Volatility is seldom described as a friend of business owners, but for recycling company owners it is a constant companion.
Operating in a supply and demand environment with volatile pricing, recyclers who invest in a multi-million dollar shredding system are to some extent making a statement that they can cope with the volatility.
In addition to that, however, shredder operators also can take steps to equip their systems to be adjustable in the way they sort and separate materials to attain a wide variety of grades, specifications and chemistries.
WIDE VARIETY
When it comes to investing in downstream sorting systems in particular, equipment manufacturers and vendors have aggressively called on scrap recyclers throughout this decade to let them know that they have new and improved equipment to offer.
The activity has been fueled not only by equipment companies with technological breakthroughs to bring to market, but also by recyclers who through most of this decade have shown a willingness to invest in their downstream systems.
A healthy percentage of metal shredding plants are operating at a level of sorting and separating sophistication that was perhaps not even conceivable at the start of this decade.
Auto shredding plants have moved well beyond their historic roots of efficiently harvesting and processing iron and steel scrap from the mixed batch of materials that comprise end-of-life vehicles.
Capturing the ferrous scrap remains vital, but the plants themselves, and especially the downstream systems, have been a major cause of capital investment because of the nonferrous metals content in the feedstock.
WIRED IN TO A NEW MARKET |
Recycling markets for scrap wire and cable are wellestablished, but auto shredder operators may be poised to play a larger role in this scrap segment. Sensing and sorting equipment being offered by manufacturers, such as the PolyFinder available in the United States through Wendt Corp., Tonawanda, N.Y., is designed to help identify and separate the small pieces of insulated copper wire (ICW) that can emanate from a shredding plant. Bill Close of Wendt Corp. says that some 80 percent of the ICW that is fed into an auto shredder emerges in pieces in the ¾-inch to 2-inch size range. These smaller pieces are not the focus at hand sorting stations, where larger pieces are typically harvested. Thus, an automated solution may prove profitable for shredder operators not currently separating this material. Adam Weitsman of Upstate Shredding, Owego, N.Y., is convinced that using automation to address this portion of his shredded scrap stream will prove to be a winner. “Our calculations show our shredding plant is generating $60,000 to $80,000 per day in insulated wire,” he comments. That material may be most profitable for Upstate if it can be processed into clean copper chops, which is why Upstate Shredding also has ordered wire chopping equipment to be installed in 2010. Weitsman notes that the equipment will not be dedicated to its post-shredder ICW alone, but that it will also be processing the wire and cable scrap the company buys as part of its overall scrap recycling operations. |
Scrap recyclers can opt to invest in newer and more effective magnets to pull out ferrous scrap, as well as increasingly sophisticated eddy currents and sensing and sorting machines that can help them produce marketable grades of red metals, aluminum scrap and stainless steel.
Recycling company owners and managers are diligent about exploring the many options and configuring a downstream system that can produce the scrap products or grades with the best margins in any given market.
MARKET FORCES
While the volatility mentioned earlier can be a source of headaches, it can also produce opportunities for scrap recyclers in the form of short-term profit margins that may emerge.
Scrap recycler Adam Weitsman of Upstate Shredding, Owego, N.Y., says that many of the investment and operating decisions he makes are based upon market conditions that can be relatively short-term.
Citing one example, Upstate runs its own heavy media plant which Weitsman says does not necessarily operate at all times. “It can be turned on or off, depending on the zorba price,” Weitsman says.
The plant separates red metals from the aluminum portion of the zorba stream. Weitsman says it is the pricing and demand for aluminum scrap from secondary smelters in North America that can dictate the media plant’s status. “If the domestic secondary aluminum smelters have strong demand and the pricing is good, you can use the heavy media plant to create a pure grade of aluminum sheet and cast and keep that in the domestic market.”
The heavy media system also extracts additional copper and brass scrap for export markets.
A technological innovation that Upstate and many other shredder operators have introduced is downstream equipment that extracts stainless steel scrap from the mixed stream.
Weitsman says that since installing his stainless-specific separating equipment, he has found it best to run the units in all markets.
The quality of newer stainless extraction units has impressed Weitsman. “The equipment is so much more advanced that we’re taking stainless out and shipping it domestically to stainless mills,” he says. “You couldn’t do that before. Now, even in a weaker stainless market, it’s best to keep removing the stainless and to reach that market.”
Bill Close, a sales engineer with equipment vendor Wendt Corp., Tonawanda, N.Y., says the decision to create mixed metals grades or to go for the purest possible sort rests on several factors.
“Shredding plant operators do have a lot of choices today,” says Close. “They can sell mixed metals domestically to heavy media plants or to China, or they can seek that incremental revenue that comes from running a more advanced downstream system.”
In many cases, aluminum margins are narrower and seeking the highest-purity aluminum grades may not suit a given market situation, says Close. “But the red metals almost always have enough incremental value to justify running machinery,” he adds.
Recyclers with whom Close has worked to design and install systems may configure a variety of machines and use them at different times to create zorba, zurich, twitch and other shredder grades, making adjustments to match the market. “It’s totally market driven,” he remarks.
Volume considerations and geographic aspects mean not all shredder operators work within an identical market, notes Close. “Commonly, operators on the East and West Coasts have easier access to the Chinese market, so their decision-making often has a bias toward export,” he says.
“Small to medium-sized shredder operators in the interior have higher freight burdens to reach the ports, so they may have more of an incentive to look for other solutions, such as sending material to the Huron Valley or Audubon Metals heavy media plants.”
FINEST FERROUS
Shredder operators also have a choice as to how much they wish to invest in drum and belt magnets, sorting stations and other equipment that can purify their ferrous scrap products.
Upstate Shredding, which is in the process of installing a new 10,000-horsepower auto shredder, also is investing in magnetic equipment to upgrade the quality of its ferrous scrap.
In particular, Upstate is installing finishing or polishing magnets supplied by Italy-based SGM Magnetics Corp., to create a low-copper-content shredded ferrous grade.
With its prior system of magnets and hand picking stations, says Weitsman, Upstate could produce a shredded grade with a copper content range of between 0.20 and 0.25.
The intent with the new system, he says, is to produce ferrous scrap with a copper content of 0.17 or less, for which buyers may pay a premium.
Weitsman says the system also extracts more copper-content “meatballs” and insulated wire pieces, which can ultimately contribute additional revenue on the red metals side.
Close says one of the equipment makers with which Wendt Corp. works, Norway-based TiTech, is gearing up to introduce a technical innovation designed to help shredder operators achieve a lower copper content in their ferrous shred.
He says high-powered magnet stands, such as ones being installed at a CMC Recycling facility in South Carolina in 2010, are another potential approach.
Even with a scrap market that has cooled off from its peak earlier this decade, it seems clear that scrap recyclers are continuing to invest in equipment and technology designed to let them take advantage of wider profit margins when those opportunities arise.
The author is editor-in-chief of Recycling Today and can be contacted at btaylor@gie.net.
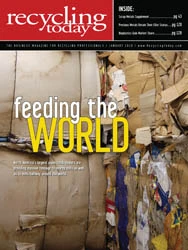
Explore the January 2010 Issue
Check out more from this issue and find your next story to read.
Latest from Recycling Today
- Nucor receives West Virginia funding assist
- Ferrous market ends 2024 in familiar rut
- Aqua Metals secures $1.5M loan, reports operational strides
- AF&PA urges veto of NY bill
- Aluminum Association includes recycling among 2025 policy priorities
- AISI applauds waterways spending bill
- Lux Research questions hydrogen’s transportation role
- Sonoco selling thermoformed, flexible packaging business to Toppan for $1.8B