Designing an effective mixed C&D debris processing system should start with market demand and work backward, determining the number and variety of screens needed to produce the desired product mix. Establishing acceptable cleanliness levels and product sizing requirements are essential in creating a capable and efficient system, those in the screening equipment business concur.

"That’s the most important thing," Bryan Sinram, vice president of Sherbrooke OEM, Sherbrooke, Quebec, Canada, says about the role of market conditions in determining screening needs. "You actually build the system backward, meaning you design the system for the products that are marketable in the area."
Sherbrooke designs and manufactures turnkey C&D recycling systems and conveyors for various industrial and environmental applications. Adds Sinram, "Also, the system has to be able to absorb any changes in the product market."
Scott Jable of Lubo USA, which is headquartered in Stamford, Conn., says speed and volume are also important considerations. Lubo USA is the North American and Canadian distributor of Lubo Recycling Equipment, which is based in the Netherlands. Lubo manufactures star screens, mobile screeners and complete systems for C&D recycling.
Bruno Lagace, application engineer manager for Erin Screens, Portland, Maine, stresses that weight removal is a factor. "When you get C&D in, you want to take as much weight out of the product as possible," Lagace says. "It is critical that your screening equipment does a good job for that."
Erin Systems provides mobile and fixed screening systems and complete fixed C&D recycling systems.
In addition to weight removal, primary screening serves to divide the stream into two different sizes, facilitating further processing.
OF PRIMARY IMPORTANCE. "Sometimes you want to have two lines: An overs picking line and a medium picking line," Lagace says. " Using a screener, material from 6-inches to 8-inches can be sorted into an overs line, with material measuring from 2-inches to 6-inches comprising the medium line, he says.
Jable says that once material has been screened into streams of two different sizes, one stream may be manually picked while the second may undergo additional automated processing.
"[With] the smaller material that falls through, you might be able to use more automation on that particular line," Jable says. "The bigger the gap of the screen, then the less you have going over to the manual picking area, so the faster you can process and the more accurately you can pick. By being able to get a wider gap," he says, "you are able to get more speed and more accuracy from your manual pickers on the overs line."
Tim Griffing of Continental Biomass Industries (CBI), Newton, N.H., adds that primary screening "cuts the volumes down to make the pickers more efficient" by eliminating dirt and dust.
CBI manufactures a pre-screener that divides material into three streams: fines, ferrous metals and overs.
FROM HERE TO THERE |
Conveyors serve to move material and to connect the whole mixed C&D debris processing system. Conveyors also contribute to the effectiveness of the screening equipment based on the manner in which they present material to the screens. Sherbrooke OEM, Sherbrooke, Quebec, manufactures an apron conveyor. Bryan Sinram, Sherbrooke’s vice president, says its all-steel apron conveyor is used in loading and infeed applications. Sorting conveyors then spread the material out, enabling manual pickers to sort through the material more easily. "The big thing, too, is how you present the material to the sorter," Sinram says. "You don’t want to present it 2-feet thick and all tangled together. The sorting conveyors are usually run with a variable frequency drive, so it [can be operated at] a variable speed, so you get a better spread of the material," he says. "Conveyors are really just for moving the product," Tim Griffing of Continental Biomass, Newton, N. H., says. "The only sorting can be done across a picking table." He adds that conveyors are the least expensive item in a mixed C&D processing system and that they can be modified easily with a torch and welder to accommodate other system adaptations. Hugh Fagan of DoppstadtUS, Haslett, Mich., says chain conveyors are "pretty efficient" in mixed C&D applications, though standard belt conveyors are common. Regardless of the specific type of conveyor used, its durability is critical. "You need to look at things like the thickness of the steel and the type of belt that’s used," Scott Jable of Lubo USA, Stamford, Conn., says. "It’s got to be some of the thicker steel out there and the better belts, maybe a five-ply belt, just because the material that you’re dropping on it is so difficult." |
Hugh Fagan, sales manager for DoppstadtUS, Haslett, Mich., says that primary shredding of C&D waste prior to entering a picking line can be emphasized sometimes instead of primary screening. "The reason for primary shredding is that C&D is generally a very un-uniform material," he says. "It’s very hard to convey and control; whereas, if you can screen it, it certainly helps. If you can shred the material to 10-inch or 12-inch minus at the start of a system, it makes the system very manageable," Fagan says.
DoppstadtUS is the North American distributor for Doppstadt, a German manufacturer of size-reduction, conveying and screening equipment.
Sinram says that controllable sizing, such as running material over with a track machine or breaking it down with a grapple bucket, is a step that can be used prior to primary screening.
SIFTING THROUGH THE SCREENS. A variety of screens are available for sorting mixed C&D debris, including trommel screens, disc and star screens, finger screens and vibratory screens.
Sinram says each screen has its strengths. "It probably depends on where you place these screens in the system," he says. "All these screens would be effective after you’ve had some type of sizing."
Trommels have both detractors and supporters. Jable says, "Trommels have been widely used, but not terribly effectively." He says trammels have a limited capacity and a tendency to jam. "And to change screen size, you have to change the entire cylinder of the trommel. For instance, if you are doing 6-inch minus today, and you want to do 3-inch minus tomorrow, you have to remove all the screens that are on the trommel and put different ones on," he says.
Griffing of CBI says, "Trommels are fading away out of C&D because of wear and tear. And it rolls the product into a bundle, and it’s hard to pick, hard to sort."
Fagan, on the other hand, says, "The best units for screening C&D as a primary screen is still a trommel screen. With a trommel, you take impact loading and you make a very specific product," he says. "A trommel is still the most efficient screen in C&D by far in my estimation."
A finger screen is comprised of vibrating rods or "fingers" placed at a downward angle. Jable says the fingers oscillating effect causes smaller particles to fall through the screen, while the larger particles remain on top.
Lagace says that finger screens are basically shaker boxes. Among the benefits of an Erin finger screen is its ability to direct load, so material is fed directly onto the screen as opposed to using a hopper.
"The machine is really rugged, which is a really important factor," Lagace says. "The simplicity is really important. Because you have so few moving parts, [there is] less maintenance, less breakdown."
Jable says, "Some people use a vibratory screen with specific-size holes in it, but that’s very rare these days because those tend to clog very easily because of the fixed hole and have a limited capacity." He adds, "Things like slot screens or fixed-hole screens work fine on homogeneous material," but he claims they are not as effective with mixed C&D debris.
Star screens are comprised of rotating rubber stars that allow fines to fall through and larger material to be carried across the screen.
A star screen has "an incredible capacity, because it’s a very dynamic screen," Jable says. "The stars are constantly in motion, and it really helps to move the material quickly over it." Jable says the motion of the star screen also serves to help break up material. In addition, he says, the gapping of a star screen can be adjusted simply by changing the speed of the stars’ rotation.
"For instance, if you run the variable speed drives all the way up, you may get 12-inch minus material falling through," Jable says. "But now you decide you need a little bit more to fall through. All you have to do is lower the rotation speed of the stars, and it allows more material to fall through." He adds, "By the way, that doesn’t affect throughput."
Jable points out that star screens are susceptible to material wrapping around the axles, and he suggests pre-sorting to remove long, stringy material as well as taking 15 minutes or so each day to clean the screen.
Disc screens are similar to star screens, although the more rounded rotating rubber wheels do not necessarily propel material forward as fast or break it up.
Sponsored Content
Labor that Works
With 25 years of experience, Leadpoint delivers cost-effective workforce solutions tailored to your needs. We handle the recruiting, hiring, training, and onboarding to deliver stable, productive, and safety-focused teams. Our commitment to safety and quality ensures peace of mind with a reliable workforce that helps you achieve your goals.
Griffing says that star screens and disc screens, though they are capable of handling high volumes of material, are not very good at spec sizing. "The gap between the stars or the discs allows elongated pieces to fall through. If you want a 3-inch product, yes, it can be 3-inches by 3-inches or 3-inches by 2-feet long," he says.
"Using a disc or star screen, the material must be picked prior to screening," Griffing adds concerning the tendency for material such as wire, rope and cable to wind themselves around the discs or stars.
Vibratory screens are available in either balanced or centrifugal varieties. "The balanced has an aggressive action without vibration to the foundation at low frequencies," Griffing says. "Centrifugal is done with a centrifugal weight and creates a higher frequency, lower vibration. Balanced can be turned on and off on demand by the pickers," he says.
Says Griffing, "The balanced screens can handle any raw C&D. I say raw as in it hasn’t been pre-picked or pre-crushed or anything."
IT’S IN THE MANUAL. Regardless of the strengths of the various screens, manual picking stations remain a necessity when processing mixed C&D material.
"At this stage in C&D picking technology," Jable says, "it’s not really possible to make clean, homogeneous – and that’s truly the key word – homogenous automated end products. You can get close, but manual intervention is still necessary."
Jable adds, "There are a lot of devices that certainly can help. Air systems can get out the light materials. Magnets get out the ferrous metals. Eddy currents can get out the nonferrous metals. Float tanks can float wood and have aggregate sink to the bottom so you can separate those two automatically.
"We’re getting close, but there’s still really no way to do it without manual sorting," Jable says. "The idea, though, is to keep manual sorting at a minimum since that’s where most of your cost goes."
"Even when some things are taken out automatically, you still need quality control," Sinram says.
Griffing says that screening takes out the fines and separates the mixed C&D stream by size, not by identity. "You do have to pick or sort through recyclables," he says.
Screening enables efficient picking, however, by removing the fines and dividing the materials into two streams.
"The screen is the most important part of any C&D system," Jable says. "It needs to be fast, accurate. It needs to keep running. Anytime you have to un-jam a screen, your throughput is zero. You really want to look at the different options of screens carefully to make sure the one you’re picking is right for your particular application."
Griffing agrees. "The screener is crucial as it is one of the mainstays of the whole system, it’s a primary component. Keeping it running is crucial to most C&D facility designs."
The author is assistant editor of Recyclng Today and can be contacted via e-mail at dtoto@RecyclingToday.com.
Get curated news on YOUR industry.
Enter your email to receive our newsletters.
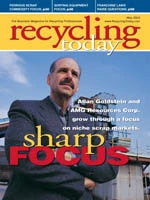
Explore the May 2003 Issue
Check out more from this issue and find your next story to read.
Latest from Recycling Today
- Returpack reports increased DRS activity in Sweden
- Trade groups align against European export restrictions
- Construction, auto sectors show mixed signals
- Politics in Turkey threaten recycled steel outlet
- Toppoint Holdings expands chassis fleet
- Lego creates miniature tire recycling market
- Lux Research webinar examines chemical recycling timetables
- Plastics producer tracks pulse of wire recycling market