Electronics recycling in North America is slowly moving out of its infancy. Most processors of electronic scrap currently run operations that use the following simple, but effective, design: They manually dismantle the incoming material, run the material through a shredder and then sort ferrous and nonferrous metals using magnets and eddy currents.
After the sorting process, the remaining material is usually a mix of plastics, metals and circuit boards that are smaller than 2 inches. The metals and circuit boards are sometimes manually sorted from the remaining material, while at other times all of the remaining materials are sent to a smelter or shipped overseas.
Sorting plastic by resin type has recently become a popular approach because of the increasing value of the secondary plastics market. A wet separation technique is a traditional approach used in plastics separation. For example, sink-float tanks that contain different chemicals have been used to separate plastics by resin type.
However, with the evolution of near-infrared (NIR) technology, dry separation of plastics has become an economical alternative to these sink-float tanks.
INTERPRETING THE SIGNSBy computing the difference among the sign waves given off by the measurement of NIR light, high-speed NIR sorting machines like those from Oslo, Norway-based TiTech, which are distributed in North America by Stamford, Conn.-based Lubo USA (www.lubousa.com), can distinguish the differences among polymers such as PS (polystyrene), ABS (acrylonitrile butadiene styrene), PCABS (polycarbonate acrylonitrile butadiene styrene), PC (polycarbonate), PPO (polyphenylene oxide), PP (polypropylene), PE (polyethylene), and PVC (polyvinyl chloride).
NIR light ranges from 1,000 nanometers to 1,900 nanometers; the sign wave measured in this range is unique for each type of polymer. While some sign waves are easy to distinguish, other waves look very similar.
Having a high signal-to-noise ratio, TiTech’s high-speed NIR sensors are able to separate these polymers with purity rates of between 95 percent and 99 percent. As important as it is to have precise NIR sensors to distinguish among the various sign waves, it is equally important to be able to distinguish among the small shredded pieces of material in electronics scrap processing facilities.
While standard NIR technology is able to handle only objects greater than 1 inch, new technology has made it possible to sort objects as small as a ¼ inch. These high-resolution (HR) NIR sorters are capable of scanning 320,000 points per second across a 3-foot-3-inch conveyor, resulting in millions of measurements per second. This HR NIR technology is designed to ensures that no material is missed on the conveyor, resulting in recovery rates greater than 95 percent.
Additionally, by being able to shred to a smaller particle size, recyclers are able to liberate more metal from plastics that otherwise would have remained joined together, and electronics recyclers can achieve higher purity and recovery rates. This improves the efficiency of such sorting operations, allowing electronics recyclers to produce high-quality materials in larger quantities for each commodity they recover.
ON SECOND GLANCEIn electronics recycling facilities that process smaller volumes of material, system operators might not always use the full capacity of a NIR sorting system and may sometimes rerun end material to sort for a second resin (and maybe a third, fourth, etc.). Depending on what kind of material is being processed, the material composition can drastically change among the polymers.
Since it is impossible to see the input composition of plastics from electronic scrap with the human eye, statistical tools are used in determining the composition. Modern NIR sorters are able to record the different materials they "see" during a run and can provide statistical information about the processed material stream. While ABS and PS are often among the dominant polymers in electronic devices, running a batch of old iMacs one day may reveal a high amount of PC.
In light of the diversity of the material composition of electronic devices, operators need NIR sorting systems that can be easily re-programmed to suit their needs. For example, Load A contains mostly ABS, PS and PCABS, while Load B contains mostly PC, PS and PCABS with little ABS. When running Load A, the operator might want to sort ABS in the first run, then PS and finally PCABS. While running B, the NIR sorter can be easily programmed to first sort the PC, then PS and finally the PCABS.
BEYOND PLASTICSAnother application where NIR technology can prove beneficial is in the sorting of flame-retardant plastics that are of the same resin type.
To meet national and international safety standards, manufacturers of electronic and electrical devices have to mix materials into their plastics to prevent them from burning. These additives are commonly known as flame retardants (FR) and can be found mostly in ABS, PS and PCABS.
Plastics containing FR additives can be separated using TiTech’s high-resolution X-ray technology, helping electronics recyclers increase the salable value of their ABS, PS and PCABS by separating it into FR and non-FR fractions.
Today’s NIR sorting systems are easy to program and user friendly. They allow operators to efficiently and economically use NIR sorting technology to increase the revenue of their operations and to produce commodities of higher value.
The author is a sales engineer from TiTech GmbH, which is based in Oslo, Norway. He can be contacted at wolf@titech.com.
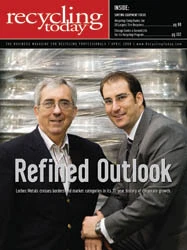
Explore the April 2008 Issue
Check out more from this issue and find your next story to read.
Latest from Recycling Today
- Athens Services terminates contract with San Marino, California
- Partners develop specialty response vehicles for LIB fires
- Sonoco cites OCC shortage for price hike in Europe
- British Steel mill’s future up in the air
- Tomra applies GAINnext AI technology to upgrade wrought aluminum scrap
- Redwood Materials partners with Isuzu Commercial Truck
- The push for more supply
- ReMA PSI Chapter adds 7 members