Purchasing the right wear part for a construction and demolition (C&D) recycling application is an important decision. Matching the correct wear part to the job involves several considerations, including what type of material is being processed and how frequently the machine is being run.
Educated decisions should be made about factors such as alloy choices for wear parts and maintenance preferences for those replacing the parts and servicing the processing equipment.
Practical Decisions
Choosing the right wear part alloys depends on the materials being processed and the application, says Stan Wooten, regional sales manager, Amcast Inc., Huntington, N.Y. “It’s not just one type of solution or option. You have to find the right one that gets the right solution.”
Don Novak agrees material choice is very important. “The selection of the material is critical,” says Novak, manager, wear material design and marketing, Metso Minerals Inc., Milwaukee, makers of crushing equipment for construction and demolition (C&D) recycling applications. “Talking about the selection of material with hammers and blow bars is very critical to get maximum life out of the hammer, yet you want to avoid fracture of the hammer. Once it fractures and flies out of the slot, it could tear out other hammers. A broken hammer can cause catastrophic failure.”
Novak suggests that sometimes spending more money up front on things such as sorting mechanisms or even hand pickers can save more money in the long run as down time can be prevented.
Wear parts are made from several types of metal alloys, and many of these are ideally suited for a particular application. Typically, manganese is a more forgiving alloy, Wooten says, and is often used for bigger materials. “It is elastic, and more forgiving and less apt to breakage so you don’t have the brittleness in manganese that you would have in high chrome and martensitic steel.”
Bill Bajadali, marketing manager for Spokane Industries, Spokane, Wash., says, “Manganese has to work harder …and is an alloy that can be used in extremely tough applications.”
Looking at the materials to be processed is a good place to start to determine which alloy would best suit a job, says Tomaso Veneroso, metallurgical consultant, Amcast Inc. “First, analyzing the quality of rock or concrete or asphalt that would be crushed is important because every rock has a different composition,” he says. “So for every outfit we have a dedicated material.” For example, Veneroso says, some materials are not suitable for construction and demolition applications because they may break too easily. Others are more suited for that application. “Manganese steel is the most elastic, generally speaking. It is typically used for jaws in jaw crushers.”
High chromium is another choice for alloys in wear parts. “High chromium content is one of the factors that can provide optimum wear life,” Wooten says. “But, there are more limitations on that product. All of these products are very specialized.”
Bajadali also says, “Chrome steels do not need to work as hard and are probably most popular because they are tough and probably more forgiving than chrome irons.”
Another material for wear parts that has come onto the market in the past five years is ceramics. “The jury is still out on that one,” Wooten says. “Ceramics is something new in the market.” The ceramics are cast with the metal alloys when the unit is formed and poured, and it is formed into one product. “It is really a wear additive that ads to the wear resistance of the product.”
Ceramics can help with increased resistance to abrasion, Veneroso says. But he cautions ceramics may not be the best choice for use in all recycling applications. If one does use ceramics in a recycling application, he suggests “double checking the dimension of the material that goes inside of the machine. If you put a block of concrete in, you have a big chance of breaking a blow bar.”
Although the use of ceramics in wear parts is still relatively new, American Magotteaux, Brentwood, Tenn., does have blow bars available, the Xwin™, with ceramics embedded into the steel, says Willy Sonnet, business development manager, aggregate division. Sonnet says there are several advantages to the use of ceramics and steel.
“This way you marry the resistance against breakage of the chrome cast steel with the resilience against breakage, and at the same time, because you have ceramics in the wear part, you have increased resistance against wear,” says Sonnet. Ceramics are about two to three times harder than chrome cast steel, making the use of ceramics ideal for recycling applications. “You could double or triple the lifetime of the blow bar and have the same resistance against breakage.”
With the added strength and lifespan of a hammer containing ceramics comes the bonuses of less downtime and maintenance on the machine because wear parts need to be changed out less, Sonnet says.
“Last but not least, the safety ratio is improved since those blow bars are replaced manually,” he says, “reducing the frequency of maintenance also reduces the risk of injury.”
Howard Roth, sales manager, Plan A Inc., San Bernardino, Calif., says, “Few [wear parts] are made of tool steel, which has a decent wear property, but is very expensive and conversely used generally for very small parts.” The most common materials used are T-1 and high tech abrasion resistant steels. Wear parts can also be enhanced with chromium carbide welds or by embedding crushed tungsten carbide, Roth says.
A material that has proven most efficient in metals applications, Roth says, is embedded, crushed 100 percent Grade 93 tungsten carbide. Although tungsten carbide is the hardest metal known, it will break down when placed in blunt trauma applications, as it could in construction and demolition uses.
Overall, Veneroso says, “the secret to good metals, to me, is the heat treatment, because with the heat treatment you can play with all of the most important elements, such as elasticity.”
Wooten agrees that heat treatment is one of the determinants of how elastic or brittle the finished product is going to be.
Preparation is the Key
Making sure the materials to be processed are properly prepared is a key to extending the life of both the machines and the wear parts in those machines, says Danny Scott, sales manager, Eagle Foundry, Eagle Creek, Ore.
“One thing we advise customers to do is when you are recycling concrete, more times than not, there is another factor involved, and that is rebar (steel reinforcing bar). There is always lots of rebar in concrete rubble and the challenge comes in getting something abrasion resistant,” he remarks. “We have to provide them with a product impact resistant enough to withstand a reasonable amount of tramp iron going through the machine.”
While operators may want to make sure they are processing the most material their machine can handle, overloading a unit can cause more harm than good. “Material prep is a huge thing,” Scott says. “One thing that is important, and a lot of people know this, is that manufacturers make horizontal impact crushers to take a certain feed size, and the majority of contractors have a tendency to want to push these machines beyond their capacities.”
Overloading a machine can cause damage to the unit and could result in increased downtime compared to when manufacturer specifications are followed. “That is a challenge for the manufacturer of the wear parts—to educate the operators of the machines,” Scott says.
Using magnets to pull out metals, as well as hand pickers to prepare material, can save valuable time and money in the long run. “There are manufacturers who have magnets put on conveyor belts that will pick up rebar and tramp iron and chunks of steel that are not good for the wear parts,” Scott says. “You might not catch every part of steel, but you can seriously minimize steel going through an impactor.”
Keeping Things Running
Maintaining the equipment as well as wear parts can greatly affect how long parts may last, Veneroso says. “Maintenance of the wear parts without maintenance of the machine can cause damage. In an impact crusher, if the blow bars don’t fit perfectly you can damage the rotors. From my experience, there is good success in crushing if good quality parts are used from a good foundry with a good maintenance schedule and good operator.”
Maintenance issues also depend on the particular wear part as well. “There are not as many maintenance issues involved with hammers because the hammer is rotating in this material... you may want to be more selective as to what you cull out,” Novak says. “You want to get as much of the metal pieces out as possible. That would definitely be an advantage to have the material prepared and as clean as possible for an impact crusher.”
Tub grinders also have maintenance issues that could either prolong or shorten the life of wear parts, and possibly the entire unit. “Once you wear that hammer out you are losing your efficiency,” says Russ Rauterkus, western sales manager, Jacobs Corp., Harlan, Iowa. “You want to make sure the hammers are rotated and kept in good condition. Hammers, rods and screens all interact with each other.”
The author is the associate editor of Recycling Today .
Get curated news on YOUR industry.
Enter your email to receive our newsletters.
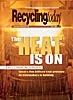
Explore the July 2001 Issue
Check out more from this issue and find your next story to read.
Latest from Recycling Today
- Green Cubes unveils forklift battery line
- Rebar association points to trade turmoil
- LumiCup offers single-use plastic alternative
- European project yields recycled-content ABS
- ICM to host colocated events in Shanghai
- Astera runs into NIMBY concerns in Colorado
- ReMA opposes European efforts seeking export restrictions for recyclables
- Fresh Perspective: Raj Bagaria