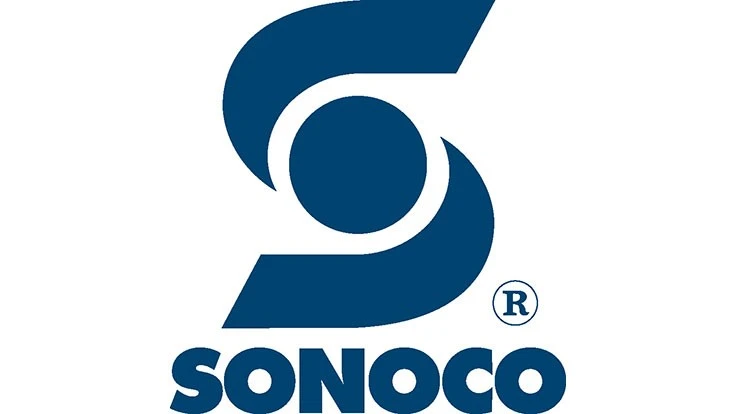
Photo courtesy of Sonoco
Sonoco has announced the new uncoated recycled paperboard (URB) No. 10 machine at its Hartsville, South Carolina, mill complex now is operational after being converted from a corrugated medium machine. The $125 million investment to update the machine previously was announced in April 2020 as part of the Hartsville-based packaging producer’s Project Horizon initiative.
“The machine was designed to be one of the largest and lowest-cost producers of URB in the world—paving the way for the future of our Hartsville paper mill complex and our global position as a high-quality URB provider,” Sonoco Chief Operating Officer Rodger Fuller says. “With the state-of-the-art capabilities, Sonoco is able to produce a wider range of high-value paper grades to serve our industrial and consumer converted products businesses and external trade customers.”
Sonoco procures nearly one-third of its U.S. and Canadian URB at the 100-year-old Hartsville facility, and according to the company, Project Horizon was initiated, in part, to ensure the long-tern viability and sustainability of the complex.
The launch of the URB No. 10 machine also marks Sonoco’s move to 100-percent-recycled fibers in Hartsville, eliminating the virgin pulp processing and chemical recovery operation at that facility. The company says the move to 100-percent-recycled fiber is expected to reduce electricity consumption, driving reductions in greenhouse gas emissions and total water use.
Previously, the No. 10 machine utilized 50 percent recycled and 50 percent virgin hardwood fibers to produce corrugated medium.
Sonoco projects the introduction of the new operation to drive $30 million in annual cost savings by 2024, and, as previously planned, the “less efficient” Nos. 1 and 9 cylinder machines will permanently be shut down by the end of October, reducing annual capacity by 70,000 tons.
“The startup of the No. 10 machine is an important milestone for Sonoco to demonstrate our ability to update and improve longstanding machines to meet changing market conditions and better serve our customers,” Fuller says. “We congratulate and thank the entire Sonoco team and our valuable suppliers for their efforts to execute this successful project.”
The machine will have a range of grade and caliper sizes, two offline slitter/rewinders to offer improved ribbon quality and precise, narrow-width slitting and lower variability across the machine width to create a more consistent product.
Project Horizon also includes other updates to the Hartsville complex:
- a new sitewide control system to promote a higher level of automation;
- a state-of-the-art cleaning system that creates more consistent paperboard; and
- modernized warehousing that allows for more efficient and safe handling of raw materials and finished goods.
Sonoco operates 23 paper mills globally with an annual capacity of 2.1 million tons, and the company says its new URB machine will be the world’s largest, with 500 tons of daily production capacity compared with its next largest machine, which has 300 tons per day of production.
Sponsored Content
Labor that Works
With 25 years of experience, Leadpoint delivers cost-effective workforce solutions tailored to your needs. We handle the recruiting, hiring, training, and onboarding to deliver stable, productive, and safety-focused teams. Our commitment to safety and quality ensures peace of mind with a reliable workforce that helps you achieve your goals.
The company operates 11 URB mills and 18 machines in South Carolina, Tennessee, Virginia, Massachusetts, Kansas, Wisconsin, California, Washington and Ontario.
Get curated news on YOUR industry.
Enter your email to receive our newsletters.
Latest from Recycling Today
- European project yields recycled-content ABS
- ICM to host co-located events in Shanghai
- Astera runs into NIMBY concerns in Colorado
- ReMA opposes European efforts seeking export restrictions for recyclables
- Fresh Perspective: Raj Bagaria
- Saica announces plans for second US site
- Update: Novelis produces first aluminum coil made fully from recycled end-of-life automotive scrap
- Aimplas doubles online course offerings