Using screening equipment to sort construction and demolition materials seems to be as much an art as a science. Many C&D recyclers always seem to want to make changes to what they are doing now in order to improve their operations.
There are a number of ways to skin the screening cat. The basic mode of screening has long been the dump and pick method, where the material is brought on site, dumped on a floor, concrete or otherwise, and workers and maybe a skid steer or two pull out the recyclable commodities. Then the residual is scooped back up, put in the roll-off and carted to disposal.
Obviously the recycling rate on such a system is nowhere near what today’s modern screening and sorting techniques can accomplish and it might come with higher labor costs, as well. However, it has been proven many times to be a great way for companies to get into the C&D recycling business. These firms often bank some of their profits and develop a track record of recycling C&D that they can then use to upgrade to better equipment.
Some current C&D recyclers say two main factors contribute to how they choose to set up their screening operations: the material coming into the plant and the final products coming out.
EASY AS ONE, TWO, THREE. Jeff Leech of New Bedford Waste Services, New Bedford, Mass., says that his current plant is set up to make large volumes of alternative daily cover (ADC) with a lot of fines. "The plant is not set up for high yields of wood for boiler fuel or mulch. For that, we would have two grinders—one for the wood only and one for all the other material to be ground up for either ADC or easier transport to disposal."
To make its ADC, New Bedford uses two Action slotted screens before the picking line. One takes out the 6-inch minus, the second removes the 2-inch minus. "The goal is to give the pickers a manageable spread of material in order to recover the maximum amount of product possible," says Leech.
Florida DEP Lauds Wood Recycling Project |
An Innovative Recycling/Waste Reduction Grant application on sorting wood debris for recycling has been ranked the No. 1 application by the Florida Department of Environmental Protection (DEP). The grant was submitted by the town of Medley, Fla., on behalf of the University of Miami, the University of Florida and Florida Wood Recycling, also of Medley. This 2006-2997 grant follows on the heels of 2004-2005 Florida DEP grant on best management practices for Florida Wood Recycling to sort wood debris for mulch products that was also rated the top grant application. "Facility operators who take the initiative to incorporate the best management practices developed in the production of quality products create consumer demand and product loyalty, while ensuring the longevity of their operations," according to Harvey Schneider, president of Florida Wood Recycling. "These projects clearly demonstrate the economic and environmental benefits derived through guidance from our scientific community in the use of technological tools for the identification of undesirable recyclables." |
He says that he has run most every screen type for C&D, including a trommel, star and finger. Leech likes the slotted screen because of its simplicity and durability. "It has almost no down time. When it does go down, it is usually a $7 V belt that takes 15 minutes to replace."
A variety of screens is what Downtown Diversion and its sister company Looney Bins operate in their two Los Angeles area plants. "At our small operation we have a ReTech trommel," says Mike Hammer. That unit has worked well for the company in processing C&D, he says, but is very limited in the number of tons it can do per hour. "The starscreens at our other operation are capable of doing a whole lot more."
That plant has three Lubo starscreens, virtually one right after the other. The first one scalps off 8-inch minus, the second takes the 2-inch, and by the time the third one gets the 1/2-inch minus, the material has also been through two picking stations.
Hammer likes the quality of product he gets from the screens, but cautions that when using a star as the primary screen, one must do presorting to remove long, stringy materials that can wrap around the stars. "Otherwise, you are constantly cleaning," he says.
A brief presort should be done, according to Ray Kvedaras of Cooper Tank Transfer in Brooklyn, N.Y. He advocates using a grapple to pull out heavy metal and garbage.
Hammer agrees, adding that for presorting to be economically viable, "you have to be careful and do it efficiently, as the margins are thin in this industry."
However, at Cooper Tank Transfer, Kvedaras uses a General Kinematics fingerscreen as the first screen because of the question of wrapping. His company operates on a little more than an acre and processes 1,500 tons per day, so there is no room for pre-sorting.
The operation mostly makes ADC. For its second screen Cooper Tank Transfer has the Bezner "bucket" screen, a simple unit from Europe that is rarely seen here. Kvedaras says he got the screen as part of an old sorting system the company picked up some time ago. However, he says he would consider having a starscreen as the second part of the processing line because that type of screen can really provide a much finer cut. "Also, you don’t have to allow room for an inclined unit." Kvedaras says, which is very important when working in confined quarters.
He thinks that the product being made isn’t as important as the density of the material coming into the plant. "Most screen manufacturers gauge production with tonnage. This is the most deceiving myth to people who don’t understand densities," Kvedaras says. "Mixed C&D waste could range from 400 pounds per yard to 800 pounds per yard. So ask the manufacturer what density their production rate is based on and get the rate in yards per hour. For C&D you should get the heaviest screen you can get."
He also believes that C&D recyclers need to screen more than once to make good products. "Two is good, three is best," he says.
Three mechanized screening stations are part of Waterway Materials’ two-line recycling plant in Chesapeake, Va.—star, air separation and float tank, in that order. Jimmy Sissons says that the screens are part of a total design system. Even before the material hits the starscreen, the C&D material has been through a presort where the excavator operators are pulling out oversized steel and concrete, long wire, couches, mattresses and the like before the remainder is fed into a pre-grinder to be brought down to a 2-foot-minus. After the pre-grinder another manual presort removes textiles and plastics. Then a Machinex starscreen removes the 1-1/2-inch minus material that is stacked for use as ADC. "The starscreens are good at getting out fines from wet material because all that bouncing and jiggling will loosen up the material," Sisson says.
The air separation and float tank are used in tandem to remove heavy products, mostly aggregates that can be crushed by the company’s crushing plant. Wood for hog fuel and a mulch filler should be left, Sissons says.
What is an even more important screening technique, Sisson says, is to control the inflow of material into the plant. "When we started looking at systems we heard that you never know what you are going to get in the C&D waste stream, and to a degree that is true," he says. "But you can control that change with a relatively narrow bandwidth that will allow you to run the plant at an optimum rate."
ALL WET. One piece of equipment that many of the operators interviewed disagreed on was the float tank, a device that separates the heavies from the light materials using water. Hammer of Downtown Diversion considered putting one in when installing the larger recycling plant, but hesitated because of concerns about regulators and stormwater. However, his company is looking at the newest float tank designs and may still install one.
New Bedford has a float tank installed in the line, but it is not in use currently because of the problems it caused. Leech says he is stubborn and plans on figuring out how to make it work the way it should.
Waterway lives up to its name by using a water tank, but Sissons does admit to those units being the biggest maintenance item the processing line has. "Even though the starscreen works well at getting out fines, there still is some in there that becomes sediment in the tank. We have much more maintenance of that part of the system than what we expected or want."
What C&D recyclers should want from their screening equipment is efficient operation with relatively low and easy maintenance and the ability to separate the materials they can sell. Good screening equipment can tremendously improve an operation’s recovery rate while helping to keep down the need for pickers. There may never be a way to remove the human part of the sorting equation, but these types of screens can limit the amount spent on human labor.
This feature originally ran in Construction and Demolition Recycling. The author is associate publisher of Construction & Demolition Recycling and executive director of the Construction Materials Recycling Association (CMRA). He can be reached at turley@cdrecycling.org.
Get curated news on YOUR industry.
Enter your email to receive our newsletters.
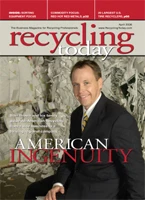
Explore the April 2006 Issue
Check out more from this issue and find your next story to read.
Latest from Recycling Today
- Astera runs into NIMBY concerns in Colorado
- ReMA opposes European efforts seeking export restrictions for recyclables
- Fresh Perspective: Raj Bagaria
- Saica announces plans for second US site
- Update: Novelis produces first aluminum coil made fully from recycled end-of-life automotive scrap
- Aimplas doubles online course offerings
- Radius to be acquired by Toyota subsidiary
- Algoma EAF to start in April