The automation of sorting and separating functions at materials recovery facilities (MRFs) has been underway for a number of years now. The trend is by no means abating, with one of the highest-volume MRF operators—Waste Management Inc., Houston—having recently retro-fitted several of its MRFs with automated single-stream systems.
The trend has been met with opposition by some recyclers, some of whom believe that automated systems cannot separate materials as thoroughly as trained sorters.
It may indeed be several more years before the full effects of the switch to automation can be measured. Ultimately, paper mills and other consumers of curbside recyclables will have the final say.
In the meantime, most recyclers remain on track to not only run with their current automatic sorting equipment, but also to shop for additional innovations.

FRAGILE GLASS. "It varies from operator to operator, but companies are continuing to recognize the value in spending money on capital equipment instead of labor," says Scott Jable, who manages the Chicago office of equipment distributor Van Dyk Baler Corp.
That judgment toward equipment and away from labor has manifested itself in the single-stream system now being used by many haulers and processors.
In an article written for Recycling Today two years ago, Bob Marshall of Machinex Industries Inc. defined the single-stream system as one that handles "a recyclable mixture containing both fibers and containers commingled in the same stream."
There are several companies in North America, Van Dyk Baler and Machinex included, selling equipment and MRF layout services to recyclers who have jumped into the single-stream pond.
Jable says the relative youth of the single-stream process means recyclers are still very much willing to tinker with the process to increase throughput and create the cleanest possible grades of materials.
"People are still exploring, I think, once they get a container stream, just what is the best thing to do with that stream," he notes.
The glass container stream is often pointed to as the problem child in single-stream set-ups. Newsprint mills and other consumers do not want broken pieces of glass in their incoming stream.
Some equipment available acts to separate out the glass before it breaks. Machinex’s Marshall says his company offers "technology that drastically reduces glass breakage while improving flat/round separation."
Van Dyk, on the other hand, offers a device called a glass breaking screen that goes toward the very front end of a MRF process. The device "breaks the glass on purpose to get it out of the stream, letting it drop down through a screen to make a mixed broken cullet."
This method has proven popular in areas where there is not a nearby furnace for clean cullet anyhow. The mixed cullet may be used as a lower value aggregate, but at least it is kept away from the marketed paper grades.
In some cases, municipal recycling programs are dropping glass altogether, concluding that the material causes more problems in the recycling process than it is worth.
PASSING GRADES. Many of the same programs have been dropping glass have been adding to the number of paper grades they will accept in the recycling bin.
In some cases, the new pulping technology being used at paper mills has helped recyclers broaden the types of paper they can accept without adding to their separating capabilities.
Jable notes, for instance, that very few recycling plants are separating magazines from the old newspapers (ONP) grade, since the "new pulpers don’t mind the magazines."
But there remains a desire to separate low grades, such as old cardboard containers (OCC), from high grades, such as ONP. And certainly, the need to separate containers from fiber and to remove contaminants from both streams remains.
MRF operators differ on their need to install an OCC separator at the front of their system, says Jable. "Some customers see the value, some don’t," he remarks. "If you use an OCC screen, it’s only a size sort. It will remove the big pieces of corrugated, allowing news and smaller corrugated to fall through. That means somewhere down the stream, you still have to separate the small corrugated."
He adds that some MRF operators with as much as 15 percent of their incoming fiber consisting of OCC will benefit from using the screens, while others with a more typical seven percent to nine percent OCC rate may not accomplish as much using the screen.
A center point of discussion concerning single-stream MRFs has involved complaints from newspaper mills that these facilities cannot produce high-quality news grades for their consumption.
In a 2002 Paper Recycling Conference presentation reprinted in the August 2002 issue of Recycling Today, Dr. James Burke of SP Newsprint Co., Dublin, Ga., declared, "We shouldn’t rush to mix all fiber streams together. The more mixed the stream, the more difficult to separate, and the higher the likelihood of cross-contamination."
Despite this reluctance, Jable was pleased to note that SP Newsprint had enough confidence in Van Dyk’s single-stream abilities to purchase a system from Van Dyk for its own recycling plant. "Like any system, it has to be designed, installed and operated properly," says Jable. "But if it is, there is absolutely no reason why a good, clean number eight news grade should not come out of that system. We have had very good results, as far as mills being happy with the cleanliness of the product."
A PROFITABLE ENDEAVOR. Purchasing automated systems requires faith by the MRF operator that the equipment will pay for itself over a number of years.
Machinex’s Marshall points out that savings can be achieved in several ways. "Older single-stream MRFs required much higher staffing levels to work the sorting lines," he notes in regard to the potential for labor savings.
While new screens may save labor costs, to do so over time they will have to be part of a system designed for flexibility, Marshall adds. "Separator screens need to be designed with built-in flexibility to allow for changes in product and climatic conditions. Separators with limited adjustment will be constantly challenged to produce quality results because of the product and climate change. Features such as variable angle screen decks, easily adjustable replaceable split discs and variable speed drives play an important role in the efficiency of the separator," Marshall wrote for his earlier Recycling Today story.
In addition to being designed for flexibility, recyclers are also hopeful that the screens are being designed for longevity.
"The life of the equipment should be a selling point, because the buyers are always looking at what their payback will be," says Jable. "Because from a certain point on the machines become pure profit, they want to know how long a screen will last."
Unfortunately, many of the screens available are fairly new to the market, and so have only had a few years with which to establish a track record. Jable says the first OCC screen Van Dyk sold into North America has been on the job for about 10 years—and remains on the job.
"The stars or discs themselves that are used on the screen will wear over time and will need to be replaced, but the screens themselves should last a very long time," he notes.
WHAT NEXT? While screens are using size and density to separate materials, entrepreneurs have offered other mixed materials sorting techniques, such as the optical systems made by MSS Inc., Nashville, Tenn. MSS has created optical systems to separate glass by color; to separate plastics by resin type; and to separate colored from white fiber streams.
Most recently MSS Inc. and AST LLC, also of Nashville, have introduced a technology using opto-electronic sensors to identify and remove OCC and non-paper items (plastics, trash, etc.) from newspaper. The FiberSort machine is designed for MRFs that use manual labor to clean up newspaper coming off a mechanical screening system (OCC and ONP screens), according to Felix Hottenstein of MSS.
The FiberSort comes with a user-friendly touchscreen, a metal detector option and the possibility of two separate positive ejections (containers into one chute, OCC into another chute) from the main newspaper stream. The FiberSort has the potential of reducing the amount of manual labor by 70 percent while nor harming quality, according to Hottenstein.
One of the first FiberSort machines will be introduced in the U.K. in May of 2003, followed by two FiberSort machines that will be installed in the U.S. this June.
The author is editor of Recycling Today and can be contacted via e-mail at btaylor@RecyclingToday.com.
Get curated news on YOUR industry.
Enter your email to receive our newsletters.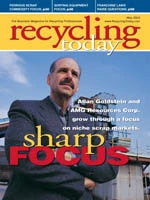
Explore the May 2003 Issue
Check out more from this issue and find your next story to read.
Latest from Recycling Today
- LumiCup offers single-use plastic alternative
- European project yields recycled-content ABS
- ICM to host colocated events in Shanghai
- Astera runs into NIMBY concerns in Colorado
- ReMA opposes European efforts seeking export restrictions for recyclables
- Fresh Perspective: Raj Bagaria
- Saica announces plans for second US site
- Update: Novelis produces first aluminum coil made fully from recycled end-of-life automotive scrap