The evolution of downstream separation systems has come about in direct relationship between the composition of cars and environmental concerns.
When shredders first came into being, the need for a downstream system was minimal to none. It was common practice to burn out the interiors of cars before shredding to eliminate most of the fluff and trash. This was a viable solution because there were no air standards to be met and there was less fluff than we have now. The dashboards were steel, there was very little sound insulation and the seats were not as luxurious as those of today’s cars.
There was also very little nonferrous metal in those early cars because the engine blocks and the transmission cases were all cast iron. After shredding, only magnetic separation was used to clean the ferrous product. No nonferrous separation was done at that time.
KEEPING UP WITH REGULATIONS
Then environmental laws were introduced and everything changed. Burning was outlawed and some form of additional cleaning was required to clean the scrap. Air systems were introduced to blow air through the scrap and vacuum the lighter fluff and trash away from the ferrous product.
The early systems consisted of a primary separation at the discharge of the shredder and additional air separation before any magnetic separation. There were many problems with this system. Any explosions that occurred in the shredder tended to explode in the primary air system also. The shredder was generally not hurt by the explosion, but the lighter air system was often severely damaged.
Also, smoke generated at the shredder was collected by the primary system and a column of smoke was created at the cyclone discharge. In addition to explosion problems, the air system required 500 to 600 horsepower for the fans and daily maintenance for cleaning the ductwork, air locks, etc. They also required constant repair of the ductwork, elbows, and cyclone shells due to the abrasive nature of the product being collected.
As environmental laws became increasingly strict, wet scrubbers were added to reduce the smoke, but were only marginally helpful. This dual cyclone with scrubber was the “standard” separation system for many years.
JUST ADD WATER
During the late ’70s and early ’80s the value of the nonferrous metals became apparent as more nonferrous was being used in the cars. The separation and collection of the nonferrous metals became another part of the system design.
Trommels and screens were the first attempts to clean the fluff product so other companies could process the ASR using heavy media separation to collect the nonferrous metals. Eddy currents came onto the scene in the late ’80s and early ’90s, serving as “add on” systems that do not necessarily affect the main separation systems for the ferrous product.
In the early 80’s the “wet” system was introduced to eliminate the air pollution problems. The “wet” systems consisted of flooding the shredder with water, using only magnets for separation of the ferrous product, and flooding the magnets with water, collecting all of this water in some form of tank, and trying to dewater the ferrous and nonferrous products. It seemed like a good idea, but the wet systems often had additional maintenance and water quality problems that many operators soured on them.
The next modification came in the form of “damp” shredding. This involved adding only a small amount of water to the shredding chamber to minimize the dust and smoke created during the shredding process. By minimizing the dust and smoke, the primary air separation at the shredder could be eliminated and all of the explosion and maintenance problems associated with the primary air system could be eliminated also.
In 1989, a “damp” shredding system was installed in Miami that had the magnetic separation before the air separation and was all under roof to minimize water run off problems. This system was designed to not lose any nonferrous metals to the air cleaning system, which was, and still can be, a problem with systems that do air separation first.
By doing the magnetic separation first, with two oscillating pan feeders and two axial pole drum magnets, the fluff going to the air system was almost non-existent. The axial pole magnets that were introduced in the late ‘80s often achieved results so superior to the shoe type magnets that they removed the need for an air system.
The axial pole magnets have a much wider field and use the whole face of the drum instead of only the pole shoe areas to separate and carry the ferrous product. Also, the axial pole magnets are wired so the primary coil is positive and the secondary coil is negative. By doing this, the material tends to flip as it goes from one pole to the next. The flipping action tends to release any rags or trash that may have been trapped between the ferrous product and the drum.
The system in Miami showed that if a third magnet was used in place of the air system, the scrap could be cleaned without air, and the “no air-no water” system was born. By using three individual pan feeders before each magnet and spreading the material out into single particles at each magnet, the three-magnet systems have proven they can produce very clean scrap without air separation.
Another advantage of the “no air-no water” systems is their ability to capture nonferrous metals. The eddy current separation systems can then produce a clean nonferrous metal product with virtually no loss of metals.
The “no air-no water” separation system also has the advantage of no emission source points, so no air permits are required in some states because there is no source to test.
The “no air-no water” system eliminates all of the horsepower requirements of the air system along with all of the ductwork cleaning and maintenance, thereby greatly reducing the operating cost and maintenance costs. It is my opinion the “no air-no water” separation system is the next major trend in shredder separation systems.
The author is the president of Innovative Recycling Systems, Solon, Ohio.
Sidebar
Recent Trends in Large Shredders
The experience of Texas Shredder Inc. (TSI), San Antonio, Texas, over the last three to four years is that (a) larger shredders are preferred, (b) smart water injection in the shredder box has become “the way to go,” (c) disc rotors have staged a comeback, (d) air cleaning after magnetic separation, coupled with eddy current technology for the non-magnetic fraction, is preferred, and (e) smart production management systems are coming into their own.
Larger shredders are in demand because they cost no more to run on a per-ton basis and often little or no over-time is necessary for normal maintenance. Also, if the machine is down for a few days, the monthly production can still be made as more tons per hour can be cranked out. Operators who have had 74/104s or 80/104s are moving up to 98/104s; and those with 98/104s are moving up to the 122/108 class; sometimes with more horsepower and sometimes not, as the bigger mills can give 10-15% more production even with the existing motor (provided the RPM are sufficient).
Sponsored Content
Labor that Works
With 25 years of experience, Leadpoint delivers cost-effective workforce solutions tailored to your needs. We handle the recruiting, hiring, training, and onboarding to deliver stable, productive, and safety-focused teams. Our commitment to safety and quality ensures peace of mind with a reliable workforce that helps you achieve your goals.
Sponsored Content
Labor that Works
With 25 years of experience, Leadpoint delivers cost-effective workforce solutions tailored to your needs. We handle the recruiting, hiring, training, and onboarding to deliver stable, productive, and safety-focused teams. Our commitment to safety and quality ensures peace of mind with a reliable workforce that helps you achieve your goals.
Sponsored Content
Labor that Works
With 25 years of experience, Leadpoint delivers cost-effective workforce solutions tailored to your needs. We handle the recruiting, hiring, training, and onboarding to deliver stable, productive, and safety-focused teams. Our commitment to safety and quality ensures peace of mind with a reliable workforce that helps you achieve your goals.
Sponsored Content
Labor that Works
With 25 years of experience, Leadpoint delivers cost-effective workforce solutions tailored to your needs. We handle the recruiting, hiring, training, and onboarding to deliver stable, productive, and safety-focused teams. Our commitment to safety and quality ensures peace of mind with a reliable workforce that helps you achieve your goals.
Sponsored Content
Labor that Works
With 25 years of experience, Leadpoint delivers cost-effective workforce solutions tailored to your needs. We handle the recruiting, hiring, training, and onboarding to deliver stable, productive, and safety-focused teams. Our commitment to safety and quality ensures peace of mind with a reliable workforce that helps you achieve your goals.
Smart water injection has come into its own as it, in most cases, means no air is needed on the shredder, which means no cyclone or high-horsepower fan, no scrubber, no pit, no ductwork and almost no maintenance. Explosions are reduced and/or mitigated as with a “wet” shredder, but there is no free water to be collected and cleaned. The material coming out of the mill is damp but not wet, so it can be cleaned with air, water, or, in limited cases, magnets only.
Disc rotors are back because they are much improved and the heavy shredding going on today is tough on spider rotors. There has been a lack of agreement over whether or not the spider rotor “cradles” an unshreddable so it can be ejected out the reject door and whether or not the disc rotor “keeps out” the unshreddable. Certainly there is some of each, but TSI’s sales show the disc rotor argument ahead by a large margin. The “no weld” feature, I must admit, probably has something to do with all this.
The traditional Achilles heel of discs was the constant welding, but the “no weld” discs are designed to gradually wear out
(as an example, around 300,000-400,000 tons processed on a 98/104) and then be replaced (the end discs are usually capped). As almost all of our disc rotor sales are “no weld,” it would appear the days of disc welding are winding down.
Air cleaning systems (drop-box, z-box or rotating drum) were for many years predominantly placed before magnetic separation, which was to clean up both the ferrous and nonferrous (known as “residue”) products. With a good system and two magnets (the industry standard) the ferrous fraction was clean to very clean and the nonferrous fraction would be up to 50% plus in dry weather.
The third fraction (“fluff”), picked up by the air system—from both the shredder pick up point and the downstream pick up point—was/is taken to a landfill. The tipping of fluff in the “good old days” was simple and cheap: much like the buying of the shredder feed material used to be!
When the reliable, cost-effective eddy current machine (ECM) came along, around 1990, the picture started to change as operators could easily clean-up their nonferrous to 80% or more, plus they discovered that the nonferrous metals (principally aluminum) in their fluff were sometimes over 3%. After some years of running separate ECM lines for fluff and residue, the concept of putting the magnet(s) before any other cleaning began to take over. This allows all material in one line to go through sizing and the ECM (often multiple units). In fact, TSI has not sold a new shredder plant any other way now in several years, essentially because buyers think this way makes the most sense when ECMs are part of the equation.
Production management systems are one of the latest ways to spend money on a shredder plant, and ideally, as with other capital equipment, they make money. Hardware, software and a fair amount of skilled labor are involved. If they are designed into a new plant, their overall cost is lower than with a retrofit job, but in both cases the benefits can be substantial. Even today, few shredder operators really know exactly where and how much their costs are. These systems can answer not only where the bucks are going, but also predict where they are going to go unless action is taken.
In these times where everyday operating costs of shredder plants are big numbers, those who do not have control over them will find profits even more elusive than ever.
—By Jim Schwartz, Texas Shredder Inc., San Antonio, Texas
Get curated news on YOUR industry.
Enter your email to receive our newsletters.
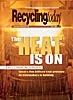
Explore the July 2001 Issue
Check out more from this issue and find your next story to read.
Latest from Recycling Today
- Green Cubes unveils forklift battery line
- Rebar association points to trade turmoil
- LumiCup offers single-use plastic alternative
- European project yields recycled-content ABS
- ICM to host colocated events in Shanghai
- Astera runs into NIMBY concerns in Colorado
- ReMA opposes European efforts seeking export restrictions for recyclables
- Fresh Perspective: Raj Bagaria