says, though he adds that they don’t quite conform to an ISRI spec."
CTR also is on the lookout for other separation and sorting advances that can improve the efficiency of its operation. "We have other lines and other advances on the blueprint board," Spayde says.
Another company with its eye on technological advancements is MaSeR Corp., with its processing plant in Barrie, Ontario.
BY DEGREES.
MaSeR Corp., a U.S.-based company with a plant in Barrie, Ontario, Canada, begins its recycling process by running material through a primary shredder that breaks it down into 6-inch chunks, after which large pieces of plastics and steel that do not require further processing are pulled. The company refers to this as the "preparation phase."The material that remains passes through a ring mill shredder and under an eddy current separator, which removes some of the aluminum in the stream.
MaSeR’s Lauren Roman says the company then sends the material through a granulator, which completes the size reduction on the front end.
The material then passes under a cross belt magnet, which removes 99 percent of the ferrous material, and another eddy current, "which kicks out aluminum and shakes out copper and precious metals fines," Roman says. A third of what comes out is a nonferrous mix that includes circuit boards with embedded metals. Typically, electronics recyclers would send this material to a smelter for the recovery of copper and precious metals, she says. However, MaSeR does not consider itself the typical electronics recycler.
Following the granulator, the mixture of fastened, coated and/or laminated materials enters the "delamination phase," which begins with MaSeR’s Fractionater. According to Roman, the process uses centrifugal force to tear apart the material, liberating pieces that may be welded or screwed together.
The resulting material is then sent through cyclones and sieves to be sorted by density, Roman says. The process results in three distinct streams of material: white metals (aluminum), red metals (precious metals and copper) and plastics.
MaSeR currently gives away its mixed plastics to various manufacturers that use it in low-value applications, such as manhole covers. She says the plastics that result from the process are the consistency of a powder and cannot be melted, but are instead heated and compressed into new products.
"We are looking at a couple of different technologies where we are going to try to pull off the plastics before it goes through the Fractionater," Roman says. The sizes of the plastics after it passes through the Fractionater—typically 4 millimeters—is too small to be sorted effectively by optical means, she adds.
MaSeR spends a lot of energy researching the best markets for its products, according to Roman. "It is highly marketable for the most part," she says. "Our research is to find the ultimate market."
MaSeR began processing commercially in December of 2005. The company currently processes 500 to 600 tons of material per month and is on target to process 800 tons per month by August, Roman says. "We are certainly happy with our progress."
The company targets its services toward demanufacturers, saying MaSeR can help them to reduce labor costs, free up storage space, eliminate unnecessary smelting charges and recover more plastic and aluminum.
FURTHER INNOVATIONS.
The electronics recycling industry is far from static. As companies prioritize raw material recovery, sorting equipment will continue to grow in importance. These three electronics recyclers show that by continuing to fine-tune their systems, they are getting closer to the goal of optimal efficiency and recovery and to commanding the highest value for their secondary commodities.The author is managing editor of Recycling Today and can be reached at dtoto@gie.net.
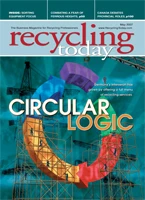
Explore the May 2007 Issue
Check out more from this issue and find your next story to read.
Latest from Recycling Today
- Nucor receives West Virginia funding assist
- Ferrous market ends 2024 in familiar rut
- Aqua Metals secures $1.5M loan, reports operational strides
- AF&PA urges veto of NY bill
- Aluminum Association includes recycling among 2025 policy priorities
- AISI applauds waterways spending bill
- Lux Research questions hydrogen’s transportation role
- Sonoco selling thermoformed, flexible packaging business to Toppan for $1.8B