Just a few years ago, operators of material recovery facilities (MRFs) would often wonder aloud whether the collection and processing of plastic bottles was worth the effort.
Among the factors that made the recycling of plastic such a challenge was the combination of the strict purity required by consumers of the material coupled with the relatively low cost paid for it.
An equation like that often looked unsolvable and provoked the question: Why put time and effort into an enterprise with so little reward?
But global forces have changed many of the variables in that former equation, and now recyclers are eager to process as many plastic bottles as they can move through their facilities.
To do this profitably, sorting is still required at some step in the process, as most consumers of the material still desire a specific resin with a low contamination threshold.
That drive for purity and profits has helped spur advances in automated sorting that can be found along every step from the MRF to the consumer.
THIRSTY MARKET. For as long as MRFs have existed, a stream of beverage cans and bottles has poured into the front door and been presented to plant managers and secondary commodity brokers charged with the task of sorting, processing and marketing a saleable commodity.
Over time, that stream has included an increasing amount of plastic, as it has become a material of choice for marketers of carbonated soft drinks and bottled water.
A typical municipal program will accept No. 1 PET beverage bottles in a variety of colors, as well as other PET packaging (ketchup, shampoo or cooking oil bottles, to name a few examples), plus No. 2 HDPE milk jugs and other containers stamped No. 2. In some programs, all plastic packaging containers containing a recycling code No. 1 through No. 7 are collected.
While recycling coordinators may be eager to take in whatever containers their citizens put in their bins, most recovered plastics consumers are not looking for a mixed bale.
MRF operators have turned to staffed sorting stations and mechanical screening devices to address some of the necessary sorting. Increasingly, though, automated devices using optical technology and targeted air nozzles are being deployed for maximum sorting capability.
Manufacturers such as the MSS subsidiary of CP Manufacturing, National City, Calif., and TiTech, a European company represented in the United States by Lubo USA, Stamford, Conn., have responded to a noticeable increase in demand for such equipment.
Lubo USA Midwest Regional Manager Scott Jable says the TiTech equipment uses a beam of near-infrared light to scan passing material that must be presented on a conveyor in a single layer. The beam reads a reflection that determines the molecular composition of each bottle.
The information read by the beam is saved as an outline of the material as it passes to an array of air nozzles that have been pre-programmed to eject one or more types of material.
The Glamour of Film |
Scrap plastic film has doubled in value, creating new opportunities for recyclers of the material, according to a presenter at the recent 2006 Global Plastics Environmental Conference (GPEC). Plastic film is now fetching up to 24 cents per pound up from about 11 cents per pound in 2004, says Daniel Schrager, president of NextLife Recycling, Delray Beach, Fla. The increased pricing represents a vibrant export market for the material, says Schrager. "Until recently, there were very few markets for recovered films [and] a dependence on one industry—composite lumber," he said. NextLife produces 100 recycle-grade resins from film and plastic bags used by makers of trash pails, recycling bins, pallets, park benches and other products. The challenge for NextLife and other companies is trying to establish a collection infrastructure to obtain adequate feedstock, says Schrager. If collection points can be established in stock rooms and distribution centers for film and at retail locations for plastic bags, the recovery rate for these materials may soar from the current 3 percent to 5 percent level. The GPEC 2006 event, organized by the Society of Plastics Engineers (SPE), took place in Atlanta in late February and early March. |
According to Jable, plant operators request a variety of configurations, although typically they might seek to separate PET from HDPE while perhaps further isolating the clear portion of the HDPE stream.
Deploying such equipment allows recyclers to put together higher-value bales that will still make their way to another step in the recycling chain—either directly to a consumer that breaks its own bales or to a custom plastics processor that will turn bales into a sorted flake commodity.
NO SMALL FEAT. Optical sorting machines that can distinguish one bottle from another on a moving conveyor are an impressive step forward for recyclers.
In the food processing industry, however, such machines have been used for decades to sort much smaller items, including beans, corn and even grains of rice.
Pat Pike, a Michigan-based senior regional sales manager for Satake USA Inc., Houston, says one of the first electronics sorters in the food processing industry was deployed in a navy bean packaging plant in 1931 by Westinghouse.
"Back in the mid-1980s, some of this technology started finding its way into the plastics industry and the recycling industry," says Pike.
As plastics recycling has become more common and the value of plastic scrap has increased, Pike says Satake USA has seen an increase in demand for its products.
The company’s line of ScanMaster machines are all optical sorters, but different models use different technology. The ScanMaster II XE uses infrared sensors and is primarily used to distinguish PET flakes from PVC flakes. The ScanMaster II SE uses ultraviolet sensors to distinguish clear PET flakes from opaque ones, while ScanMaster CCD Camera models look for non-conforming flakes at a rates of 1,000 to 8,000 pounds per hour.
Just as at the MRF stage, the desire for a pure, marketable grade of flake combined with an increasingly diverse stream of material is keeping equipment suppliers busy to find the best automated solutions.
"The challenge with the recycling stream is that it is changing constantly," says Pike. "PET recyclers are seeing more blue bottles coming into the stream, and some beverage companies put out products in red plastic bottles last holiday season," he notes.
Sorting machines must also be able to distinguish PVC ketchup bottles (or flakes) that manual sorters may have assumed to be PET. Some plastic bottles or flakes also contain titanium oxide (TiO2), which can be distinguished by some optical sorting machines but not necessarily by others.
Thus, manufacturers like Satake USA must offer a variety of equipment that can be configured in different ways to meet the customized needs of a buyer.
"Many of our customers are targeting one item, but they may have to remove a variety of contaminants," says Pike. "In any given application, there might be a defect that manifests itself in the ultraviolet scan, or in the infrared. It can even vary geographically, depending on regional bottling habits."
Right now, though, plastics recyclers’ potential returns are allowing them to invest in automated equipment that helps them overcome those obstacles.
END OF THE LINE. After plastic scrap has been handled by haulers, MRF operators and possibly a custom re-grinder or an export broker, it ultimately finds its way to a consuming destination that often has narrow chemistry and color specifications.
One such consumer of PET plastic bottle scrap in particular is Mohawk Industries, a Calhoun, Ga.-based manufacturer of flooring, carpet padding and cushion material.
In coordination with the recent 2006 Global Plastics Environmental Conference (GPEC 2006), sponsored by the Society of Plastics Engineers, the company hosted a tour of one of its plants in Summerville, Ga.
The plant produces a variety of materials on several production lines, including a cushion and pillow fill material made from re-processed post-consumer PET bottles.
The plant’s equipment can also be configured to produce stain-resistant carpeting made from the same stream of scrap bottles.
The Summerville plant contains four shredding and sorting lines that process up to 100,000 tons of PET bottles each year, according to a report on an Athens, Ga., Web site—a significant percentage of all the post-consumer PET collected in the United States each year.
The company’s recycling process starts with breaking the bales it receives and sending the bottles through large trommel screens or tumblers to remove loose dirt.
Conveyors then pass by manual sorters who remove non-PET containers that have made it into the bales, including enough crushed aluminum cans to regularly fill a truck trailer for shipment to a secondary aluminum producer.
Optical sorting equipment with accompanying air jets made by MSS Inc. is also deployed to remove PVC and off-color containers from the stream.
Bottle caps and labels are also removed during this process, with each sent to different facilities to be used in other recycling applications.
After the bottles pass through the gauntlet of manual and mechanical sorting steps, they are ground into flakes to face more scrutiny, with electro-static and other technology used to help purify the flake stream before it heads to the extruding, drawing and spinning portions of the plant.
What Mohawk accomplishes in-house at Summerville is the conversion of bales that—despite the best efforts of recyclers—contain a mixture of materials (including caps, labels and contaminants) to produce a saleable end product.
It seems likely that if oil and petro-chemical prices have reached a new, higher plateau, such efforts will continue to increase as a means of keeping plastic out of the landfill and within the commodities loop.
The author is editor of Recycling Today and can be contacted at btaylor@gie.net.
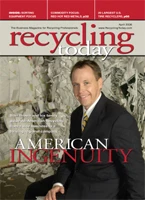
Explore the April 2006 Issue
Check out more from this issue and find your next story to read.
Latest from Recycling Today
- Nucor expects slimmer profits in early 2025
- CP Group announces new senior vice president
- APR publishes Design Guide in French
- AmSty recorded first sales of PolyRenew Styrene in 2024
- PRE says EU’s plastic recycling industry at a breaking point
- Call2Recycle Canada, Staples Professional expand partnership
- Circular Services breaks ground on north Texas MRF
- Tariff uncertainty results in choppy nonferrous scrap flows