Sorting out the size reduction options available today can be confusing. More types of equipment are available from more companies than ever before. On the surface, the perfect solution seems readily available as one watches shredder videos that seem to process everything at record rates.
Unfortunately, reality is a different story. Despite all the equipment available and the increased capabilities, no one machine is perfect for all applications. There is no single machine that can do it all.
Finding the best solution requires a more thorough approach today. A buyer-beware attitude is appropriate for all of the different types of products available and their seemingly unlimited capabilities.
WHAT ARE THE QUESTIONS?
The basic criteria for buying equipment have not changed. The specific application requirements of the customer need to be clearly identified prior to evaluating any type of shredder. This includes a thorough analysis of the type of material to be processed; the feed method; the mix or percentage of material processed; the desired particle size required; discharge requirements; and budget.
Will the material be presented to the shredder in boxes, bales, rolls, slabs or loose? What is the chance of contaminants in the waste stream? Is general volume reduction required or is a specific particle size required?
Typically, the higher the production rate and the smaller the particle size desired the more expensive the solution, so be certain about your requirements. For example, if you request the shredder to produce a 50 mm particle size, be certain to specify whether a 50 mm strip of material is adequate, or whether a 50 mm by 50 mm cube is needed. The difference can be significant, as the 50 mm by 50 mm size will likely require a system to recirculate material with a screen. This is fine; however, utilizing a system with a screen has trade-offs.
While screens are useful at producing a uniform particle size, the screen may reduce the throughput rate significantly and some material may not be suitable for processing with a screen due to blinding of the screen. Since the screen restricts material flow, damage to the screen or equipment may occur if non-shreddable material is processed.
Twin Shaft Shredders
Slow-speed, twin-shaft shredders, also called rotary shear shredders, have been used for years as an accepted technology for processing a wide range of applications.
The twin-shaft shredder can be appropriate for applications such as composting, municipal solid waste, tires, metals, industrial waste, electronic scrap and plastics. The advantages of the twin-shaft shredder are many; but perhaps most notable is its ability to process contaminated waste steams that may contain metal or non-shreddable materials. Because of the large, heavy-duty, slow-speed cutting disks and the automatic reversing capabilities of the shredder, the chance of damage to the equipment is minimal when the shredder encounters difficult-to-shred materials. These large diameter cutters are also known for very long life, sometimes lasting years in non-abrasive applications.
The twin-shaft shredder of the proper size can be very reliable, provide low operating costs and process a high volume of material under many feed conditions and operating environments.
Companies such as SSI Shredding Systems Inc., Wilsonville, Ore., provide sizes ranging from 10 horsepower to 800 horsepower to meet the many applications suitable for processing on the twin-shaft shredder.
For some materials and for applications that require a smaller, more uniform particle size, the twin-shaft shredder is less suitable. Twin-shaft shredders are somewhat limited in the particle size they produce. Most materials with the twin-shaft tend to be shredded into strips of various lengths.
Strip width depends on the cutter width, and most systems provide one to two inch-wide cutters on the small and mid-range systems, 20-100 horsepower, and two to six-inch cutters on the larger systems, 150 HP-500 horsepower. Particle size lengths from the twin-shaft varies widely depending on the material, and can range from a few inches to a few feet. This particle size may not meet the needs in some applications to produce a consistent and smaller particle size.
Single Shaft Shredders
Single shaft shredder technology is now entering the market from many suppliers. This technology has advantages for certain applications.
The single-rotor shredders offer the advantage of better particle size control through use of a sizing screen. This technology typically operates at rotor speeds in the 80-110 rpm range with some styles operating at a much higher speed. The single-shaft shredder is ideal for processing “clean” waste streams such as plastic purgings, foam, fiber or fabric materials.
Most use a horizontal ram to feed the material to a single drum rotor. Rotor sizes vary typically in the 300-500 mm range. The cutting action is achieved as 30 to 90 small (40-50 mm) square cutters pass a fixed cutting anvil. If a sizing screen is used, oversize material is re-circulated and processed again by the rotor until the desired particle size is achieved. The small cutters often can be rotated two to four times and replaced when worn or damaged. Screen sizing can typically range from 5/8-inch to six inches.
Achieving a uniform particle size is a major advantage of the single-shaft shredder, but this technology also has limitations. Because the system is processing at a higher speed with a smaller cutter, some damage can occur if the cutter encounters certain size metal or non-shreddable material. Cutter life can also vary when processing abrasive materials such as carpet.
The rotor may have some difficulty processing some materials, as they can wrap or bridge in the cutting chamber. Some materials can plug or blind the screen. The higher rpm rotor can generate heat and create fines on some materials.
The single shaft shredder has its applications and is gaining popularity in certain applications.
Four Shaft Shredders
Sponsored Content
Labor that Works
With 25 years of experience, Leadpoint delivers cost-effective workforce solutions tailored to your needs. We handle the recruiting, hiring, training, and onboarding to deliver stable, productive, and safety-focused teams. Our commitment to safety and quality ensures peace of mind with a reliable workforce that helps you achieve your goals.
Sponsored Content
Labor that Works
With 25 years of experience, Leadpoint delivers cost-effective workforce solutions tailored to your needs. We handle the recruiting, hiring, training, and onboarding to deliver stable, productive, and safety-focused teams. Our commitment to safety and quality ensures peace of mind with a reliable workforce that helps you achieve your goals.
Sponsored Content
Labor that Works
With 25 years of experience, Leadpoint delivers cost-effective workforce solutions tailored to your needs. We handle the recruiting, hiring, training, and onboarding to deliver stable, productive, and safety-focused teams. Our commitment to safety and quality ensures peace of mind with a reliable workforce that helps you achieve your goals.
Sponsored Content
Labor that Works
With 25 years of experience, Leadpoint delivers cost-effective workforce solutions tailored to your needs. We handle the recruiting, hiring, training, and onboarding to deliver stable, productive, and safety-focused teams. Our commitment to safety and quality ensures peace of mind with a reliable workforce that helps you achieve your goals.
Sponsored Content
Labor that Works
With 25 years of experience, Leadpoint delivers cost-effective workforce solutions tailored to your needs. We handle the recruiting, hiring, training, and onboarding to deliver stable, productive, and safety-focused teams. Our commitment to safety and quality ensures peace of mind with a reliable workforce that helps you achieve your goals.
Four shaft, slow-speed shredders are also available from some suppliers. This shredder combines the strengths of the twin-shaft shredder for reliability and uses a sizing screen for particle size control.
SSI Shredding Systems Inc. has recently introduced the Quad 85 150 HP system for applications that require a more uniform particle size than the twin-shaft shredder can produce, such as the processing of mixed waste streams. Such applications include tire chip productions and electronic scrap.
The four-shaft shredder is a top feed shredder like the twin-shaft and processes material as the cutting disks shear the material. The lower cutters are typically bi-directional cutting while operating in either direction. The upper two sets of cutters clean the primary shafts and also provide some shearing. All the cutters sweep the sizing screen, which produces the desired particle size.
In summary, no one piece of size reduction equipment is the all-in-one do-it-all machine.
Each technology has its strengths and weaknesses and each machine excels in certain applications and is less effective in others.
When selecting equipment, choose to work with suppliers who are experienced with the equipment, support the system with parts and service, and provide a high level of applications knowledge.
This article was provided by SSI Shredding Systems Inc., Wilsonville, Ore.
Get curated news on YOUR industry.
Enter your email to receive our newsletters.
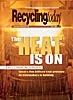
Explore the July 2001 Issue
Check out more from this issue and find your next story to read.
Latest from Recycling Today
- Green Cubes unveils forklift battery line
- Rebar association points to trade turmoil
- LumiCup offers single-use plastic alternative
- European project yields recycled-content ABS
- ICM to host colocated events in Shanghai
- Astera runs into NIMBY concerns in Colorado
- ReMA opposes European efforts seeking export restrictions for recyclables
- Fresh Perspective: Raj Bagaria