Size reduction equipment is viewed differently by recyclers operating in various segments. While metals recyclers may first think of automobile shredders, C&D operators think of concrete crushers and wood grinders while a document destruction machine may be the first thing that comes into mind for a paper recycler.
The many names alone—shredders, hammermills, pulverizers, grinders, granulators, crushers—can cause confusion for those entering the industry. Add to that the different design configurations and the array of end products desired, and it becomes clear that learning about size reduction equipment is a big part of learning about recycling.
The following summaries are by no means comprehensive, but ideally provide an overview of the different machines used by recyclers to create a shippable, saleable secondary commodity from obsolete items.
AUTO SHREDDERS
Large hammermills, with rotors ranging in diameter from 60 inches to more than 100 inches, are often called automobile shredders, though they can be used to downsize all types of materials.
Hammermills feature several large, hard metal hammers attached to a fast-spinning rotor that is powered by an either diesel or electric engine with up to 6,000 horsepower of force.
The machines are generally furnished with outboard flywheels for pulling them through any surge load periods. They must be built to endure a constant pounding, and are generally fitted with manganese or T-1 liners. In the larger machines, reject doors in the back upper housing are often furnished as a place where unshreddable items may be ejected.
The hammermill breaks up items as large as mini-vans into fist-sized pieces of material that enter downstream systems where they can be separated into like material streams.
The largest hammermills, sometimes referred to as super-sized shredders, can feature a hammer swing area of up to 120 inches in diameter, with about 1.2 million foot pounds of energy generated.
Each hammer on one of these machines weighs from 950 to 1,200 pounds. The machines can handle some additional materials—both bulkier items and more dense items—that their smaller predecessors could not.
The improvement and upgrading of these downstream systems using such equipment as eddy current separators and dry and wet media baths has become an area of concentration for shredder operators looking to offer premium grades of shredded scrap to both ferrous and nonferrous consumers.
Smaller hammermills are also used for shredding such items as aluminum sheet, cast and extrusions; steel shredding clips; white goods and small appliances; automobile parts; and other metal objects.
MEDIUM SPEED SHREDDERS
Medium-speed size reduction machines often feature a round drum with multiple cutter inserts that cut against a fixed bed knife. Cut material is often discharged through a screen to produce a consistently sized product.
Whether used with screens or not, the medium-speed grinders have been adopted by processors of plastics, tires, electronic scrap, wood and some types of nonferrous metals.
Plastic manufacturers using scrap material on site as well as plastics recycling companies have found uses for the medium-speed machines. Rejected bulky molded plastic parts can be batch-fed into the machine, processed by the rotor through the screen and fed back into an extruder for repelletizing.
Larger medium-speed grinders—ones that use up to 400 horsepower drives and with rotors weighing up to 20,000 pounds—are being used in the tire recycling industry. The machines are typically vertically fed, and like hammermills the force of the rotor is used to get much of the work done. But unlike a hammermill, a true cutting process also takes place.
These larger medium-speed grinders can reduce pre-shredded tire pieces to ¾-inch chips that are nearly free of steel. An added feature of the process is the machine’s ability to separate bead and tread wire from the rubber in a clean enough form to permit the sale of the steel as a scrap product.
Additional applications in which medium speed grinders have gained acceptance include the single-step processing of thin-film plastics to extruder-quality feedstock; the processing of asphalt shingles; as a secondary processor for wire and cable; and to shred carpet.
SHEAR SHREDDERS
The shear shredder—also described as a high-torque, low-speed industrial shear shredder—is a relative latecomer to the recycling size reduction line-up.
Among the advantages makers of these machines claim are their versatility, lower energy consumption, and lower levels of noise and dust.
The industrial shear-shredder has two or more counter-rotating shafts equipped with hooked knives capable of reducing a wide variety of recyclable materials, including tires, steel drums, some appliances, electronic scrap, carpeting, wooden pallets, and baled metals.
Shear shredders can feature drive systems using either direct electric or hydraulic systems.
Direct electric drives are frequently used for machines requiring 100 horsepower or less. These are relatively light duty, low-volume applications where shredder reversal is not likely to occur.
In an overload condition, the direct electric drive is unable to stall and reverse rapidly before resuming a forward rotation. The time needed for an electric motor to do these three things could exceed 10 to 15 seconds, causing the motor temperature to rise. Applications less likely to cause overloads include paper shredding and secondary step tire shredding.
Hydraulic drive shredders feature a motor powered by a pump connected to an electric motor or diesel engine. With this configuration, an overload can be sensed and the shredder can reverse away from the load and resume forward rotation in less than three seconds.
The shredder’s ability to reverse rapidly reduces prolonged stress on the machine and increases capacity due to the increased forward rotation time. Common applications include the shredding of tires, nonferrous metals, both rigid and film plastics, and polyurethane foam.
C&D EQUIPMENT
There are several different machines used to process the stream of materials produced at demolition and construction sites. Equipment manufacturers offer many different types of shredders, crushers and grinders for construction and demolition (C&D) recyclers to use.
With many construction projects preceded by the razing of trees, many states attempting to reach mandated landfill diversion rates have singled out green waste, or organic waste, as a portion of the solid waste stream that can be easily recycled.
Grinding tree limbs and branches into a usable mulch product has become one of the most common diversion techniques. Both municipalities and contractors engaged in land clearing have grown to rely on tub grinders and horizontal grinders to process trees and brush into mulch.
Tub grinders can trace their origins back to farmers who devised the machines to grind hay and other products into animal feed. In the 1980s, manufacturers began designing and selling heavier-duty tub grinders to handle the green waste stream that municipalities hoped to divert from landfills.
According to Dan Brandon, marketing manager for Morbark Corp., Winn, Mich., tub grinders are now built in sizes up to 15 feet in diameter and powered by engines with up to 1,000 horsepower. These large grinders can produce up to 500 cubic yards of end product per hour.
“Despite all its recent design enhancements, the tub grinder remains a very simple machine,” says Brandon. “At its heart is the hammermill, a high-speed steel rotor that can be equipped with a variety of hammer configurations, numbers, sizes and shapes, depending on the machine and the application.”
The top half of the hammermill extends through the floor of the tub to encounter incoming material.
Horizontal grinders contain a conveyor belt that feeds material into a solid drum that is fitted with replaceable cutters or a fixed hammer-style rotor, according to Mike Hinsey of Granutech Saturn Systems, Grand Prairie, Texas. RT
Excerpts from several past Shredder Guide articles are included in this feature, including contributions from Ed Kramer of American Pulverizer Co., St. Louis; Donald Graveman of Magnatech, Tonganoxie, Kan.; Terry Coker of Sunbelt Wendt LLC, Tonawanda, N.Y.; Mike Hinsey of Granutech Saturn Systems, Grand Prairie, Texas; and Rob Glass of Shred-Tech, Cambridge, Ontario, Canada.
A Crush on Concrete
While recycled concrete and asphalt cannot necessarily be said to be shredded, there is certainly a size reduction process occurring when slabs of pavement or building material enter a crushing machine.
Impact crushers use a large rotor with hardened steel “blow bars” placed intermittently to bang against the concrete being fed in and then to throw the pieces being created against a hard steel wall to break down those pieces further into smaller pieces. They are built in many different sizes, with some being able to accept sizable slabs of concrete, while others may require that material be broken down first in another type of crusher.
A common preliminary crusher type is the jaw crusher, which, as the name implies, uses metal “jaws” to break down large concrete and asphalt slabs into smaller pieces. Both impact and jaw crushers can be set up to contain downstream configurations that include a belt magnet to remove any steel reinforcing bar that enters the material stream.
Sellers of impact crushers contend that their units are better configured to produce a uniformly sized recycled concrete product, and that while jaw crushers can make a good first step in breaking down slabs, machines such as impact crushers or cone crushers produce the end product. (Cone crushers, more commonly used in the mining and virgin aggregates industries, are sometimes adapted for recycled concrete uses.)
Impact crushers are generally considered to carry higher ongoing wear parts costs, though many impact crusher manufacturers would point out that the machines are more affordable up front by a significant margin, leaving the purchaser with the ability to budget in the wear parts costs.
The wear parts on an impact crusher requiring intermittent replacement include the blow bars on the rotor, the side liner plates, and the apron or curtain liners.
Crushing equipment is made in various sizes and degrees of portability to suit different market segments. When large operations devoted exclusively to crushing concrete to produce secondary aggregates are established, and they tend to buy the largest units.
Other segments of the market—often seeking smaller machines—include demolition contractors and road construction contractors. These contractors tend to do their crushing on-site, perhaps crushing the concrete remains of one structure to be used as parking lot sub-base near the new building. Road contractors may tear up and crush slabs of old highway and use the recycled product as road base.
A variety of factors have led concrete crushing and re-use to become more common, including the depletion of quarries located within major metropolitan areas and the desire of states and municipalities to keep concrete and asphalt out of landfills.
Get curated news on YOUR industry.
Enter your email to receive our newsletters.
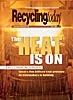
Explore the July 2001 Issue
Check out more from this issue and find your next story to read.
Latest from Recycling Today
- Nucor expects slimmer profits in early 2025
- CP Group announces new senior vice president
- APR publishes Design Guide in French
- AmSty recorded first sales of PolyRenew Styrene in 2024
- PRE says EU’s plastic recycling industry at a breaking point
- Call2Recycle Canada, Staples Professional expand partnership
- Circular Services breaks ground on north Texas MRF
- Tariff uncertainty results in choppy nonferrous scrap flows