![]() Joseph Colubriale |
W
atching his recycling plant go up in flames more than a decade ago was disheartening for Joseph Colubriale, CEO of J.C. Fibers Inc., Chambly, Quebec, Canada. Although the life- long recycler acknowledges that the setback cast him into a month-long depression, Joe bounced back, a trait that has helped him not only to weather tough times, but eventually to prosper over them.Despite such setbacks, Joe and his associates (including two sons and two daughters who are part of the family business) have built one of the largest recycling firms in North America—one that shows no signs of pulling back from its growth trend.
CLIMBING THE LADDER
Joe began his career in the recycling industry in the mid-1960s with Plotnick & Sons Ltd. in Montreal. The facility changed hands numerous times in the 1970s, with Joe remaining as the head of operations for the location with each consecutive company.
While the successor companies that ran the Montreal recycling operation met with mixed results, Joe was always eager to stay, at times declining assignments in other cities. The volatile employment situation—combined with the always-volatile secondary commodity markets—gave Joe a feel for the roller coaster ride that can result from a life spent in the recycling industry.
In 1985, Joe decided to venture out on his own with the support of his family, opening J.C. Fibers’ first plant in Chambly.

"That first year, we recorded $700,000 in the three months we operated, and things have been going up ever since," he says.
Mixed in with the steady growth, however, have been a few lessons as the company has added to its service mix, spread to a new metropolitan region (Rochester, N.Y.) and suffered a major setback in 1989.
RISING LIKE A PHOENIX
"I started the business from a small location in St. Jean de Richelieu (near Montreal), but established myself in Chambly in 1985," Joe says. By 1989 the company had added a fleet of trucks, but a fire that year took the plant down.
Joe, depressed following the fire, originally had no intention of returning to the recycling industry. He changed his mind, however, because of his customers’ support.
"After the fire, people called me from all over to see what they could do to help," he says. "From September of 1989 to March the next year, it was challenging trying to service clients without a facility."
Crowning Achievements in Baling |
J.C. Fibers is well acquainted with Macpresse balers from Sierra International Machinery LLC, Bakersfield, Calif. The company, which is headquartered in Chambly, Quebec, has owned four Macpresse balers in the last 15 years and currently operates a MAC 111AS baler at its plants in Montreal and Rochester, N.Y. The company receives nearly 300,000 tons of paper, plastic and metal per year at its three plants and uses its Macpresse units to bale high- and low-grade fiber, which comes in loose, on pallets or in bins. The Rochester and Montreal facilities also offer in-plant confidential document destruction services. J.C. Fibers installed its first MAC baler in its Chambly plant in 1989 when rebuilding after a devastating fire. When it came time to upgrade to a larger baler in 1997, J.C. Fibers turned to Macpresse and Sierra again. This was after having purchased Macpresse balers for its Montreal plant in 1995 and its Rochester facility in 1996. Each plant has a capacity of more than 40,000 square feet and operates three shifts seven days a week. The Chambly facility is focused on recovery and recycling for the printing, commercial and paper mill industries, while the Montreal plant serves banks, high-rise office buildings and institutions, as well as the commercial, residential and industrial recycling markets. J.C. Fibers’s Rochester plant offers a combination of the services offered at both Canadian plants. Joseph Colubriale, CEO of J.C. Fibers, says he is most impressed by the quality of the MAC bales. And for a company with considerable export business, bale quality is key. "For the export market, you need to get a condensed, heavy bale." Joe says that’s exactly what Macpresse balers deliver. "They form sturdy bales that you can stack high," he says. Sturdy stacks of bales are also safer stacks, which appeals to J.C. Fibers’ dedication to safety. Additionally, Joe values the relationship J.C. Fibers has established with Sierra and Macpresse and their commitment to timely service and honest dealings. "As far as my experience, nothing beats Macpresse for us at J.C. Fibers," Joe says. "It’s the king of balers." With the help of its Macpresse balers and the ethics the staff of J.C. Fibers puts into practice, the company hopes to become a leading recycler in North America’s eastern region. |
During the reconstruction period, J.C. Fibers drivers continued picking up paper, delivering it loose to the mill. "This meant less money for my suppliers, but they still gave me that opportunity," he says. Joe adds that many printing plants allowed the company to manage their scrap paper on site.
Joe is honored by the loyalty his customers showed him after the fire and credits these relationships to his belief in treating everyone with respect and delivering on his word. He says that when J.C. Fibers takes pride in servicing its customers, the company is rewarded with long-term commitments.
Meeting the challenges associated with this period helped the Calubriale family decide to expand beyond a replacement facility in Chambly.
GROWING BEYOND BORDERS
During the scrap paper boom of 1994 and 1995, J.C. Fibers took advantage of its growing cash flow to build a recycling plant in Montreal and to purchase Regional Recycling & Resource Recovery Inc. in Rochester.
The purchase made J.C. Fibers an international company, though the Colubriales can argue that their attention to export markets has always made the business international in nature.
In combination with its growth outside of Canada, J.C. Fibers and its subsidiaries have also expanded the scope of their service offerings, which now includes industrial, office and retail paper recycling services; curbside recycling services; solid waste services; secure document destruction services; paper roll and sheet distribution; and transportation services provided by a fleet of 45 tractor trailers serving eastern Canada and the Eastern United States and the export locations found there.
The document destruction operations grew out of requests from Montreal’s banking and finance community and now include health care and government clients.
"Our company serves 85 to 90 buildings operated by the Quebec provincial government," says Joe, "and we also pick up documents for federal buildings located in our service area." The government service contracts have allowed J.C. Fibers to establish a presence 175 miles to the northeast in Quebec City. A J.C. Fibers plant in the Quebec City area may well be on the horizon.
This service, along with other programs designed to efficiently serve high-rise buildings, has helped J.C. Fibers increase the amount of office paper grades it handles each year.
Another pivotal way the company bolsters the amount of material it collects has been by offering residential and curbside recycling, which began in 2002.

The company’s J.C. Paper Recovery Inc. subsidiary collects residential waste and recyclables from approximately half of the city of Montreal, resulting in 15,000 to 20,000 tons of recyclables annually, Joe says.
LOOKING AHEAD
Joe says friendly, reliable service and timely payments are his keys to customer happiness. "I pay my suppliers," he says. "I tell them they’ll be paid every 30 days, and they get the check every 30 days." In this way, Joe is able to procure material without necessarily offering the highest dollar-per-ton figure. "Reputation is important," says Joe.
The legacy of the J.C. Fibers reputation is something that Joe has begun putting into the hands of his children and other people within the company.
"For a business to continue, you have to be a good coach, to keep employees motivated."
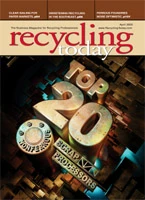
Explore the April 2005 Issue
Check out more from this issue and find your next story to read.
Latest from Recycling Today
- Fitch Ratings sees reasons for steel optimism in 2025
- P+PB adds new board members
- BlueScope, BHP & Rio Tinto select site for electric smelting furnace pilot plant
- Magnomer joins Canada Plastics Pact
- Out of touch with reality
- Electra names new CFO
- WM of Pennsylvania awarded RNG vehicle funding
- Nucor receives West Virginia funding assist