When it comes to metals shredding operations, achieving high-volume output is one of the keys to success. But when high volume can be combined with the production of scrap grades that fetch a premium, it can bump up total revenues generated from shredding.
Ferrous Processing & Trading (FP&T), Detroit, has successfully become the dominant shredder operator in southeastern Michigan, chewing through piles of obsolete automobiles, appliances and other types of scrap with three auto shredders in the Detroit area (and additional Detroit area shredding capacity that would be able to come online should the ferrous scrap market kick back into high gear).
While the shear volume churned out by FP&T is impressive, the company’s capital investment in downstream operations is also worthy of attention.
Over the past nine months, FP&T has installed a post-shredder processing system that allows it not only to keep its downstream shredding operations entirely in-house, but also focuses on the quality of nonferrous scrap grades produced.
OLD NAME, NEW MISSION
SLC Recycling is a name that goes back more than fifty years in the Detroit area nonferrous scrap business. The company, founded in Detroit but based in adjacent Warren, Mich., by 1983, was acquired in 1997 by Windsor, Ontario’s Zalev Metals Inc., which was itself acquired by FP&T two years later.
Even after the dual acquisitions, the SLC Recycling name lives on and remains part of FP&T’s operations. In 2001, SLC’s responsibilities and volume have increased, and the company’s operations have moved about a quarter-mile down the road to a newer facility configured to accommodate SLC’s increased activities.
The front half of the company’s new facility looks like a traditional nonferrous facility, accepting contractor scrap and other peddler trade materials. Sorting, and in some cases baling, of assorted copper, brass and tool steel scrap takes place here
But the back half of the facility is quite different. Much of the new work that has come SLC’s way involves a decision by FP&T to consolidate its downstream shredder nonferrous separating and shipping operations at the SLC site, and these materials are being taken to the back half of the SLC facility.
According to FP&T executive vice president-nonferrous Dick Kenny, the company spent more than two years researching and designing a system that was put into place this year to “upgrade the nonferrous material produced by shredders for shipment to smelters, mills and specialty houses.”
As befits a company that features shredding as a core operation, the new SLC system features a Newell 60/104 shredder, which further downsizes and size-classifies the aluminum twitch brought in from FP&T’s auto shredding sites. Aluminum twitch is one of three types of scrap run through SLC’s shredder, along with aluminum extrusions and obsolete “old sheet” aluminum.
Beyond the shredder is further sorting and separating equipment that has helped FP&T greatly improve the chemistry of the aluminum, zinc, copper and brass scrap grades it derives from its shredder stream. “We’re very pleased with the chemistry we’ve been achieving,” says Kenny. “Before this equipment was set up at FP&T, we were getting 6% zinc levels in our aluminum twitch. Now we’re down between 1% and 1.5%.”
Producing a grade that is attractive to consumers is a mission that Kenny can relate to. His industry background is on the secondary aluminum smelter side, having spent many years with the former U.S. Reduction Co., a secondary smelter operator. “I’ve seen aluminum twitch from every place there is, and I have a pretty good idea of what consumers are looking for,” he comments.
The goal of the newly installed system, says Kenny, is “to upgrade the material for mills, smelters and specialty houses. The grades we’re producing are meeting different mills’ commitments to chemistry and content quality.”
CALLING UPON THE ELEMENTS
Earth, water, wind and fire—the forces of nature shaping the planet—are also called into service in the scrap recycling industry. In the case of SLC, all of these elements are put to use in one way or another to help the company create the premium nonferrous scrap grades coming out of its auto shredders.
Water comes in to play the least, as FP&T has chosen a sand separation system rather than a heavy media system, which relies on heavy media baths consisting of differently formulated waters.
However, when materials are shredded both at auto shredding sites and through the shredder at the SLC site, a light mist is sprayed to control dust and retain fine metallics as part of the material stream. Baghouses capture the remaining dust.
At the SLC facility, the first post-shredder step involves a trommel used to take out dirt and fines. The metallic fines falling through the trommel are sold as a lower grade melting material, while the larger-sized materials move on to the next steps of the sorting system.
Eddy current separators are also deployed at all sites, both at the auto shredding yards and as a post-shredder step at SLC’s facility. Each conveying line leading to the sand flotation systems is equipped with a Steinert eddy current that further purifies the nonferrous stream, removing plastics, rubber and other organics.
The sand flotation systems provided by the British company Rutherford Light Alloys provide a key processing step taking place at SLC. As of early in the summer of 2001, four of the sand separation lines were running at the FP&T plant, with two additional lines installed and ready to go should processing demands dictate greater capacity, and room provided for yet two more lines to be installed.
The sand systems provide a medium that allows lighter aluminum to stay afloat atop the grains of sand and be diverted as a positive sort into its own grade of clean aluminum. Remaining copper, brass and zinc pieces sink beneath the sand and are diverted to a different conveyor for additional processing.
That next step for the red metals and zinc brings the wind factor into the equation. These remaining metals are led to one of two optical sorting machines made by Metal Optics, a California-based company. These innovative machines can optically scan and identify metals by color, and can be programmed to detect the reddish tint of copper pieces or the yellowish tint of honey brass. Once identified, computer controls instruct air jets to direct the pieces to a separate conveyor.
While the machines have been helpful in separating these “sinking” grades of nonferrous metals, manual sorters double-check and improve upon the work of the optical sorting machines. Between the positive and the negative sorts produced by the machines and their manual checkers, FP&T is able to get shippable grades of copper, brass and zinc.
With sand systems providing the earth connection, shredder mist the water and air nozzles the wind, where does fire come into the picture?
In order to verify the quality of its nonferrous products for consuming smelters and mills, FP&T runs its own melt shop that conducts daily melts for chemical sampling of the nonferrous grades produced at the SLC facility.
“To provide a return on the media plant investments we’ve made, the quality and the chemistry of the material being produced is vital,” says Kenny. “We melt down samples daily and the chemistry information is fed back to our sales people and their customers. The quality program is fantastic. If you know what your chemistries are and they are consistent, you can get a premium,” he remarks.
Those statistics—the ones Kenny noted earlier showing a reduction in zinc content in the aluminum from 6% down to 1% to 1.5%—are showing that the investments were well made.
PUMP UP THE VOLUME?
FP&T’s investment in its downstream systems is noteworthy not only because of its innovation, but also because it is occurring at a time when scrap pricing and flow is in a cyclical trough.
Kenny says, though, that FP&T president Howard Sherman and other company leaders are making the investments to meet long-term needs. Installing and perfecting the systems in the down market will put the company in a position to take full advantage of the next upswing.
The system has been built “with room to grow,” says Kenny. “The operation is based on getting material in one door and out the other while maintaining the high quality standards.”
The company has set up the facility to exclusively handle shredder residue produced by FP&T’s own shredders. Noting the amount of competition, Kenny says he does not know if the company will accept outside residue in the future.
“We’re just getting to where the system is handling the volumes we projected,” notes Kenny. “This facility is just coming into its own now. This plant will be quite capable of processing at least 12 to 15 million pounds of nonferrous scrap per month. Once the markets turn around, this process will really show its value.”
The author is editor of Recycling Today.
WANT MORE?
Enter your email to receive our newsletters.
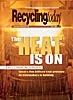
Explore the July 2001 Issue
Check out more from this issue and find your next story to read.
Latest from Recycling Today
- Republic Services, Blue Polymers open Indianapolis recycling complex
- Altilium produces EV battery cells using recycled materials
- Brightmark enters subsidiaries of Indiana recycling facility into Chapter 11
- Freepoint Eco-Systems receives $50M loan for plastics recycling facility
- PET thermoform recycling the focus of new NAPCOR white paper
- Steel Dynamics cites favorable conditions in Q1
- Hydro starts up construction in Spain
- Green Cubes unveils forklift battery line