At first glance, it may be difficult to imagine how a catastrophe in the food and beverage industry could cause far-reaching effects for managers of document destruction facilities. However, in February 2008, that unlikely scenario came to fruition when a fire erupted at an Imperial Sugar factory.
On Feb. 7, 2008, an explosion and fire at an Imperial Sugar plant in Port Wentworth, Ga., killed 14 workers and injured several more. News reports indicated that the explosion was caused by the accumulation of massive amounts of sugar dust within the facility.
As a result of the tragic fire, the Occupational Safety and Health Administration (OSHA) revised and reissued its Combustible Dust National Emphasis Program (CDNEP). OSHA enacted the original CDNEP in October 2007, but after the Imperial Sugar plant fire just a few weeks later, the regulatory agency reissued the CDNEP in March 2008. Among the most significant changes to the program were increased inspections and enforcement.
“OSHA revised the Combustible Dust NEP to focus on industries with more frequent and high-consequence dust incidents, and to include more inspections,” an OSHA spokesman says. The revised CDNEP calls for 300 inspections per year, up from the 80 inspections in the original program. Within the executive summary of the revised CDNEP, both the paper products industry and the recycling industry are specifically mentioned among the various industries that are expected to comply with the CDNEP.
According to an OSHA spokesman, the agency “has found more than 4,900 violations at the facilities inspected pursuant to the Combustible Dust NEP,” which includes dust-related violations as well as others. He adds that the average number of violations per NEP inspection is 6.5 in federal enforcement compared to 3.1 for other types of inspection.
Although there are costs to upgrading dust collection equipment, doing so now may ultimately save a company money in the long run, especially with increased compliance regulations, according to Jeremiah Wann, president of Jackson Center, Pa.-based dust collection equipment manufacturer Imperial Systems Inc.
“There has been a huge push by OSHA to force companies handling combustible dust to clean up their operations,” says Wann. “We have seen many companies get fines, some in excess of $750,000, due to poor housekeeping. Once OSHA gets involved, they might require you to install a system that is very expensive and that would not have had to been installed if the [original] system was properly designed in the first place.”
PLANNING A SYSTEM
Managers of document destruction companies must consider several factors before installing a dust collection system at their facilities, including shredding equipment selection, facility layout and method of conveyance.
“Shredding technology is the first step in understanding dust control,” says Dave Wilson, manager of document/product destruction for SSI Shredding Systems, Wilsonville, Ore. “Each type produces varying degrees of dust, consequently the type of shredding technology is the first thing to evaluate and understand.”
Wilson says, in general, the slower the speed of the cutting technology, the less dust it will produce. “A 20-rpm shredder will produce less dust than a 100-rpm shredder, and the most dust produced will be a hammer-mill type shredder.”
Additionally, when using a rotary grinder, document destruction companies should be sure to rotate the teeth regularly and to keep them sharp to reduce the amount dust generated, says Gregg Puhl, president and owner of G.F. Puhl, a dust control supplier based in Gallatin, Tenn. Puhl also advises using the maximum screen size available when possible, which will decrease the need to reshred documents and ultimately reduce the amount of dust generated.
Plant layout and location can have an impact on setting up a dust collection system. “We usually install any system over 5,000 CFM (cubic feet per minute) outside. Some industrial parks will not let you install equipment outside.”
Within a document shredding facility, it is vital to consider the amount of available floor space as well as ceiling heights and the location of support columns, according to Steve Idalski, sales manager for Alpena, Mich.-based Ameri-Shred. Idalski also notes that it is important to know the amount of voltage and maximum amps available to ensure that the dust control system will not exceed a facility’s electrical capacity.
Other planning considerations may seem obvious, but must not be overlooked. “Consider air flow patterns in the facility when you are determining placement of shredding systems,” advises Mike Carver, co-owner of SC Environmental, a Mequon, Wis.-based partner company of Cresswood Shredding Machinery that engineers and installs recycling equipment. “Keep equipment away from dock doors, for instance, where wind gusts may wreak havoc on dust control patterns.”
Material transfer points can be prime areas for dust generation. Therefore, Shred-Tech’s Mike Davison advises placing pickups at all transfer points. “Pickups should be located at each material drop point: from conveyor to shredder, conveyor to conveyor, conveyor to baler hopper and baler stroke exhaust,” says Davison, applications manager for the Ontario, Canada-based shredding equipment manufacturer.
Two predominant models are available for containing dust after the shredded material exits the shredder. “Conveyors can be equipped with top and bottom covers to contain dust,” says Jeff Dietterich, president of Advanced Equipment Sales (AES), a shredding system and dust control equipment provider based in Franconia, Pa. “Using air conveyance to transfer paper from the shredder to the baler instead of conveyor belts eliminates transfer points and keeps dust contained,” he offers as an alternative.
While using conveyors to transfer material may have cost benefits in the short term, Puhl says air conveyance is more effective at controlling dust. “Air evacuation is an excellent method to both convey the shredded material as well as to move the dust to a filter,” he says. “Conveyor evacuation of a shredder is less costly up front in many cases but does not address the dust generated in the shredding process.”
SHOPPING FOR A SYSTEM
Once a document destruction company has determined it needs to install a dust collection system or to or expand an existing system, selecting an equipment vendor that is aware of the various regulations affecting the document destruction industry is vital.
“Ask about the vendor’s familiarity with prevailing state, federal and local regulations as well as current applicable National Fire Prevention Association (NFPA) standards,” Dietterich says. “NFPA standards will be the primary point of reference for all above referenced regulatory agencies, insurance underwriters and other authorities having jurisdiction.”
Davison adds that the dust collection supplier should have a working knowledge of OSHA’s CDNEP and that document destruction companies should request the supplier’s aid in gaining the regulatory approvals needed.
In addition, shredding companies should provide equipment suppliers with a detailed floor plan of the site, information about the shredding method to be used and the FPM (feet per minute) speed of the cutting equipment, says Idalski. “The faster the FPM, the greater risk of a spark, fire or explosion. This may affect the type of dust collector needed; explosion proof or not explosion proof. There is a big difference in pricing between the two,” he says.
Wann says it is necessary for document destruction firms to have their dust tested to determine its Kst value (a measurement of dust’s deflagration index or explosive power). “We will need to know the Kst values in order to determine if explosion vents are required and how many,” he says, noting that the NFPA 68 Standard on Explosive Protection by Deflagration Venting requires deflagration venting depending upon the Kst value.
Wann says dust collection systems are sized by the square footage of media and advises comparing several dust collection systems using the ATC (air-to-cloth) ratio industry measurement. “It is extremely important to compare the ATC of the different collectors,” he says. “This will determine how long the filters last before you have to change them and how well the system performs during the life of the filters. If the ATC is too high, the filters will need changed more frequently and once the filters start to lead up, there will not be adequate suction.”
Finally, facilities that will be handling the destruction of electronic media or hard drives seeking to add a dust collection system have additional factors to consider. In most instances the system required for shredding electronic media is more extensive.
“When shredding electronics, hard drives and some products sparks can be created. If the spark reaches the dust collector, it could ignite a fire or cause an explosion,” Dietterich says. “The dust generated from shredding these items has different explosive characteristics than paper dust as measured by the Kst factor of the dust.”
He adds, “Metal dusts are generally far more explosive than paper dusts and therefore affect the required area of the dust collector explosion relief venting. The conveyance ducting should be equipped with a flame and spark detection and extinguishing system that will detect and extinguish the flame or spark while moving through the ductwork prior to entering the dust collector.”
Even facilities that are not currently shredding hard drives or other electronic devices may want to consider including such equipment or at least installing a system that can be retrofitted to include the necessary equipment, should the facility grow and begin handling these materials.
According to SC Environmental’s Carver, the fundamental question to consider before purchasing and installing a dust collection system is, “What are my current shredding requirements and what is my five- to 10-year growth plan for my plant-based destruction business?”
Answering that question may help document destruction firms to comply with current regulatory requirements in addition to enabling them to expand their operations as their business grows.
Get curated news on YOUR industry.
Enter your email to receive our newsletters.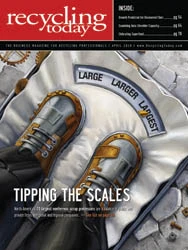
Explore the April 2010 Issue
Check out more from this issue and find your next story to read.
Latest from Recycling Today
- ReMA opposes European efforts seeking export restrictions for recyclables
- Fresh Perspective: Raj Bagaria
- Saica announces plans for second US site
- Update: Novelis produces first aluminum coil made fully from recycled end-of-life automotive scrap
- Aimplas doubles online course offerings
- Radius to be acquired by Toyota subsidiary
- Algoma EAF to start in April
- Erema sees strong demand for high-volume PET systems