
About six years ago, Smurfit Kappa Group, Dublin, Ireland, expanded its footprint in the United States after it acquired Orange County Container Group, Forney, Texas, for $340 million. Through that deal, Smurfit Kappa Group received eight packaging facilities, seven distribution centers in Mexico, seven wholly owned recycling centers in the southern U.S., two packaging facilities and a recycled containerboard mill in Forney.
Since that deal, the company has grown its presence in Texas and Arizona. It also has invested in its operations located along the border with Mexico.
Marty Rusk, Smurfit Kappa North America’s vice president of North America recycling operations, says the company has been growing its recycling efforts since the 2012 acquisition, too. Smurfit Kappa’s seven recycling centers are located in Arkansas, Oklahoma
The primary purpose of these recycling centers is to supply Smurfit Kappa’s Forney mill. However, he adds that the company’s recycling division has grown to supply other mills with recovered fiber.
“Our primary focus is to supply our mill, but we’ve grown because of our service record and our pay,” he says. “Other mills can trust the material we can support them with because we’re a mill-operated business. We preach the gospel of quality.”
Addressing contamination
Smurfit Kappa North America’s recycling centers tend to receive slightly cleaner incoming material than traditional material recovery facilities (MRFs). Rusk says the recycling centers receive mostly clean bulk corrugated material.
Although the company’s focus is on recovered fiber, he adds that Smurfit Kappa North America’s customers “wanted us to handle [plastics]. They wanted a one-stop shop recycling professional.”
By performing some sorting in-house at its recycling centers, Rusk says the company has more control over the recovered fiber that ends up at its mill.
“We’re controlling our own destiny by working directly with our own accounts, sorting it and bringing it into our mill,” Rusk says.
However, the company’s Forney mill is not totally immune to contamination concerns because it has contract agreements with outside suppliers as well. Rusk notes that bales delivered by suppliers tend to have slightly higher contamination rates. He adds that he noticed higher contamination levels in the last two quarters of 2018 from many suppliers.
“We’re controlling our own destiny by working directly with our own accounts, sorting it and bringing it into our mill.” – Marty Rusk, Smurfit Kappa North America
“The main impact [of China’s scrap import restrictions] is the availability of quality fiber,” Rusk says. “If a supplier was moving material to China, they were used to those lower quality levels, which is lower than our standards. China shut doors, and they didn’t adjust quick enough, so now there’s no place for some of the paper. There is a glut in the market, and that’s reflected in the price.”
Smurfit Kappa North America hasn’t cut back on its contracts with its recovered fiber suppliers. Instead, Rusk says the company has been inspecting incoming loads more thoroughly and has taken a hard stance on rejections when needed. If rejections persist with a vendor, he says the company will “work with the supplier on their facility floor and offer suggestions on how they can improve their bales.” He adds, “Nobody benefits from a rejected load.”
Rusk continues, “A lot of large companies out there have been talking at conferences about the percentage of contaminants they are seeing in the waste stream. It takes effort from everybody to make sure this doesn’t contaminate our system.”
Constant contact
Smurfit Kappa North America’s recycling division works alongside its suppliers as much as possible. Rusk says the company’s suppliers for its Forney paper mill are all based within a 300-mile radius—from near Shreveport, Louisiana, to the east to Abilene, Texas, to the west.
Rusk says it’s ideal for the company to visit with suppliers every month “just to ensure that quality is on their minds.”
One of the biggest things Rusk says Smurfit Kappa educates its suppliers on is sorting. He says he reminds them to be teaching their customers and communities about how to recycle properly.
“The more that [suppliers and recyclers] can coach their customers to separate at the source, the better things will be for the entire system,” he says.
Rusk adds that retail generators also should educate their employees on what can be included in recycling. “[Employees] change at these companies all the time,” he says. “You have to be sure they’re up to speed.”
Although educating suppliers takes “a lot” of time, Rusk says it will help to improve the quality of recovered fiber going to paper mills in the long run.
“It’s all about how they sort material, that’s key,” he says. “It’s all about the sorting process and educating on sorting.”
Smurfit Kappa also educates suppliers on any noticeable safety concerns. Rusk says he recently saw a safety concern with a retail chain supplier. The retailer’s drivers weren’t completely safe in their unloading processes.
“From time to time, you hear of drivers getting hurt in the process of opening up a door,” he says. “So, we’ve come up with straps we put on the door before we unload anything in our paper mill. They can open up the door, and if something’s against it, it can’t fall back on the driver because of the straps. It’s a simple thing like that that goes a long way.”
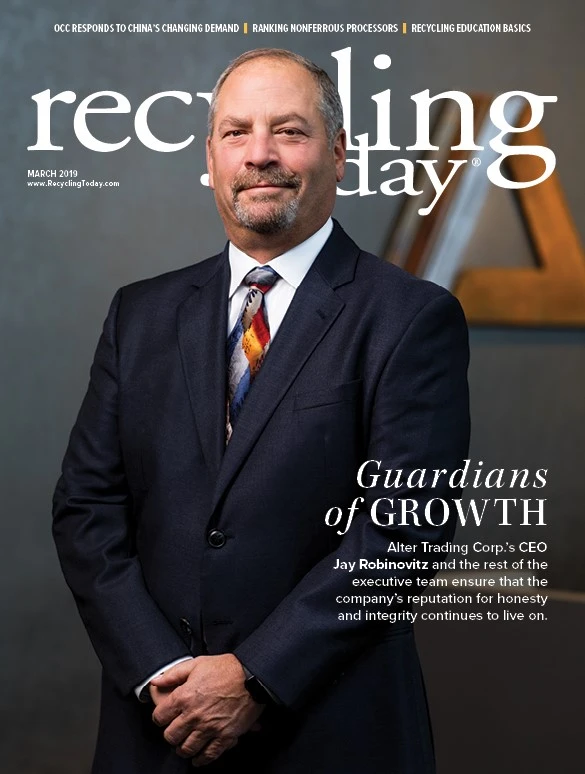
Explore the March 2019 Issue
Check out more from this issue and find your next story to read.
Latest from Recycling Today
- Lautenbach Recycling names business development manager
- Sebright Products partners with German waste management equipment company
- WasteExpo transitions to biennial format for enhanced experiences
- Study highlights progress, challenges in meeting PCR goals for packaging
- Washington legislature passes EPR bill
- PureCycle makes progress on use of PureFive resin in film trials
- New copper alloy achieves unprecedented high-temperature performance
- Gränges boosts profits and sales volume in Q1 2025