
The demand for plastics is increasing worldwide, and more end-of-life plastics consequently are being generated. However, this material can be recycled and returned to production with a high degree of quality using machinery to process primary and secondary raw materials, enabling a circular economy.
More industries such as the automotive and aviation sectors rely on plastics nowadays. For example, engineering thermoplastics are temperature-resistant and are characterized by their strength, toughness and damping properties—and this is why they are increasingly replacing metal in the automotive industry.
Plastics also are used increasingly by beverage and food producers. Polyethylene terephthalate (PET), for example, is particularly abrasion-resistant and resists diluted acids, oils, fats and alcohols. Used as packaging, this tough plastic protects food against spoilage and contamination.
However, as populations continue to grow worldwide, more plastics are produced, often ending up as waste rather than being recycled or reused.
Against this background, the European Commission presented its new plastics strategy in January 2018.
“Unless we change the way we make and use plastics, by 2050 there will be more plastic swimming in our oceans than fish,” said EU Commission First Vice President Frans Timmermans at that time. “The only long-term solution is to reduce plastic waste by increasing recycling and reuse. With the EU Strategy for Plastics, we are driving a new, more circulation-oriented business model onwards.”
Plastics, therefore, must be designed and manufactured in such a way that they can be recycled.
Recycling production waste
According to figures from the European Parliament for 2016, 39 percent of end-of-life plastics is incinerated, while only 31 percent is recycled—and that’s not much.
“The demand for recycled materials is still too low,” says Martina Schmidt, who heads the Recycling & Waste division at Vecoplan AG, based in Bad Marienberg, Germany. The company’s North American division, Vecoplan LLC, is based in High Point, North Carolina.
For this to change, manufacturers of consumer goods, building materials and furniture must rethink their approaches. According to forecasts, global demand for plastics will double in the next 20 years. Today, most plastics are still produced from crude oil or natural gas. However, according to EU policy and European recycling companies, the future should see the proportion of recycled plastics increase noticeably.
“The increasing demand for plastics can also lead to a tense supply situation,” Schmidt says.
Recycled plastics can be an economical solution for some companies.
High quality preferred
However, for more companies to use recycled plastics, they must meet their quality specifications. The purer the postconsumer resin (PCR) is, the easier it can be processed and used to produce high-quality products.
“Without consistent quality, there’s no process reliability, so we won’t have a good end product,” Schmidt says.
Production scrap in the form of purgings or rejects is, therefore, an economical alternative. The manufacturer can directly process this scrap into flake and return it through the smallest possible production circuit. Additionally, the material possesses the same quality as virgin material, since contamination and material mixing are reduced. This means that no waste is produced in the first place, and the circuit is closed.
In-house recycling offers many advantages: Companies spend less on new material, and processing at external recycling facilities is unnecessary.
In the case of postconsumer plastic scrap, the process is not that simple and can even become expensive. Recycling this material is more complex because it often is soiled and must be sorted. A great deal of water and energy can be required to process this material in such a way that it can yield high-quality PCR—and comparatively small quantities are produced relative to virgin material.
Schmidt says, “In the ideal scenario, however, regranulate possesses the quality of pure material, so it can be replaced one to one in the final application.”

The right technical solution
This is not quite as easy as it sounds, but the key is shredding. Schmidt cites glass-fiber-reinforced plastics as an example. “The fibers added to this material must be of a certain length to ensure the required rigidity,” she says. “If the fibers are too long, the quality suffers, and the same is true if they’re too short.”
Viscosity also plays a role when other plastics—such as PET—are compounded in the extruder. Material flow can be improved if shredding occurs in a single stage rather than in a multistage process.
What distinguishes a machine that’s up to the task and which components are important depends on the subsequent processing steps, Schmidt says, which often include washing, sorting and extruding.
Shredder manufacturers can adapt their shredding technologies to the materials in question and to the subsequent process steps. Schmidt says this lays the foundation for efficient, high-quality production.
“In the case of our shredders, it’s the cutting geometry that is decisive. We can exactly adapt our plants to input and output requirements by changing the rotors and cutters and selecting the right screen,” she says.
Schmidt adds that a shredder’s drive technology and a sturdy design also are important because they prevent premature wear when shredding abrasive materials, such as glass fiber-reinforced plastics.
Shredding technology can help recyclers close the cycle and ensure the quality of the PCR they produce. Schmidt adds that shredder manufacturers have all the necessary process engineering know-how to help recyclers produce high-quality recycled materials.
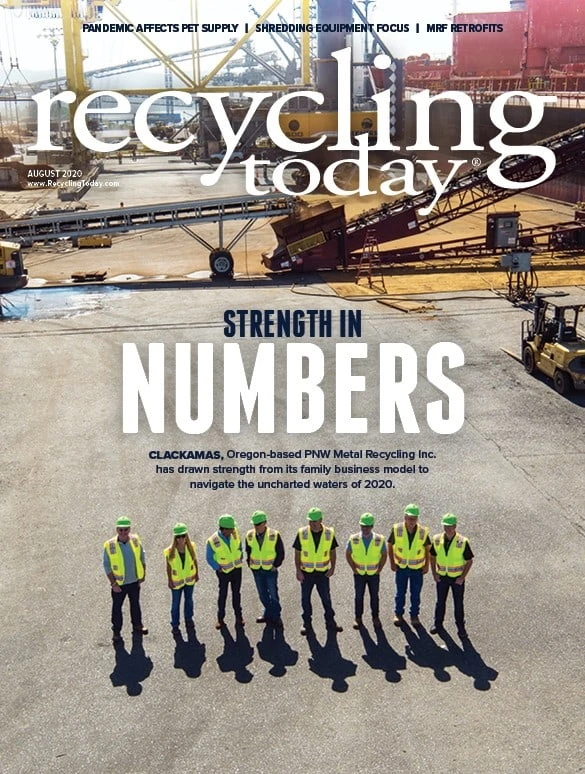
Explore the August 2020 Issue
Check out more from this issue and find your next story to read.
Latest from Recycling Today
- ReMA opposes European efforts seeking export restrictions for recyclables
- Fresh Perspective: Raj Bagaria
- Saica announces plans for second US site
- Update: Novelis produces first aluminum coil made fully from recycled end-of-life automotive scrap
- Aimplas doubles online course offerings
- Radius to be acquired by Toyota subsidiary
- Algoma EAF to start in April
- Erema sees strong demand for high-volume PET systems