
The hottest development in the recycling world during the past five years has been the movement toward single-stream collection of post-consumer recyclables. Using a host of new technologies, single-stream material recovery facility (MRF) operators are now able to accept mixed loads of paper, bottles and cans from commercial and residential sources.
Single-stream programs allow for fully and semi-automated containerized residential collection using traditional compactor trucks. Proponents say collection costs can be reduced by 35 percent to 50 percent.
But the reality, as many operators and recycling coordinators know, is that collection efficiency gains can also mean reduced material quality and added processing costs. Numerous studies show varying degrees of success for single-stream systems because of this.
Purchasing the right type of equipment, developing the proper relationships with markets, working carefully with municipal and commercial haulers and designing for specific types of material mixes all play a part in the success or failure of single-stream systems.
In Philadelphia, two entrepreneurs with more than 50 years of experience between them have achieved single-stream success. David DiIenno and Herb Northrop, the founders of Blue Mountain Recycling (acquired recently by Casella Waste Systems), have been involved in trash and recycling their entire careers. Both have worked for large industry players and independent recycling firms as well.
In 2000 they went out on a limb and bought an idle 62,000-square-foot Philadelphia paper-processing plant built in the early 1990s to handle high-grade office paper. DiIenno and Northrop gutted the operation then re-built it from scratch to process mixed commercial and institutional fiber. They also installed a separation system for food and beverage containers.
By early 2003 Blue Mountain was packing roughly 5,000 tons per month of material from commercial and residential programs—including a significant portion of Philadelphia’s curbside bottles and cans.
"We started out with a dual-stream setup," says DiIenno, "but it didn’t take too long with technology developments and the markets stabilizing before we set our sights on single stream."
Blue Mountain’s Philadelphia facility has gone through numerous retrofits throughout the past few years, but can now accept fully commingled loads of fiber and food and beverage containers. After shifting to single stream, the MRF processes up to 12,000 tons per month, though that figure is growing.
DESIGNING FOR GLASS. During the early planning stages for the 2004 single-stream renovation, DiIenno and Northrup looked at what others were already doing in the industry. "California was leading the charge," says DiIenno, "They had the first generation of single-stream systems." However, the California facilities had a number of problems with material flow and sometimes had to deal with costly downtime and quality control issues, he adds. Broken glass seemed an almost insurmountable problem, as well.
With a lot of contemplation and a good deal of common sense, DiIenno and Northrop thought through this problem. "We decided that one of the secrets to single-stream processing had to be to design your system to actually accommodate broken glass," says Northrop. Most single-stream MRFs are built to keep glass out of the paper stream as fiber flows through the facility. At Blue Mountain’s Philadelphia plant, however, the system has been designed to "want broken glass."
Blue Mountain Recycling now produces more than 2,000 tons per month of marketable crushed glass cullet. DiInneo and Northrop are in the process of developing 18 different markets for this material, including the use of cullet as a bulking agent for river dredge, in asphalt blends and concrete mix applications and as a filter medium.
The MRF also handles 10,000 tons of mixed paper, cardboard and commingled food and beverage containers.
THE KEY SCREEN. Trucks dump loads of mixed recyclables in a large bay at the top of Blue Mountain’s main facility. Cardboard is separated from the mix using a cardboard screen made by Bulk Handling Systems, Eugene, Ore. Magnets and eddy currents yank ferrous metals and aluminum out of the system. Plastic is mostly hand sorted.
The key to Blue Mountain’s system, though, is its new V-Screen Separator made by CP Manufacturing, National City, Calif. Using a combination of gravity, spinning discs and air, the paper portion of the mixed material flows onto the V-Screen. As the discs spin, small, heavier material falls to the bottom of the V, pouring onto another conveyor heading for further separation. Paper—free sheet, magazines, newspapers, phone books and more—floats on top of the discs and is blown up and over the sides of the screen, cascading onto two large conveyors where workers perform a negative sort, pulling out non-fiber materials.
Banking on Partnership |
Additionally, the company has developed an exclusive partnership in the Philadelphia area with up-start RecycleBank LLC of Philadelphia. This two-year-old company is looking to pioneer an innovative incentive-based curbside recycling program, awarding credits to every household that recycles in a municipality.
Deploying wheeled-carts with embedded radio frequency identification (RFID) chips, RecycleBank retrofits rear-loading trash trucks with on-board scales and cart lifters. A computerized scale system reads the chip coded with the cart’s address, weighs the material and logs the data into a computer. Residents can go on-line or use an automated phone system to learn how much they recycled and how many credits they earned. Credits are converted into discount coupons at more than 100 different businesses. Currently, RecycleBank is working in partnership with the city of Philadelphia on two pilot projects totaling 2,500 households in two city neighborhoods. Blue Mountain processes the RecycleBank material. Participation rates have tripled in the pilot programs, with households averaging about 25 pounds of recyclables per week (up from about 10 pounds before the program started), according to estimates. Blue Mountain’s single-stream capability lends itself perfectly to RecycleBank’s cart-oriented incentive program. “If we had to go dual-stream,” says Ron Gonen, RecycleBank’s co-founder, “it would take a lot longer to weigh two different containers. Blue Mountain Recycling has made our program a huge success.”
Within the solid waste service industry, the quality of an operation like Blue Mountain’s has not gone unnoticed. Casella Waste Systems, of Rutland, Vt., acquired Blue Mountain in September of this year. While a number of the biggest, publicly-traded waste companies continue to struggle trying to balance trash disposal interests with recycling service requirements, Casella has forged ahead on the recycling side of the equation with strategic MRF acquisitions throughout the years. In a recent report to investors, company chairman and chief executive officer John W. Casella said that the Blue Mountain transaction “is a great example of the execution of our strategic goals of sustainability—making recycling more sustainable economically for both our customers and providers of services and for driving significantly greater utilization of the company’s recycling assets.” |
DiIenno says, "Our system raises the bar for recycling. Now it will be easier for people to recycle more materials, ultimately increasing volume in programs, reducing costs to communities and improving our environment."
Blue Mountain has long-term contracts for all of the commodities it sells, its biggest with Kimberly-Clark. The MRF provides the paper giant with a quality tissue-grade mix loaded onto railroad cars that sit inside its MRF. "We get a detailed analysis regularly from the mill when they come to re-qualify our material," says DiIenno. "They say our color values are superior and that our product is clean."
Blue Mountain also has supply partnerships with Anheuser-Busch for aluminum cans; Tube City Inc. for steel; Apex Environmental for pulverized glass; Mohawk Industries, Wellman and Shaw Carpet for PET; KW Plastics and Trex Co. for HDPE; and Smurfit-Stone Container, Bowater, Abitibi-Consolidated, Solvay Paperboard and Canusa Corp.—along with Kimberly-Clark—for fiber.
CALCULATING CONTAMINANTS. As far as material contamination is concerned, according to a 2005 report by the Pennsylvania Department of Environmental Protection titled "Pennsylvania Recycled Material Composition Analysis", residue from Blue Mountain’s Philadelphia MRF ranges from 2 percent to 4 percent for residential material and 5 percent to 10 percent for commercial loads of paper. Now that its single-stream system is fully up and running, DiIenno says Blue Mountain’s Philadelphia MRF is seeing overall residue out-throws that range from 5 percent to 12 percent.
A WORK IN PROGRESS. Northrop stresses that the Philadelphia facility is a work in progress. "We’re taking a systems approach to this. The V-Screen was a multi-million dollar investment and it costs a lot to operate and maintain. This year we’re also putting in a number of optical sorters on our lines to better segregate our plastic container mix."
These sorters will first separate plastics by resin type and then further sort by color and density. As Blue Mountain continues to see more residential material, management calculates that the sorters should quickly pay for themselves.
Blue Mountain’s success has also led to the design and operation of a second MRF in nearby Montgomery County. DiIenno and Northrop are also considering an option to expand into the Wilmington, Del., market.
The quality of an operation like Blue Mountain has not gone unnoticed. Casella Waste Systems of Rutland, Vt., acquired the company in September.
In a recent report to investors, Casella Chairman and CEO John W. Casella said the Blue Mountain transaction "is a great example of the execution of our strategic goals of sustainability—making recycling more sustainable economically for both our customers and providers of services and for driving significantly greater utilization of the company’s recycling assets."
With Casella’s support, DiIenno and Northrop can continue to invest in Blue Mountain.
DiIenno says, "We’re like a pebble in the lake. Everything in the industry was on autopilot for a long time there. No one was being creative. But we’re having a lot of fun now and we’re making a difference. We’re helping change recycling in Philadelphia and we’re pushing the industry forward at the same time."
The author is a contributing editor to In Business who writes on recycling and sustainable development out of Philadelphia. He can be reached through www.blueolives.blogspot.com.
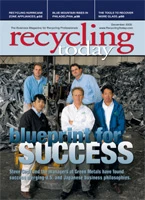
Explore the December 2005 Issue
Check out more from this issue and find your next story to read.
Latest from Recycling Today
- PCA reports profitable Q1
- British Steel mill subject of UK government intervention
- NRC seeks speakers for October event
- LME identifies Hong Kong warehouses
- Greenville, Mississippi, launches aluminum can recycling program
- Cotton Lives On kicks off 2025 recycling activities
- Georgia-Pacific names president of corrugated business
- Sev.en Global Investments completes acquisitions of Celsa Steel UK, Celsa Nordic