M
ixed C&D material, with its everything-and-the-kitchen-sink makeup, can represent a significant challenge for recyclers. That’s not to say that it’s impossible to arrive at a variety of clean end products, as long as the system employs the appropriate level of automation in combination with hand sorting.Screening equipment, from trommels to vibrating screens to finger screens to disc screens, can facilitate further separation and sorting of mixed C&D material by sizing the material as it moves through the system, creating an overs line that is hand picked and an unders line that is separated into its constituent parts using automation in the form of magnets, air classification systems and sink tanks. The diversity of the materials in the stream makes this a challenging, though achievable, process,
MATERIAL COMPLEXITY. "The only consistent thing about mixed C&D material is its inconsistency," Bill Guptail, director of process sales for General Kinematics, Crystal Lake, Ill., says.
While it’s not difficult to separate functionally, he says the percentage of material that will constitute the overs and unders lines is difficult to know when setting up a system.
"When you design a system where you split material flows, it is difficult to know what will go on through the unders screen so you can design the downstream processing appropriately," Guptail says.
Dirk van der Wal, managing director for screening equipment manufacturer Waltec, based in the Netherlands, says C&D material doesn’t have to be difficult to separate, as long as the correct processing principles are used.
Scott Jable of Lubo USA, a screening and recycling equipment manufacturer headquartered in Stamford, Conn., says that mixed C&D material is difficult to separate in light of its complex composition. "You can get carpeting grabbing hold of rebar that is still wrapped up in concrete," he says. This complexity requires more sophisticated separation systems, Jable says. "It requires a little more automation to do it successfully."
The challenge lies in sorting a large volume of material while keeping labor costs low yet still producing clean end products. "To accomplish all three of these is difficult and a great measure of success," says Jable.
The composition of incoming material is an important factor in determining the appropriate screening and sorting system for a company.
SYSTEM CONFIGURATION. "All separation systems start with a correct analysis of the composition of the material to be processed at a desired volume per hour," van der Wal says.
He adds that nearly all systems work on the principle of degrees of separation that involve screens, air classification, float tanks and magnets as well as hand sorting.
"The first thing that has to happen is a pre-sort of material before it goes onto the system," Jable says. "There are always prohibitives that you don’t want to put into the system," he says, citing couches and kitchen sinks as two such examples.
Jable likes using vibratory feeders to feed material to the system because they help to spread material out. "A conveyor doesn’t do that. You get lumps and clumps," he says. He then suggests another pre-sort on the mezzanine to remove smaller residuals such as plastic sheeting and toasters.
However, John O’Neill, vice president of sales and marketing for McCloskey International, Peterborough, Ontario, Canada, prefers using trommels to feed material into the system because they can handle irregular shapes and do not clog easily, making them lower in maintenance, he says.
O’Neill adds that vibrating screens are preferable in applications where the material is sized anywhere from 3/8 inches to ¼-inch minus. "You get the right screen cloth on there, and it can size the material a lot faster than a trommel screen could."
Jable then suggests a large cut to remove 2-foot-minus material so that manual pickers can sort the overs line easily because the volume of material on the conveyor is reduced.
"On the overs line of the large screen, you can pull all commodities and let the residue go off the end as a negative sort or let the aggregate be the negative sort if there is a lot of that on their line," he adds.
Jable stresses the need for flexibility. "A good system should be modular," he says. "You may start off small and have a single line without much automation. A good system will allow you to grow easily, add a second line, air systems and magnets."
Guptail says, "A system should be designed based on volume," adding that the overs line should be designed to handle most of the system’s volume. "The unders line takes 60 percent by weight, but only 30 percent by volume," he says.
For high-volume recyclers, Guptail suggests using a finger screen to make a primary cut of nominal 8-to-10-inch material, sending the overs material along to a picking line and the material under 10-inches on to the unders line, where a magnet will recover the ferrous material in the stream. At this point, the material on the unders line will go on to a secondary finger screen that will remove 2-inch-minus material, while the larger material will go on to the a de-stoner classifier to recover the aggregate.
General Kinematics and Sherbrooke OEM, Sherbrooke, Quebec, Canada, put in a classification system at a Florida recycling facility that Guptail says he considers an ideal system. The system, which can process up to 500 cubic yards per hour, uses two dual-deck vibratory finger screens to receive and size material at 8 inches. Following the first cut, heavy-duty apron conveyors elevate and transfer material to a trommel and picking platform. The minus-8-inch material goes on to an automating sorting line.
For recyclers producing less volume, Guptail suggests removing the 2-inch-minus material using a finger screen and manually picking the larger material.
MEASURES OF SUCCESS. While a few yardsticks can measure the success of a screening system, for Jable, nothing is more important than the quality of the end products.
"If you don’t have high-quality end products, the markets tend to go away," he says. "You need to run as fast as you can with maximum throughput that still allow you to get saleable end products."
Jable also says C&D recyclers should consider their processing rate and the amount of manual labor involved in arriving at their end products. "If a company can do 10 or 12 tons per hour [but] get dirty or unsellable product, they haven’t maximized the return on their investment," he says.
Guptail suggests that the percentage of recovered products a company achieves through its screening and sorting system is a good measure of a system’s effectiveness.
Van der Wal indicates that the best measure for a system is the purity of the finished product because it determines the price of the yield. "You can make a really great product, but if it costs more than it earns, then that makes no sense. This is the difficulty with C&D recycling," he says.
"C&D recyclers must continue to create high-quality end products to be open to the largest variety of end markets," Jable says. "If recyclers create quality to sell, more people are going to buy."
This feature originally ran in the March/April issue of Construction & Demolition Recycling magazine. The author is managing editor of the Recycling Today Media Group and can be reached at dtoto@gie.net.
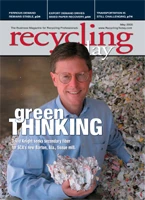
Explore the May 2005 Issue
Check out more from this issue and find your next story to read.
Latest from Recycling Today
- Nucor receives West Virginia funding assist
- Ferrous market ends 2024 in familiar rut
- Aqua Metals secures $1.5M loan, reports operational strides
- AF&PA urges veto of NY bill
- Aluminum Association includes recycling among 2025 policy priorities
- AISI applauds waterways spending bill
- Lux Research questions hydrogen’s transportation role
- Sonoco selling thermoformed, flexible packaging business to Toppan for $1.8B