I
n with the new, out with the old. A reversal of an old adage isperhaps the best way to describe the increased demand for America’s scrap metals. The world’s hunger for new cars, appliances and buildings was a boon for steel makers in 2004. Global steel production exceeded 1 billion tons last year, a record amount. And as the need for "new" steel products increases, the output volume—and price—of processed scrap metal has soared.
To keep up with the high demand, leaders in the scrap industry are investing in new processing equipment.
A scrap metal recycler in the Southeast recently unveiled a new state-of-the-art shredder. The new 7,000-hp shredder processes cars and other ferrous scrap.
The size and volume of the downstream run of scrap coming off the new shredder required a high-volume ferrous metal separator. The company turned to Eriez Magnetics of Erie, Pa.
SCRAP RECOVERY. Magnetic equipment is used to recover ferrous and nonferrous metals from automobile shredder streams, as welll as from solid waste, electronic/computer scrap and bottom ash.
Three common magnet technologies are used in ferrous scrap recovery: drum, belt and pulley magnets. Downstream from auto shredders, the most effective systems will use a combination of two or even all three configurations to effectively separate ferrous scrap from the other material that is present.
It’s important that the processor understand that each of the top three magnet configurations is designed for certain applications. However, drum magnets require material to be shredded thoroughly, and it was an innovative drum magnet solution that was needed for this particular application.
Drum magnets are positioned so that material cascades over a rotating shell of a stationary drum. Inside the drum, a magnetic element projects a field within a certain arc, carrying the ferrous material past a splitter and enabling it to drop the material on the opposite side. Cleats on the outer shell of the drum aid in moving the material.
A DIFFERENT DRUM. Simply said, drum magnets can improve ferrous recovery and they also clean the ferrous, improving purity and grade.
However, a wide variety of diameters, widths and magnetic strengths are available to provide the desired capacity and degree of separation at the lowest possible cost.
The drum magnet specified for the super-shredder was an electro-agitator type, which uses a deep-field, rectangular-core pickup magnet to reach out and grab the ferrous, and a second rectangular-core agitator magnet to flip or agitate the ferrous material, cleaning it of contaminants like loose mud, paper, fluff and trash.
A double-drum scheme with counter rotation (see illustration above) provided maximum cleaning without secondary shredding or air classification, according to Eriez. In this configuration, the first drum, suspended above the primary feed conveyor, picks up ferrous material from the waste and carries it up and over the top to the intermediate conveyor section. The bulk of the non-magnetic material falls to a take-away conveyor located below the primary separator. Vibratory shakers are often used instead of belt conveyors.
Both drums rotate in a direction opposite to the material flow, helping to ensure that there is no jamming or bridging. Clean metal with a minimum of non-magnetic material is deposited on the ferrous conveyor.
"We recommended the two drum configuration because of the efficiency of the process," says Al Gedgaudas, a resource recovery market manager with Eriez Magnetics. "The electro-agitator type attracts ferrous from a distance of 15 inches to the internal primary magnet pole, then flips the ferrous as it goes to the secondary agitator magnet pole. A bleed-off pole helps release and discharge the ferrous. The flipping cleans the ferrous or ‘frag’," he says. Using a vibratory shaker under the drum magnets also helps release trapped nonmetallic trash.
The recycling operation’s two Eriez 60-inch diameter by 96-inch overall width electro-agitator drum magnets were installed over a 96-inch-wide vibratory shaker. Custom built for this width, they are some of the largest drums used in shredder yards today. The especially wide magnetic field pulls ferrous from the edges of the shaker tray, improving purity in the downstream product run.
In addition to the larger width of the drum magnets, Eriez recommended additional customization, as well, Gedgaudas says. "We worked with the client on custom drum wipers. The unique wipers were 2-inches high and 1-inch thick; the total thickness of the drum shell is ¾ inches. The more substantial shell and wipers would increase durability over the long haul," he explains.
Eriez details a few of the standard benefits to such a drum solution.
Working Overtime |
For a list of auto shredders in operation throughout the United States, visit Recycling Today online. |
"Our drum shell, which contacts the ferrous material, is made of heavy manganese steel and is abrasion resistant for extended operating life," Gedgaudas says. "Plus, our coil-system is warranted for three years."
Another benefit is that drum separators are completely enclosed; there is no possibility of pieces of iron jamming internally and stopping their operation. Outdoor installation with exposure to the weather presents no problems, according to Eriez.
Finally, Gedgaudas says, drum magnets are easy to maintain. There is no scheduled maintenance on the drum separators other than the occasional lubrication of two heavy duty bearings and the optional drive chain."
The installation, now in operation for more than two years, has been a great success, thanks in part to the reliability of the custom-built separation equipment provided by the magnet supplier. High volume and high purity combined to meet the market’s high demand.
This article was submitted by Stevens Baron Communications on behalf of Eriez Magnetics of Erie, Pa.
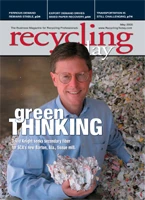
Explore the May 2005 Issue
Check out more from this issue and find your next story to read.
Latest from Recycling Today
- Nucor receives West Virginia funding assist
- Ferrous market ends 2024 in familiar rut
- Aqua Metals secures $1.5M loan, reports operational strides
- AF&PA urges veto of NY bill
- Aluminum Association includes recycling among 2025 policy priorities
- AISI applauds waterways spending bill
- Lux Research questions hydrogen’s transportation role
- Sonoco selling thermoformed, flexible packaging business to Toppan for $1.8B