
To Frank Giglia, co-owner of Allied Scrap Processors Inc. in Lakeland, Florida, the beauty of the Zato Blue Devil twin-shaft shredder is its simplicity.
Metal scrap is fed into his Blue Devil seven hours a day, five days a week and requires minimal fuss.
“It’s a real simple machine and it runs all the time,” Giglia says. “It prepares the material well and produces a high grade of scrap, comparable to No. 1 [heavy melting] steel.”
The machine has served as a reliable workhorse since its installation in 2021. Used as a shear to complement the facility’s 1,000-ton shear that already was in place, the Blue Devil primarily is used to tear through light metal such as tin to help create a clean No. 2 heavy melting steel (HMS) product approved by Allied’s steel mill customers.
“As far as the grade goes, it’s perfect,” Giglia says. The mills like it a lot. They pay HMS No. 1 [pricing] for it. … It’s just not as dense as shredded [material], but the quality is good.”
Allied is owned and operated by the second-generation team of Giglia and his sister, Rose Mock. Its facility spans 15 acres and accepts a wide array of ferrous and nonferrous metals including tin; prepared and unprepared steel; unprepared nongalvanized metal; cast iron; nonferrous metals such as copper, aluminum and brass; motors; automobiles; and used electronics and cell phones. The facility purchases scrap from a range of domestic, industrial and commercial customers.
The full-service company was founded by Frank Giglia Sr. in 1956 and provides roll-off container services for commercial and industrial clients in Polk, Lake, Highlands, Hardee, Pasco, Hillsborough and Osceola counties and the surrounding Central Florida area.
When the time came in 2020 to purchase a machine that could process more material than what the facility’s shear already was handling, while reducing that material’s size to upgrade it for nearby mills, Giglia Jr. discovered Italy-based Zato’s offering through an online search and found it to be the perfect fit for Allied. “Nobody else could produce what Zato did,” he says.
Currently, Allied’s Blue Devil processes between 60 and 80 tons per day. “It works just as advertised,” Giglia says. “Everything’s been just like Zato said. The maintenance is low and there’s hardly any downtime at all.”
The Blue Devil also has made a believer out of Mock.
“It’s a very well-made machine,” she says. “That’s important. To me, it’s pretty much a beast for what the application is. … It’s got to have material that it can grip and tear apart, and it’s doing a heck of a job on it.”
Zato, which has a North American headquarters in Cincinnati, says the Blue Devil is a best-seller in the scrap recycling market because its versatility can meet or exceed almost all production requirements. The machine can shred light- to medium-grade scrap including entire cars and their engines.
The machine’s counter-rotating cutting shafts are either electrically or diesel powered by four hydraulic motors (two per shaft), coupled to four planetary gearboxes (also two per shaft). According to Zato, the slow-rotating high-torque shafts create a powerful cutting action that creates less noise, less dust and greater cutting efficiency than other rotary shears on the market. Its long-lasting blades are uniquely designed, made of special heat-treated steel with a profile configuration designed for high performance.
Zato says the machine allows for easy installation in a maximum of six days, and a maximum of three days for the quick transfer of the machine to other areas of the yard if required.
And both Giglia and Mock say Zato has delivered attentive customer service.
“I really like Zato,” Mock says. “For us, they’ve been really good. They’ve done what they said they were going to do. They’re getting parts here and doing all the right things to service North America. It’s not hard to get ahold of them.”
Giglia adds that the Blue Devil provides a low variable cost, low entry cost option that allows small and midsize yards such as Allied to upgrade the same material they have already been buying for a long period of time.
“We can compete for material much better because we have that upgrade capability now,” he says. “We’re really not buying any different material; we are just getting better prices because it is shredded and prepared.”
Zato will occupy booth 2361 at ISRI2024 April 15-18 at the Mandalay Bay Resort & Casino in Las Vegas.
Get curated news on YOUR industry.
Enter your email to receive our newsletters.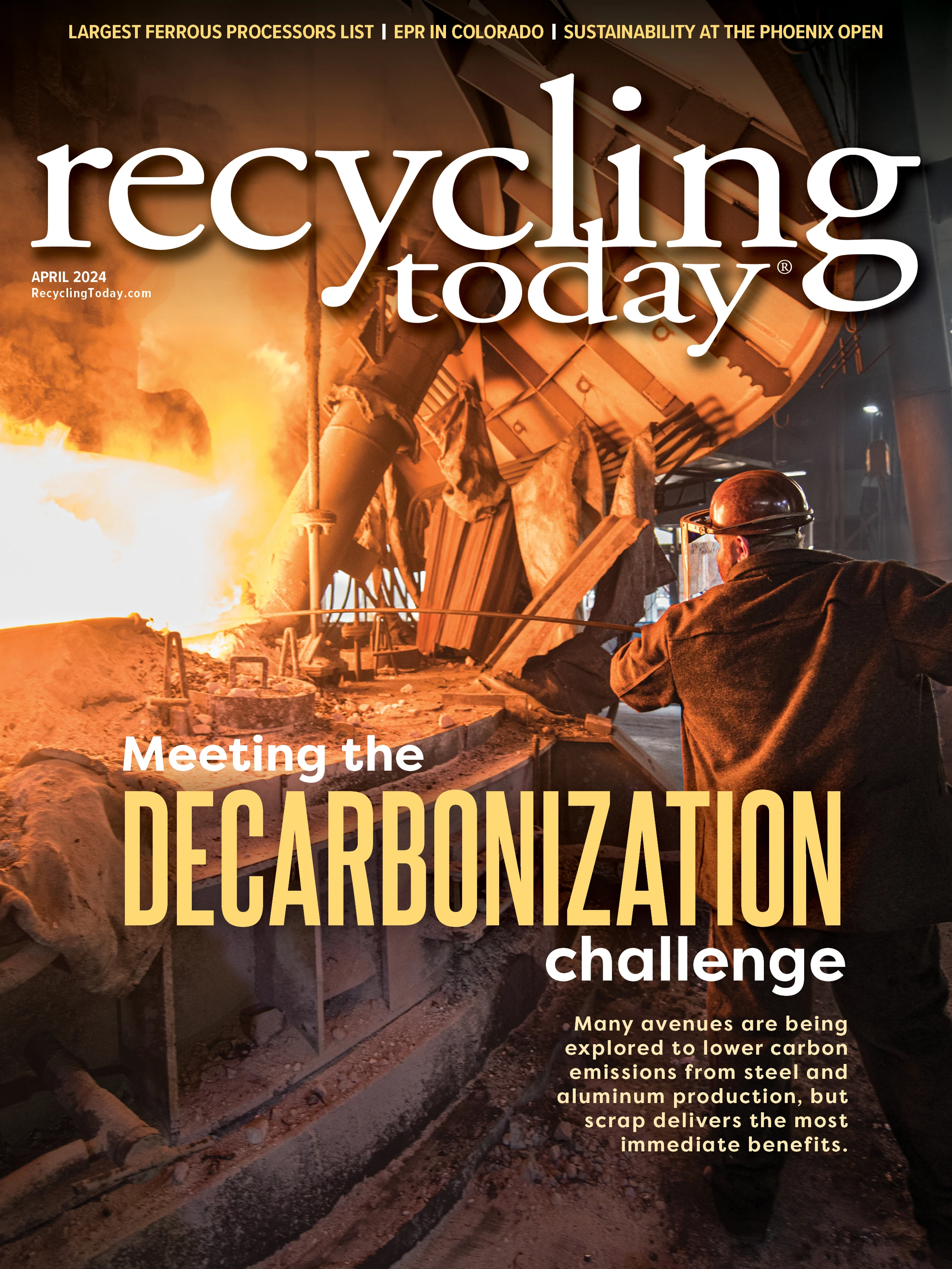
Explore the April 2024 Issue
Check out more from this issue and find your next story to read.