For the past several years I have been monitoring, from my European perspective, the evolution of trends and thinking of U.S. car shredder operators concerning their post-shredder systems.

The European perspective is characterized by a strong tradition for going to the bitter end of reclaiming all possible marketable material from any scrap source (in Europe, raw materials are often more expensive and rare than in the U.S.) Tipping fees for residue that on average are significantly higher than in the U.S. also affect the European perspective.
Scrap processors typically look to achieve a target rate close to the maximum marketable material that can be reclaimed out of their scrap before process costs associated with that result become burdensome.
It would be my contention that magnetic separators (both ferrous and eddy current) enjoy the premium for the best ratio between cost (up-front and operating) and throughput capacity, compared to many other sorting solutions, such as hand pickers, heavy media plants, metal sensors, furnaces.
It is important, then, to look for innovative magnetic solutions that can optimize the yield of this low-cost and high-productivity technology prior to possibly further processing the material through more expensive cleaning or/and sorting processes.
Innovative magnetic separators offer the possibility and convenience of reclaiming more from scrap (resulting in more selling opportunities) while also lowering landfill costs.
OPEN MINDS. The recent 2003 ISRI show in Orlando was an occasion to see that, as never before, U.S. scrap processors are focused on getting more from their scrap and open to listening to innovative solutions that address that focus.
It is therefore also the right moment for the manufactures of magnetic separators to show that magnets are not that technological "black box" too often perceived as a commodity for which the limits in performance are set and known.
It is typically at the exit of the car shredder that you find the first magnetic process with the presence of one, two or three electro-magnetic drums (usually with diameters ranging from 48 to 60 inches) placed a row to serve two purposes: 1) to collect the ferrous portion of the stream, and; 2) to clean (or liberate) the ferrous from the nonferrous material dragged along with it. This is the reason why those drums are often called "agitator drums".
The performance of both the drum separators themselves and the design of their assembly is very straightforward and can be assessed by analyzing the resulting materials.
1) Collection of ferrous: Check the auto shredder residue (ASR), or fluff, examining, the size and shape of the ferrous pieces missed by the drum(s). The larger the size and less spherical the pieces of ferrous material found, the larger the quantity is likely to be.
2) Cleaning of the ferrous: The purpose of the first drum is to pick up the maximum possible ferrous portion of the shredded material (typically around 70%). Therefore it is normal that this first drum carries some nonferrous material along with the ferrous. The liberation of the nonferrous carried along by the first drum is mainly the purpose of the second (and third) drum(s). The first drum must be strong enough to attract almost all the ferrous from your material while the second (and third) drums must be sufficiently strong so they can be placed in suitably high and distant position from the in-feed conveyor, thus leaving room for the nonferrous to drop and at the same time not lose the ferrous.
When drums two (and three) are not magnetically strong enough to perform a good liberation of the nonferrous, they are often used by operators unsuitably, acting more as excavators than magnetic separators. In these cases, they are carrying indiscriminately with their cleats both ferrous and nonferrous material. They are often placed too close and low with regards to the infeed conveyor, leaving minimum possibilities for the nonferrous portion to drop.
Indications of drums performing well are when your ferrous shred grade is clean and, at the same time, you do not find the typical small spherical ferrous pieces of engine blocks in your fluff that should have been part of your ferrous grade. The ferrous missed by these drums that is found in your fluff will be very small and/or attached to larger pieces of non-ferrous (possibly subject to other specific magnetic sorting solutions later on).
FURTHER STEPS. Often operators rely on additional ferrous separators (typically belt magnets and head pulleys) placed on their downstream fluff line to make up for what their agitator drums have missed. We must not forget that these belt magnet and head pulley separators will encounter much smaller magnetic masses than the drums, and therefore they can only magnetically grab what crosses their magnetic field in much better distance conditions than on the drums.
The head pulleys can thus address the lower part of the fluff burden running on the transfer belt conveyor while the belt magnets reach for the larger pieces of ferrous running on the upper part of the fluff burden.
Small pieces of ferrous coming from the engine blocks—shattered apart during the shredding process—are difficult to grab by the smaller ferrous separators, and therefore end up in the fines. This represents a loss of ferrous earnings for the scrap operators who dispose of their fines fraction. It also causes problems for the ones who process them on further specific eddy current separators (more on this later).
Despite the fact that, from the outside, agitator drums do not seem to have changed since they first appeared along with the first shredders, the latest generations can guarantee optimum cleaning quality and ferrous recovery rates. These drums have become so strong that their outside shells have had to become thicker and thicker to mechanically withstand the impact shocks of the larger pieces of ferrous metal hurtling toward them. The result can be that the ferrous portion will not require any further mechanical sorting attention.
The next magnetic stages are the ones related to reclaiming the valuable nonferrous metal fraction from the fluff.
In this case, ideas have gone a long way ahead since the time where the performance of an eddy current separator was supposed to be gauged on the maximum length of the jump that a piece of aluminium could achieve, or by the gauss reading that could be measured on the shell of the rotor.
Gauss reading value is a representative measure of the performance (force) of a lifting magnet but is not always valid for magnetic separators. Unlike with lifting magnets, the purpose of magnetism for separating is not to anchor a load firmly, but to induce a motion into material (attraction for the ferrous and repulsion for the nonferrous), that has more to do with magnetic gradient and suitable frequency.
SOMETHING INNOVATIVE |
Innovative Recycling Systems, Solon, Ohio, has introduced what it is calling a magnetic innovation for ferrous separation. According to the company’s Paul Popovich, the system still uses three rotating drum magnets with axial pole design, but includes only one feed pan. "We are using gravity to help separate the ferrous product, instead of fighting gravity," says Popovich. "Up to now, magnetic separation systems have used the magnets to lift the ferrous product up from a pan feeder or conveyor and leave the waste and nonferrous product below," Popovich adds. "This use has a few basic design flaws. By lifting the ferrous material, material that is only slightly magnetic, or large dense pieces of ferrous, are dropped by the magnets and must be captured later." Popovich notes that in this configuration, as mixed material falls from the pan, the magnet pulls the ferrous product sideways instead of lifting it vertically. "Even slightly magnetic, or heavy dense pieces, can be deflected sideways to the magnet," he remarks. With a wider gap between the magnet and pan edge is greater, material is free falling with no rolling of material, he claims. "After all three magnets, the ferrous product is clean and passes onto a picking conveyor for hand picking copper or any entrapped waste. All of the waste and nonferrous metals is collected in a single hopper and is taken away by a conveyor for further eddy current separation." Popovich says the layout also uses less equipment, which reduces the initial cost and also reduces maintenance and operating costs continuously. —Brian Taylor |
As far as the jumping capacity of the nonferrous metals is concerned, the performance of an eddy is much better represented by the percentage rate of the nonferrous pieces that manage to jump the splitter than by the maximum jump length that large pieces of aluminum can achieve. (To get a clean fraction of aluminium further apart from your reclaimed mix of non-ferrous metals, it is always possible to provide the hopper of your eddy current separator with a double splitter).
EDDY ADVANCES. The latest generation of eddy current separators are trying to achieve two primary goals: a maximum recovery rate of nonferrous metals and the ability to seek out differently-sized material to separate.
A trommel screen often placed before an eddy current sorts out three fractions: A first fraction represented by the fines, typically below 3/8-inch or ½-inch in size; a second fraction (often cleaner, since much of the dirt goes into the fines) going up to six inches in size; and a third fraction made of the oversize materials measuring more than six inches in any one dimension.
But the latest generation of eddy current separators feature magnetic circuits suitable to cover material sizes ranging from 3/8-inches to six inches, and do not require that the standard material size fraction be further split into different sub-fraction sizes that would necessitate either different eddy current separator lines or for these different fractions to pass in different batches on the same machine with different settings.
The productivity and universality of the latest generation of eddy current separators is achieved through advanced magnetic circuits as well as from higher magnetic frequencies.
One way to assess the performance of an eddy current process on fluff is to send samples of material to magnet manufactures for trials on their latest eddy current models. If the result obtained from the passage on a new eddy is significantly higher than any of the ones achievable through existing equipment, a processor has reason to calculate the possible return on an investment in a new eddy.
Until not so long ago, the fines fraction of the fluff was disregarded and disposed of by many shredder operators. But there are now several reasons to reconsider the situation.
One possible reason is the traditional underestimation of the content of nonferrous metals in the fines stream. Many shredder operators estimated their nonferrous percentage at around 2 to 3 percent, which made it economically unfeasible to seek further recovery. But results achieved by newer eddy separators on car shredder fines show that the metals content can be as high as 10 to 25 percent, mainly made up of small pieces of aluminium coming from engine blocks that have been shattered apart during the shredding process.
Fines often include a lot of dirt and dust, making them difficult to process. The presence of excessive dirt and dust in the reclaimed mix of nonferrous metals creates a very low-value commodity. But the latest eddy current processes for fines include a de-dusting stage.
For those who have not checked for the past several years, there is still a lot to get from that affordable and productive "black box" that is magnetism.
The author is managing director of SGM Magnetics Corp. and can be contacted via e-mail at didier.Haegelsteen@SGM-magnetics.com.
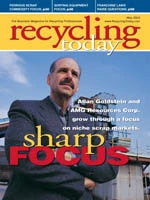
Explore the May 2003 Issue
Check out more from this issue and find your next story to read.
Latest from Recycling Today
- ReMA opposes European efforts seeking export restrictions for recyclables
- Fresh Perspective: Raj Bagaria
- Saica announces plans for second US site
- Update: Novelis produces first aluminum coil made fully from recycled end-of-life automotive scrap
- Aimplas doubles online course offerings
- Radius to be acquired by Toyota subsidiary
- Algoma EAF to start in April
- Erema sees strong demand for high-volume PET systems