![]() Don Matthews |
I
n 1965 Ray and Barbara Matthews founded Ray’s Trash Service in Clayton, Ind., just west of Indianapolis, to keep their three sons busy. Forty years later, this side business with only one truck has grown to include three transfer stations, a scrap yard, a 17-county service area and a workforce of 330 employees.When Ray and Barbara founded the company four decades ago, Ray was employed as a factory worker in the Indianapolis area and worked part-time at the newly formed family business, which focused on trash hauling. The family incorporated the business in 1967.
FOCUSING ON FAMILY
In 1982, Don Matthews became president of Ray’s Trash Service. His brother Mark serves as the company’s vice president, while their sister Becky Bingham is the company’s secretary/treasurer.
Don says Ray is amazed at the company’s growth over the years. Ray still makes regular appearances at the company’s yard, either to deliver coffee and donuts, to mow the grass or to lend a hand overseeing the company’s operations.
Recently, a third generation of the Matthews family has entered the business, with Don’s son running one of the company’s plants. Don’s daughter Britter also spends her summer breaks from college helping out.
In addition to the leadership offered by the Matthews family, the company has also benefited from a dedicated staff of employees. "We have a lot of good people working for us," Don says. "Lots of good people help to keep the company successful."
Don says he keeps good employees by treating them with respect. "I wouldn’t ask them to do something I wouldn’t do myself," he says.
The Matthews and the staff at Ray’s Trash Service believe in hard work. "In this day and age, nothing is given to you," Don says. "Bigger doesn’t necessarily mean better if you work harder."
Working harder for Don meant expanding beyond trash hauling into the recycling businesses.
EXPANDING ITS FOCUS
About 15 years ago, Ray’s Trash Service began offering recycling services to its customers. Don says he realized the need for recycling and wanted to be a leader in the industry. Adding recycling services also made financial sense. "When you don’t own a landfill, you have to recycle," Don says of his decision to add the service to Ray’s roster.
Currently the company processes about 2,000 tons of material each day from its own hauling service and from several other companies.
Best Practices Make Perfect |
When it came time to set up metal processing equipment, Don Matthews, president of Ray’s Trash Service, Clayton, Ind., needed a little help in determining his equipment needs. He turned to Sierra International Machinery, Bakersfield, Calif. "John Sacco of Sierra was recommended by a friend. John visited me, we looked at another facility, and the 500 looked like the piece of equipment we needed," says Don. The shear/baler/logger has been operational since March 2004. Don says Ray’s is using its Sierra 500 to create No. 1 and No. 2 steel bundles, which it delivers directly to steel mills within Indiana. For a man who believes in hard work and dedication to the industry, Don appreciates the Sierra’s and the Sacco family’s straightforwardness. "John gave me the timeline for delivery, the machine was shipped from Italy and it got here on time. Everything John has said has been true," he confirms. In addition, Sierra helped set up the machine and train six of Ray’s employees. Even more importantly, Don indicates that the operators have had no problems with the machine. Don modestly suggests that he uses best practice scenarios to keep his business viable. "I’m not trying to reinvent the wheel. I try to learn from other people and from my mistakes." One lesson is to keep the product moving. With the Sierra 500, Ray’s can capitalize on the current boom in steel prices. "We take great pride in the fact that our material is prepped and ready to go," says Don. "When it’s shipped to the mill, it’s what the mill asked for. We inspect everything before it leaves the yard and know if it’s grade one or two. It’s totally ready for the end user." |
Ray’s three transfer stations bale corrugated, office paper and newspaper, while the company’s scrap yard shears and bales scrap metals, sending most of its ferrous scrap to Nucor’s Crawfords-ville, Ind., plant and to Steel Dynamics Inc., Pittsboro, Ind.
According to the company’s Web site www.raystrash.com, Ray’s has recycling programs in hundreds of businesses in Central Indiana that it services with its fleet of roll-off containers.
Don says Ray’s recycling facilities recover a greater percentage of material than other facilities in the state. He adds that the company spent the time and money needed to set its facilities up "right."
The company’s recycling plant in Clayton processes curbside recyclables and office paper. It is divided into two areas; the first is dedicated to the separation of curbside food and beverage containers, and the second area focuses on residential and commercial scrap paper.
Ray’s Zionsville, Ind., facility is dedicated to construction debris recycling, recovering aggregates, metals and cardboard from incoming loads.

The company’s newest facility in Indianapolis is equipped with the latest paper sorting equipment and specializes in various grades of commercial and residential mixed paper. The equipment at Ray’s Indianapolis plant enables area business to include previously unacceptable grades of paper. Ray’s commercial paper recycling program enables companies that previously did not generate sufficient quantities of paper to combine their cardboard, newspaper, office paper and magazines into a single stream to reduce their overall waste.
It appears as if Ray’s Trash Service has mastered the recycling aspect of its business. These days, Don says the company is looking toward future expansion and at making its hauling division more profitable. "Travel costs you time and money," he says. "If we can keep trucks in general areas, that will keep us more productive."
Productivity is a key operations concept at Ray’s Trash Service, especially when it comes to processing recyclables.

A CONTINUING COMMITMENT
The company’s approach to recycling involves "keeping the wheel rolling," as Don says, as opposed to reinventing it. "I try to learn from other people and from my mistakes." Don’s learning process also involves reading trade magazines and attending trade shows.
One of the lessons Don has taken to heart is the importance of keeping material moving. "The economy is the best it’s been for awhile with the boom in steel prices," he says, and moving material—whether it’s OCC or ferrous scrap—quickly helps Ray’s to capitalize on this trend. Ray’s choice of processing equipment affects the company’s ability to process material quickly and to receive top-dollar for it (see sidebar).
Ray’s Trash Service is committed to providing cost-effective recycling programs for its commercial, residential and industrial customers. Don says the company uses the latest technologies to increase material recovery at its plants. Ray’s also works directly with mills throughout the United States and overseas to ensure the best prices for its customers.
Ray’s prides itself on having its material prepped according to customer specifications and inspects each outgoing load the company ships.
This dedication to recycling and to the proper preparation of materials appears to be working to Ray’s advantage, as the company’s growth over the years will attest.
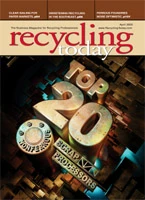
Explore the April 2005 Issue
Check out more from this issue and find your next story to read.
Latest from Recycling Today
- Fitch Ratings sees reasons for steel optimism in 2025
- P+PB adds new board members
- BlueScope, BHP & Rio Tinto select site for electric smelting furnace pilot plant
- Magnomer joins Canada Plastics Pact
- Out of touch with reality
- Electra names new CFO
- WM of Pennsylvania awarded RNG vehicle funding
- Nucor receives West Virginia funding assist