E
lectronics recycling is still an emerging industry, which meansthat many recyclers—and equipment providers to the industry—are still experimenting with the processing methods that can best serve their needs, as well as those of their consuming markets.
While many recyclers engage in some degree of testing and manual disassembly to recover resalable components, eventually, many end-of-life electronics will be sent along an infeed conveyor to meet the hungry jaws of a shredder. What emerges from the other end can vary widely depending on the infeed material. The amount of automation that recyclers employ to sort and separate the electronics’ constituent materials can also vary widely.
When setting up a processing system for electronics, manufacturers often recommend considering the system as a whole, not just the individual components. Versatility is another important factor, as the composition of various electronics can fluctuate widely.
Envirocycle Inc., headquartered in Hallstead, Pa., with processing facilities in Rancho Cucamonga and San Diego, Calif., and in Mount Pleasant, Pa., has made a conscious decision to avoid shredding in favor of disassembly.
BY HAND. Greg Voorhees, vice president of operations for Envirocycle, says manual demanufacturing allows the company to provide jobs to people in the communities where it operates, as well as to cut down on airborne particulates that could affect the health of employees.
"We were also concerned that shredding increases the amount of material that is unacceptable for recycling and has to be disposed of," Voorhees says. "We have managed to reduce our actual disposal rates to less than half of a percent."
The company is marketing working equipment and components to resale markets, as well as raw secondary materials. Envirocycle’s dismantle department can process roughly 135,000 pounds per week during one shift, while the company’s glass department processes a minimum of 200,000 pounds weekly.
"Mainly our process is affected by the frequency or regularity of the incoming material; basically we can process as much as we receive," Voorhees says.
"Our lines are set up in such a way that all of the material passes by multiple people, each charged with different tasks," he says. "For example, on our dismantle line, after the unit is disassembled, the glass is sent in one direction and the rest of the material in the opposite direction. Then the components are segregated based on type, such as the kind of plastic, circuit boards or color or black-and-white tubes and so on."
Envirocycle staff sorts the glass by hand, first by size, then by type—either funnel or panel—then by chemistry—leaded or lead-free. "We think this system of multiple checks allows us to remove contamination and avoid mixing materials," he says.
When considering further automation, Voorhees recommends taking a practical approach. "You have to be realistic about what kind of return you are going to get for the material you generate and compare that to the initial cost of the equipment, the cost of maintaining it and your other expenses," he says. "Compare that to what you pay now for wages and other employee expenses."
Voorhees also recommends assessing a company’s long-term goals prior to setting up a processing system, considering the expandability of the system and the equipments’ ability to keep up with increasing volumes of incoming material. Companies should also consider the effect of declining volumes of incoming material. "If it decreases dramatically, can you afford your monthly payments?"
For the companies who have opted to include shredding as a means to recover the constituent parts from electronics, downstream sorting can vary.
HELPING HANDS. Intechra, an IT assets disposition service provider with a 193,000-square-foot processing facility in the Dallas-Fort Worth area, employs a magnetic pulley to remove ferrous materials downstream from its shredder. The company relies on hand sorters, however, to recover the remaining materials.
Grover Edmiston, vice president of operations at Intechra, says the company processes IT equipment of all kinds.
Currently, Intechra processes roughly 1.2 million pounds of electronics per month through its shredder.
Prior to shredding computer monitors, Edmiston says the Intechra staff performs manual disassembly. "We bale the plastics from the monitors and shred the glass, put it into gaylords and ship it to a downstream recycler," he says. Intechra also ships the yokes from the CRTs and the monitors’ printed circuit boards to qualified downstream partners.
Downstream from the magnet, the company uses two to six hand sorters, depending on the in-feed material. "Some think that there are not many differences in electronics. If you threw in complete computer systems, you will be sorting more items: plastic, cable, metal, printed circuit boards," Edmiston says.
He adds that Intechra is interested in adding more automation to its sorting line in the future.
"We would like to have a more self-contained system from an environmental and noise standpoint," Edmiston says.
FURTHER AUTOMATION. United Recycling Industries (URI), based in West Chicago, Ill., has opted to use more automation downstream from its shredders.
Jim Glavin, vice president of URI, says the company shreds everything from medical, IT and lab equipment to consumer products like bread makers and toasters, recovering low-grade and high-grade ferrous metals; aluminum, copper and mixed alloys; precious metals; plastics; and leaded glass.
Disassembly also factors into URI’s operations. "We have an integrated circuit division that removes components off of circuits," Glavin says. "We are doing manual disassembly for chip-on-board recovery and component recovery—like DVD or hard drives—for the resale markets." United also partially disassembles some electronics that may be too large to feed to the shredder if kept whole.
URI has developed and installed two separate shredding lines. One system is for monitors and televisions and is equipped with extensive lead abatement equipment. A second larger system is for more complex electronics. Glavin says the company can process 45 million to 50 million pounds per year through its large shredder and 35 million pounds per year through its monitor shredder, which it also uses to process less complex materials.
Downstream from URI’s shredders, magnets remove the ferrous metal fraction and eddy currents recover nonferrous metals. The company also uses different sizing and sorting screens. On the monitor line, a trommel screen aids in separation, while the more complex shredder uses vibratory screens. Glavin says finger screens further assist in copper recovery.
"You can sort anything to the nth degree, but economics really drives the sortation," he says.
With that in mind, URI is looking to make use of new sorting technology as it becomes available. "We are constantly updating our systems as our customers’ needs change," he says.
The diversity of URI’s incoming stream of electronics also requires the company to have a flexible approach to its shredding and sorting system. "It’s not like you’re making cereal with the same ingredients every time," Glavin says.
The author is managing editor of Recycling Today magazine and can be e-mailed at dtoto@gie.net.
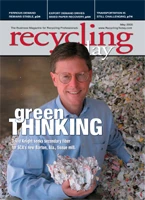
Explore the May 2005 Issue
Check out more from this issue and find your next story to read.
Latest from Recycling Today
- Nucor receives West Virginia funding assist
- Ferrous market ends 2024 in familiar rut
- Aqua Metals secures $1.5M loan, reports operational strides
- AF&PA urges veto of NY bill
- Aluminum Association includes recycling among 2025 policy priorities
- AISI applauds waterways spending bill
- Lux Research questions hydrogen’s transportation role
- Sonoco selling thermoformed, flexible packaging business to Toppan for $1.8B