Waste Management’s St. Charles Street material recovery facility (MRF) in Newark, N.J., processes material from a 200-mile radius. The former dual-stream facility was redesigned in 2008 to process commingled material, making it the largest single-stream MRF in New Jersey, according to Waste Management (WM), based in Houston.
The company and its subsidiary Waste Management Recycle America (WMRA) have invested more than $4 million in the 110,000-square-foot facility to install the single-stream system, which includes three optical sorters, a glass breaker and assorted screens. The system aids in the separation of commingled material from residential as well as commercial sources.
"WM Recycle America is focused on making it easier for people to recycle, at home or at work," WMRA President Patrick DeRueda said at a ceremony celebrating the opening of the MRF in the spring of 2008. "By making the process of handling recyclables simpler for New Jersey residents and businesses, this retooled facility has the potential to significantly increase local recycling participation rates, enabling us to further reduce waste, recover more material and improve the effectiveness of municipal and commercial recycling programs."
The St. Charles Street MRF processes material from a variety of municipalities and counties within a 200-mile radius, according to Mike Taylor, director of recycling operations for Waste Management. Taylor is based out of the company’s Columbia, Md., office.
REGIONAL DRAW
"We can currently draw material from as far away as 200 miles," Taylor says, adding that most of the material the MRF processes comes from within a 100-mile radius of the facility. "It really is dependent on our customers and our geography with respect to transfer facilities. Our strength is using the Waste Management transfer assets as a means of drawing more material," he says.
The WMRA St. Charles Street MRF, which was designed to process 12,000 tons per month, is currently processing 10,000 tons of material per month, running two shifts per day.
Most of the material arriving at the St. Charles Street facility is collected through single-stream residential programs; however, the MRF does not process single-stream material exclusively.
Regardless of whether the material is from residential programs or from commercial accounts, it is introduced to the MRF’s single-stream processing system in the same way.
SINGLE MINDED
The St. Charles Street MRF features a single-stream processing system installed by Van Dyk Baler Corp., Stamford, Conn. The system features equipment made by Bollegraaf Recycling Machinery of The Netherlands and other European manufacturers.
SUSTAINABILITY MOVEMENT Houston-based Waste Management (WM) has released its 2008 corporate sustainability report, titled "The Color of Our World." The report outlines the internal steps the company is taking to advance its environmental performance in addition to a number of environmental services it provides for customers. "A sustainability program requires everyone in our organization to envision a better future and take concrete steps to protect and enhance the environment," says David Steiner, CEO of Waste Management. "Many people identify us by our green trucks and bins, but we want customers to understand we are more than a garbage company; we enable others to succeed by helping them to implement responsible social and environmental business practices. Not only are we setting ambitious targets for our own operations, we are also continually expanding the ways we can help customers thrive through efficient and responsible practices," he adds. In 2007, the baseline year of the report, WM established four key goals for corporate sustainability: • Doubling waste-based energy production—Today, the company reports creating enough energy to power 1 million homes each year through landfill-gas-to-energy and waste-to-energy facilities. • Triple the volume of recyclables—WM currently manages 8 million tons of recyclables, and by 2020 it plans to process more than 20 million tons. • Improve fuel efficiency—By directing capital spending of up to $500 million per year throughout the next decade, the company will move to increase fleet efficiency by 15 percent and to reduce emissions by 15 percent by 2020. • Preserve and restore wildlife habitat—WM plans to quadruple the number of its facilities certified by the Wildlife Habitat Council from 24 to 100. The 2008 report provides a baseline by which these four key elements of Waste Management’s sustainability program will be measured and outlines its progress toward those goals. The report is available at www.wm.com/wm/environmental/srr.asp.
The system includes optical scanning technology that is used to sort and separate plastics, an OCC (old corrugated containers) screen that segregates OCC from the commingled stream and a double-deck screen to separate ONP (old newspapers).
A drum feeder, which is designed to improve plant performance by providing a constant flow of material, transports material to the infeed conveyor. The conveyor deposits material to a pre-sort station, where employees screen out large residual material, Taylor says. The material is then conveyed to the OCC screen, which separates the OCC from the other material. At this point, the OCC is diverted to a bunker and is then baled for shipment.
The remaining material is conveyed to the double-deck news screen, which removes the fiber from the containers. Once the material goes through the double-deck screen, roughly 5 percent of the fiber remains in the stream, Taylor says. A secondary screen, known as a "banana screen," is employed to remove the remaining fiber from the containers. An optical sorting unit from TiTech, based in Norway and Germany, also aids in separating the containers from the fiber in the incoming material stream.
"The containers then proceed to our commingled separation system, where we are using a high-volume container separation system," Taylor says.
The MRF uses a glass breaker at the start of the container line to segregate the glass containers from the rest of the container stream. After this step, steel cans are removed with overhead magnets. Then two sizing screens are used to separate milk jugs and two-liter bottles from 20-ounce and smaller bottles and UBCs (aluminum used beverage containers). The smaller material is then run through two eddy currents to recover the aluminum, he says. The plastics are recombined prior to being run through two additional optical scanners that are calibrated to recover plastic containers Nos. 1 through 7.
SUSTAINABILITY MOVEMENT |
Houston-based Waste Management (WM) has released its 2008 corporate sustainability report, titled "The Color of Our World." The report outlines the internal steps the company is taking to advance its environmental performance in addition to a number of environmental services it provides for customers. "A sustainability program requires everyone in our organization to envision a better future and take concrete steps to protect and enhance the environment," says David Steiner, CEO of Waste Management. "Many people identify us by our green trucks and bins, but we want customers to understand we are more than a garbage company; we enable others to succeed by helping them to implement responsible social and environmental business practices. Not only are we setting ambitious targets for our own operations, we are also continually expanding the ways we can help customers thrive through efficient and responsible practices," he adds. In 2007, the baseline year of the report, WM established four key goals for corporate sustainability: • Doubling waste-based energy production—Today, the company reports creating enough energy to power 1 million homes each year through landfill-gas-to-energy and waste-to-energy facilities. • Triple the volume of recyclables—WM currently manages 8 million tons of recyclables, and by 2020 it plans to process more than 20 million tons. • Improve fuel efficiency—By directing capital spending of up to $500 million per year throughout the next decade, the company will move to increase fleet efficiency by 15 percent and to reduce emissions by 15 percent by 2020. • Preserve and restore wildlife habitat—WM plans to quadruple the number of its facilities certified by the Wildlife Habitat Council from 24 to 100. The 2008 report provides a baseline by which these four key elements of Waste Management’s sustainability program will be measured and outlines its progress toward those goals. The report is available at www.wm.com/wm/environmental/srr.asp. |
The container portion of the system was part of the original installation at the St. Charles Street MRF, while the OCC, double-deck news screen and banana screen were added in 2008 as part of the facility’s expansion, Taylor says.
THE END OF THE LINE
The WMRA St. Charles Street MRF produces finished bales of ONP, OCC, aluminum, tin and mixed one through seven plastics. The glass recovered through the system goes to a benefication facility for further processing or is used in engineering applications.
The broken glass measuring 3/8 inches and smaller is being used in engineering applications, such as road base, while the larger glass pieces are sent to a Bridgeport, N.J., plant operated by Strategic Materials, based in Houston, where the three-color mix is optically sorted by color and returned to container manufacturers, Taylor explains.
"The news and corrugated goes predominantly overseas due to the facility’s proximity to Port Newark," Taylor says.
The commingled plastics are shipped to Waste Management’s integrated plastics facility in Raleigh, N.C., where they are optically sorted by resin type and processed further. "They produce a ground dirty flake that is going to end markets," he adds.
"As with any MRF, the revenue generation from the sale of the material has affected the facility," Taylor says of the market downturn. "We continue to do what we expected the facility to do in terms of processing and making a quality product. We can ensure the steady movement of material by producing a superior product."
Waste Management Recycle America has more than 30 single-stream recycling facilities in operation in the U.S. Taylor says the St. Charles Street MRF can produce a quality product because of the proper operation of its single-stream sorting system as well as the depth of WMRA’s management expertise that comes from operating a network of single-stream processing systems.
The author is managing editor of Recycling Today and can be contacted at dtoto@gie.net.
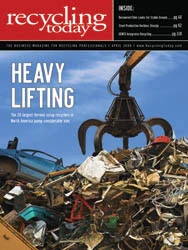
Explore the April 2009 Issue
Check out more from this issue and find your next story to read.
Latest from Recycling Today
- Aqua Metals secures $1.5M loan, reports operational strides
- AF&PA urges veto of NY bill
- Aluminum Association includes recycling among 2025 policy priorities
- AISI applauds waterways spending bill
- Lux Research questions hydrogen’s transportation role
- Sonoco selling thermoformed, flexible packaging business to Toppan for $1.8B
- ReMA offers Superfund informational reports
- Hyster-Yale commits to US production