S
ingle-stream recycling is taking hold in municipalities acrossthe country, and consumers of secondary commodities haven’t relaxed their standards for quality products, which makes sorting at the material recovery facility (MRF) level an increasingly integral part of the recycling process.
And for some MRF operators looking to keep their costs down and to maintain or improve the quality of their end products, municipal optical sorting technology provides an attractive alternative to traditional manual sorting methods.
"Commingled curbside [collection] is gaining popularity and generating more interest in optical sorting technology," says Scott Jable of Lubo USA, which is headquartered in Stamford, Conn. "Because more materials are being collected together, people need to find more creative, economical ways to separate it back out."
SEPARATING FROM TRADITION. The technology has been around for more than a decade, and while it’s been extremely popular in Europe since its development, only recently has optical sorting equipment began to pique the interest of a significant number of American recyclers, according to Jable.
"It’s not ‘new’ as far as being untested, it’s just now gaining popularity and acceptance in the U.S," he says.
And the number of commodities that can be sorted by optical technology is constantly expanding, Jable says. "Right now there aren’t too many you can’t use it with," he says. "At first, it was mostly used with plastic, but now we’re able to separate fiber from fiber, fiber from containers and we’re even looking into the C&D arena, being able to separate wood from stone."
The equipment works kind of like an automated human eye with arms. A conveyor transports material underneath an optical sensor, which shines a beam of non-visible light that identifies the objects below depending on how the machine is programmed. In the cases of plastics and glass, the sensor identifies the commodities as desirable and the machine tracks the material to the end of the conveyor, where it is discharged with an air jet.
With paper, the process is the same, but a negative sort technique is used—the optical sorter is programmed to pick out the contaminants from the scrap paper.
"When sorting paper, the optical sort is used to clean up after the mechanical sorting equipment," says Felix Hottenstein of MSS, a Nashville-based division of CP Manufacturing, which is headquartered in National City, Calif. "It’s not really replacing the mechanical screen, it’s more like an add-on."
Dual-eject systems are also available to allow the machines to sort out two commodities at the same time, Jable says.
And while the fundamental principals of the equipment haven’t changed much since its introduction in the market, Hottenstein says the technology is constantly being refined to be more flexible and more productive.
Jable says the accuracy of the automated machines has increased significantly since the early days of its use. "Like any new technology, it had to crawl before it ran. The accuracy is much higher—it was maybe 70 percent with the older equipment, but now it’s more like 95 percent," he says. "It’s also become much more economical—it can do eight tons per hour instead of two. All of that helps with the bottom line."
The newest facet of optical sorting technology is an attempted foray into the construction and demolition debris market. "Wood is the main driver for that," says Hottenstein. "It might be a good alternative to current systems like float tanks, especially in the north where such systems can be hampered by freezing temperatures."
However, a number of challenges exist in trying to apply optical sorting to C&D.
"There are so many unknowns to C&D," Hottenstein says. "The material is a lot more diverse." The size of the material is a big factor. "It’s a question of how big of a piece you can actually sort," he says.
THE PAYOFF. Hottenstein says the growing popularity of single-stream recycling isn’t the only thing driving more recyclers to take a closer look at optical sorting equipment.
He says single stream or not, all MRFs want better quality commodities to stay competitive in the market and that optical sorting has the edge in producing cleaner, more uniform bales. "The machine does the job the same all the time," he says.
Hottenstein also says consolidation in the industry is resulting in bigger MRFs where it makes more sense to automate.
While it’s not the only factor, volume is definitely something to consider when making the decision to include optical sorting technology in a facility.
"If you’re doing a couple hundred tons a month, you’re probably not going to justify it," says Jable. He says facilities that are processing in the 30-ton range or more of material per day would be more likely to look at optical sorting.
MRFs also have to take a close look at the commodities they’re considering using the equipment with, as materials with high-end markets that require cleaner bales could justify the system better than those whose end markets aren’t as discriminating, says Hottenstein. For instance, to justify a system for glass, he says, depends strictly on what markets the MRF has for the material. "If your eye is on the lower end market, it might not be worth it," he says.
The ratio of employees to quality is another factor to consider, Hottenstein says. "It always comes down to what kind of quality has to come out at the end," he says. "If [an operator] needs five people to achieve the quality that he needs, it might be worth it."
The investment is significant—between $150,000 and $200,000—according to Jable and Hottenstein. Hottenstein points out that the initial investment is usually less if the equipment is being built into a new facility. "Retrofitting is sometimes more complicated" and tends to be slightly more expensive, he says.
And operators should also consider what they could save in labor costs when weighing the option of optical sorting equipment.
"You have to look at the life of a system," says Jable. "It should last 10 years or more. So, if you save one sorter and his $20,000 salary over the years, or if you can save two or three sorters, you can really save money."
Cutting labor costs is another advantage to optical sorting equipment, he says. "With just about any industry, people are looking to reduce labor," says Jable. "This has become a viable option."
"If a plant gets big enough, running two or three shifts, optical sorting starts to make a lot of sense," Hottenstein agrees. "You can only put so many people in these facilities. Some plants want more throughput, so they put an optical sort in."
Labor concerns helped Bob Torriere at Recycle America Alliance, Berlin, Conn., decide to add optical sorting equipment to his operation. He purchased two of Lubo USA’s TiTech Polysort 1400 units—one in the fall of 2004 and one in early 2005—to separate Nos. 1-7 plastics out of a commingled stream.
Torriere says the additions allowed him to eliminate three sorters from his line while maintaining a throughput volume of 20 to 30 tons per day of plastic.
Torriere says he’s noticed his fellow recyclers taking more interest in optical sorting equipment recently. "It definitely has more real-world applications," he says. "A lot of people are taking a hard look at it now."
Alan Stein, president of Gulf Coast Recycling in Houston, purchased a TiTech Polysort in December 2004 from Lubo USA, and he says cleaner bales of mixed paper have been the result. The machine separates paper out of the unders of a commercial OCC screen. "We needed a way to reduce our waste stream," Stein says. He also says that the optical sorting setup takes up less space than traditional sorting equipment at his facility.
ANYBODY’S GAME. Jable and Hottenstein tout the dependability of the optical sorting equipment as superior to that of its human counterparts. "It’s not as subject to human fallibility," Jable says. "The machine is going to be there everyday, it’s not going to call in sick."
While some disagree as to what trend is behind it, more and more recyclers are considering optical sorting equipment at their facilities, even smaller operations that wouldn’t have thought it a practical option only a few years ago.
"You have to look at volume and the number of people you’re using," Jable says. "You have to ask yourself, ‘Is there a stream that I can clean up better and make more marketable?’ Anybody who has manual labor trying to sort a large volume of material can take a look at this technology and see if it applies to them."
The author is assistant editor of Recycling Today and can be contacted via e-mail at jgubeno@gie.net.
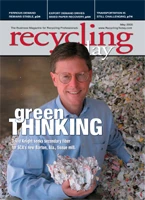
Explore the May 2005 Issue
Check out more from this issue and find your next story to read.
Latest from Recycling Today
- Nucor receives West Virginia funding assist
- Ferrous market ends 2024 in familiar rut
- Aqua Metals secures $1.5M loan, reports operational strides
- AF&PA urges veto of NY bill
- Aluminum Association includes recycling among 2025 policy priorities
- AISI applauds waterways spending bill
- Lux Research questions hydrogen’s transportation role
- Sonoco selling thermoformed, flexible packaging business to Toppan for $1.8B