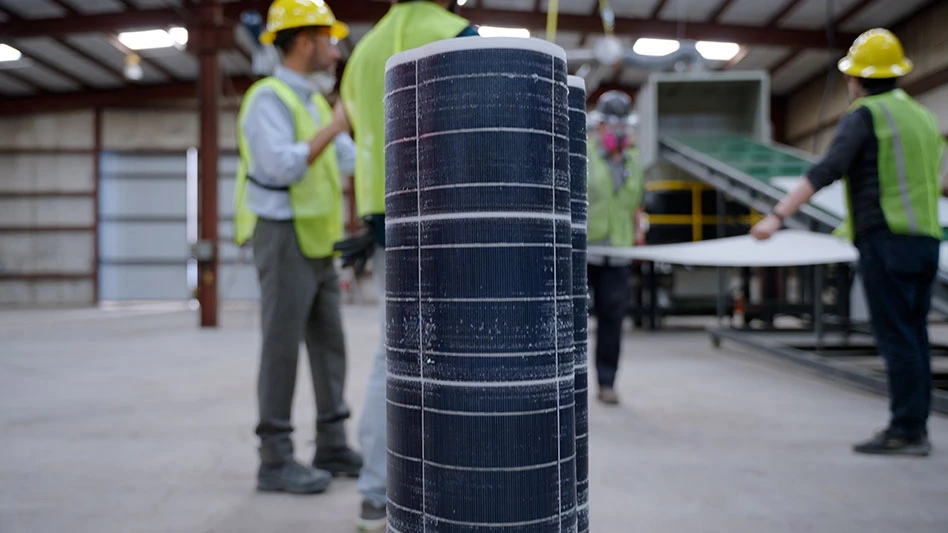
Photo courtesy of Solarcycle
The Solar Energy Industries Association (SEIA), Washington, has set a goal for solar to provide 30 percent of U.S. electricity generation by 2030. For that to happen, the U.S. will need to add nearly 125 gigawatts of solar power annually, the SEIA says, which will require building roughly 850 gigawatts of total capacity, an increase from 95 gigawatts at the end of 2020. In the eyes of one entrepreneur, creating circular domestic supply chains will be essential to scaling solar power.
“When I co-founded Solarcycle in 2022 alongside experts in sustainability and recycling, I knew the moment was right to build an industry-backed advanced technology solution to recycle solar panels that ensures that valuable materials go back into the domestic supply chain,” Suvi Sharma, co-founder and CEO of Solarcycle, says.

Prior to co-founding Solarcycle, which is headquartered in Oakland, California, Sharma spent nearly 20 years in the solar industry at Solaria and Nextracker. “Solar power is one of the most powerful tools we have to fight against climate change,” he says. Solarcycle's work seeks to further enhance the power of solar energy by bringing circularity to solar panel manufacturing.
“The current focus is for Solarcycle to return 95 percent of the value and 90 percent of the weight recovered from a solar panel to the domestic supply chain for the emerging solar manufacturing industry,” Sharma adds. “Our commitment is to get to zero waste and, in as many cases as possible, upcycle the materials rather than downcycle them.”
Solarcycle’s mission is to create value for the industry rather than simply extract it. “Recycling for Solarcycle is a means to an end,” Sharma says. “The end goal is to create a more scalable and sustainable solar industry, so that means advanced recycling is done not just to avoid waste but to obtain the feedstock materials needed for creating sustainable materials for the next generation of solar panels.”
RELATED: Solarcycle raises $30M | AES partners with Solarcycle
To assist with that mission, the company has developed a patented technology and a business model that puts its customers first. “At Solarcycle, we are very customer focused and engage comprehensively with them to provide an important service that has been lacking in the industry for some time,” he says.
A green wave
Last year, Solarcycle opened its first solar panel recycling facility on a 15-acre plot of land in Odessa, Texas. “Our company is on track to install the capacity to recycle 1 million solar panels per year by the end of 2023, and we plan to open a vertically integrated, advanced recycling factory capable of processing millions of panels annually in late 2024,” Sharma says.
By the end of the year, he says, Solarcycle expects to grow from 35 employees to approximately 100. The company also plans to increase the number of facilities it operates, “supporting a wave of green job growth in the recycling sector that provides good, family-sustaining jobs while positively impacting the environment,” Sharma adds.

Solarcycle
Solarcycle works with residential, commercial and industrial and utility companies and has formed partnerships with major solar companies, including Sunrun, Silicon Ranch, DPECOM Power, SOLV Energy, NovaSource, Greentech Renewables and Forum Energy Partners, to recycle decommissioned solar panels and to repair, refurbish and reuse solar systems.
He adds that partnerships are critical to Solarcycle’s success. The company works closely with solar developers; owners; engineering, procurement and construction firms; operations and maintenance providers; distributors; and manufacturers to ensure efficient collection and transportion of solar panels to Odessa.
“As part of that, solar panel manufacturers are an important partner since they are the ones that manufacture the solar panels,” Sharma says. “We are also beginning to engage with several large solar panel manufacturers now to develop plans to provide them with remanufactured materials, such as glass and aluminum, for the next generation of solar panels they will manufacture.
“Given the rapidly growing rate of solar panel production globally, there is an increasing demand for raw materials, like silver and copper,” Sharma says. “This high demand could also hinder supply chains and clean energy’s growth. For example, the world will use 20 percent of the current annual silver supply on solar production by 2027 and approximately 85 percent to 98 percent of the current global silver reserves through 2050.”
The Odessa plant can recycle solar panel components, including aluminum frames, other metals and glass, using tailormade equipment. “We are expanding our in-house technology to be able to produce pure products that are welcome in many different industries.,” Sharma says.
Returning materials to the production cycle
Solarcycle employees examine solar panels that arrive at the Odessa site to identify those that are suitable for reuse. “We have the capability to assess the power and durability of decommissioned panels and evaluate whether they can be used secondhand on-site by employing equipment used in the [photovoltaic] manufacturing industry.
“If a panel cannot be used secondhand and needs to be recycled, we use equipment that removes the aluminum frame,” Sharma continues, “and then it goes through an automated machine to remove the junction box. Next, it goes through a machine to remove the glass, and then the remaining panel is shredded.”
The shredded material is electrostatically separated to recover metals that include silver and copper, he says, and to separate the plastics.
Sharma says the construction of solar panels, which sandwich metals and glass together, makes extracting their constituent materials with a high level of purity challenging.
Solarcycle has developed and continues to refine specialized equipment and processes to take these panels apart using mechanical, electrical and chemical processes.
“Soon, we will be implementing additional processes to further purify our metals and add more value to our materials,” Sharma adds. “This will require additional innovation and capital investment, so for the moment Solarcycle sells the materials we obtain to vetted off-takers who meet high standards for worker safety and environmental controls.”
The large and bulky nature of solar panels provides another challenge in the recycling process that requires closely managing transportation and logistics costs. “At Solarcycle, we have optimized the packaging and transport of these panels from around the country to make it most cost-efficient,” Sharma says.

The company sells the aluminum it recovers within west Texas and the copper from the junction boxes and cables locally as well. Sharma says Solarcycle has some qualified buyers of glass near Texas. “Crucially, however, we are using part of our recent financing to build our own refining capacity on-site, at which point all of the materials will be sold domestically,” he adds.
While some electronics recyclers accept solar panels, Sharma says Solarcycle is different because it offers the solar industry a network of logistics providers to handle all logistics and shipping from warehouses, rooftops or fields; quick testing of the health of panels to determine the potential for reuse; a low-cost recycling process that can extract 95 percent of the materials from a panel, including glass, aluminum, silver, silicon and copper; and advanced environmental, social and governance, or ESG, reporting. “By recycling with Solarcycle, customers are taking advantage of the industry’s most advanced technology for recycling and reducing virgin mining and greenhouse gas emissions through the process,” he says. “We also have a transparent methodology and reporting, which gives our customers the net environmental benefits in tailored reports.
“In the past decade, solar has made great strides by becoming the dominant renewable energy source,” Sharma continues. “But scaling installations only is no longer enough. Engineers, lawmakers, entrepreneurs and investors must again come together to build a circular economy. We can do this by building recycling facilities nationwide and partnering with established solar asset holders and installers.”
A growing need
Approximately 500 million solar panels are installed in the United States, Sharma says. “And thanks to the Inflation Reduction Act and incentives for domestic manufacturing and installation, there will be 1 billion panels installed within the next five years.”
He says Solarcycle can be part of a domestic, circular economy for solar that allows Americans access to clean energy.
Sharma notes projections that indicate recyclables recovered from solar panels will be worth more than $2.7 billion by 2030, up from $170 million this year. “And the Department of Energy’s National Renewable Laboratory found that with modest government support, recycled materials can meet 30 to 50 percent of domestic solar manufacturing needs in the United States by 2040.
“In my view, solar panel recycling is no longer an afterthought to building a steady domestic clean energy supply: It’s an environmental necessity and an economic opportunity.”
Latest from Recycling Today
- Greenville, Mississippi, launches aluminum can recycling program
- Cotton Lives On kicks off 2025 recycling activities
- Georgia-Pacific names president of corrugated business
- Sev.en Global Investments completes acquisitions of Celsa Steel UK, Celsa Nordic
- Wisconsin Aluminum Foundry is a finalist for US manufacturing leadership award
- MetalX announces leadership appointments
- Sofidel agrees to purchase Royal Paper assets
- US Plastics Pact report charts expansion path for recycled content in packaging