With customer input, shredder manufacturers have created machines capable of shredding everything from asphalt shingles to mattresses.
Shredders are a necessity in the reduction and recycling of construction and demolition debris ranging from asphalt shingles to furniture. They’re also employed in product destruction and in the cre-ation of decorative packaging. Some of these applications are brutal. Many shredder manufacturers take the specific applications into account, equipping their machines with the hardware and technology necessary to process such materials without flinching.
"There are difficult-to-shred materials, and then relatively common materials to shred," says Joel Miller of Hammel North America, Fort Wayne, Ind. "For example, a difficult to shred material might be construction and demolition waste because it has a wide variety of materials in it."
Miller points out that landfills may reduce tipping fees for shredded C&D material, as it spreads more easily, compacts better and requires less space. While many look for secondary markets for their materials, Miller says, some view shredding chiefly as an expense. "You’re trying to reduce your freight, and sometimes you’re looking at a revenue source . . . because there is an aftermarket for the material that you’re shredding."
Jack Cress, owner of Cresswood Recycling Systems, Cortland, Ill., says that his company sells shredders into the wood and plastics industries. Cresswood’s customers have reduced pallets into mulch or boiler feed and returned plastic purgings and rejects into the manufacturing process, he says.
Ken Lewis of Shred-Tech, Cambridge, Ontario, says, "Just about anything that is manufactured, if you want to recycle it, you have to reduce it." Shred-Tech’s machines have shredded everything from tea bags to napalm containers, Lewis says.
With the variety of materials and applications that require shredding, customer input becomes essential, and machines are often modified to better meet the needs of their users.
VARIETY SHREDDING |
Greg Conigliaro of Conigliaro Industries Inc., Framingham, Mass., puts it plainly: "It's a lot of fun shredding stuff." And he should know. The company began in 1990 as Conigliaro Engineering, a recycling services firm focused on the removal of paper waste from offices. However, the company changed its focus in 1991 to "total" recycling and incorporated under the name Conigliaro Industries Inc. Since that time, the list of recyclables Conigliaro Industries accepts has expanded to include 150 different plastic, metal, glass, rubber, wood, corrugated, paper and textile materials. Conigliaro Industries has shred everything from chocolate to mattresses to lamps at its 88,000 square-foot material recovery facility in Framingham. "Our key shredder is the AZ-80 Shred Pax Shredder," Conigliaro says. "We utilize that for all of our product destruction activities. It might be any kind of consumer good, clothing, anything at all that we are trying to destroy and render unusable. And then we recycle the constituent parts after it's shredded." Conigliaro Industries also uses the AZ-80 in its new mattress, box spring and furniture recycling program. The AZ-80 shreds these materials to the approximate size of a softball, Conigliaro says. The resulting shred then goes through a couple of picking stations where the bulk of the foam is removed. The remaining material goes under a magnet to remove the metal. The residual material is dumped into a roll-off container and off to landfill, he says. "I can tell you, the primary purpose of the shredder is to cut through the carcass of the mattress, really. That's some real tough stuff. It's very hardened steel, and it goes through it with no problem," Conigliaro says. He adds that Conigliaro Industries typically recycles between 60 to 90 percent of a mattress's volume, depending on its quality. Conigliaro Industries recently added an Andela Pulverizer to its AZ-80 and ReTech size-reduction equipment. Conigliaro says the company will use the Andela machine to create glass sand. The resulting sand will be combined with the plastic aggregate Conigliaro produces to manufacture Plas-Crete blocks. The blocks will contain 80 percent recycled material and can be used in the construction of retaining walls and storage buildings. . |
CUSTOMER INPUT
Despite the name, Industrial Paper Shredders’ (IPS) machines have shredded much more than paper, including wall insulation and carpet. DeeDee Thomas, co-owner of the Salem, Ohio, company says, "We start with a sample of material, ask the customer what they would like to see for the end results and design a shredder for their need. Our shredders are not made until we have consulted with the customer, shredded samples of their materials to their specifications and received their approval."
Customer input led Peterson Pacific Corp. (PPC), Eugene, Ore., to develop the HC 2400-B Portable Waste Recycler, a grinder that is designed to process asphalt shingles. Rebecca Smith, intranet and marketing specialist for PPC, says, "We have a customer in the Northeast who called and said, ‘I’ve been using this 2400-B that you generally run waste wood through, and it works okay, but I’d like to see it wear a little longer.’"
Smith adds, "I know that we have one customer in particular who was using a machine previous to ours, and he is getting something like three times as much production . . . since he started using the 2400-B that’s been modified."
While designing the modifications to the 2400-B, PPC engineers took operating costs and downtime into consideration, Smith says. "We really looked at the bits that we needed to use in order to grind the shingles. To the best of my knowledge, we started using a bit that is newer to the market. It’s a lot tougher and stands up to the beating from those shingles," she says.
Additionally, PPC improved the anvil and grates, added a 54-inch continuous conveyor system to improve material flow and increased the number of water nozzles at the compression roll to keep the shingles from gumming and sticking, Smith says.
Cress describes Cresswood’s machinery as "standard products, custom configured." Every application, he says, presents variations in cutter head and ram configurations and in feed systems.
Thomas says, "We manufacture 20 shredders, all of which can be re-engineered to the customer’s need. We have changed the shred size from 1-inch by 6-inches to 1/8-inch by 1/8-inch squares with variations in between. Also, we can put a screen on our cutters and make a disintegrator for very fine shreds."
IPS has also manufactured shredders out of stainless steel for shredding food, Thomas says. "We can carbonize the ends to shred very abrasive material like fiberglass. The opportunities are endless. If you’re material is pliable," Thomas says, "we can shred it."
ASSESSING THE OPTIONS
Miller says, "There’s basically two categories of shredder. There’s your high-speed shredder where the shredding mill rotates at 600 to 1,000 rpms. It generally shreds material and forces it through a screen that gives you a small piece size. Then there’s the low-speed shredder that can handle a wider variety of materials, and it rotates at 30 to 40 rpms. It has the ability to stop if it encounters an obstacle that will damage your shredder," he says.
"Many operators look at that as optimum, because a shredder is a high-maintenance, high-wear item because there is constant volatility," Miller says. He adds that while maintenance costs are reduced with a low-speed shredder, such machines typically will generate a piece size of 6 inches or 8 inches, which may require additional processing.
Cress says that one of the hallmarks of his single-shaft shredders is a uniform product size, which then can go on to a secondary grinder, depending on the customers’ needs. "This type of shredder technology will range anywhere from 60 rpm up to, say, 400 rpm, depending on the type of model and the type of configuration," he says.
Miller says that some operators are looking at tandem units where they grind material in a low-speed shredder, use magnets to remove the metal from the downstream and then go into a high-speed shredder for further size reduction. "You’re feeding your high-speed shredder with consistent piece size, and you are pulling 95 percent of the metal prior . . . so you are greatly reducing any potential damage to the machine, and thereby considerably lowering your maintenance cost," Miller says.
"Working in tandem, you can have two lower horsepower units doing the same work as a high horsepower, but in the long run, you’re going to have increased profits because of way, way less maintenance," he adds.
Dave Kaczmarek, owner of Shred Pax Inc., Wood Dale, Ill., says his company’s low-speed, high-torque AZ-80 shredder is cost efficient. The machine is most often sold to companies shredding C&D waste. Conigliaro Industries of Framingham, Mass., uses its AZ-80 to shred everything from mattresses to chocolate to lamps.
Kaczmarek says that the short distance between the center of the hex, the shaft and the tip of the knife on the AZ-80 produces more power.
Lewis says that adjusting the shredder for a particular application is only part of the equation. "It might not necessarily be that the shredder is the varying item. It could be the downstream processing equipment. For example, if you are shredding liquid packaging, you can shred that in just an ordinary high-torque shear shredder, but in the downstream equipment, you need to maybe have stainless steel vibrating screens to separate the fluids," Lewis says.
Cress says most sorting needs to be done prior to grinding. "If you get commingling of products after it’s ground, your value becomes so low, it doesn’t pay to grind it. You definitely have to pre-sort before you grind," he says.
With a slow-speed shredder, Miller says, the sorting can be done downstream. "You grind everything and then pull the metal from the output conveyor with a cross belt magnet or a cross belt in combination with a head pulley magnet."
Kaczmarek says, " We can install shaker tables with different size screens, magnets to pull out any metal objects. We can put trommel mills on them, which are particle sizers that go around the shredder to assure certain sizes. We can use a series of shredders to bring the stuff down to a powder, if you need to."
Cress says, "Part of the total solution is to put the material into the shredder and to take it away to minimize material handing." Reduced material handling means reduced labor, he adds.
FUTURE IMPROVEMENTS
Miller says, "There are different metals that are involved with difficult-to-shred materials as opposed to materials that you want to hit hard that fracture. Combinations of nickel and chrome and manganese give extra striking surface life because of the metallurgy involved."
Miller says that feeding mechanisms have been modified slightly, with more companies using a powered hopper rather than a belt infeed conveyor.
Additionally, Miller says that mobility is an issue. "Some of the shredders now have hook lifts so you can put them on container trucks rather than having to have an extra piece of equipment to load them onto a flatbed," he says.
Cress says, "Designs have given way to a lot more dependable machinery, which is demanded today in all sectors." In recent years, Cresswood has made changes in its cutter head geometry to give more output with less horsepower, Cress notes.
"Getting more output with less energy has been one of our biggest emphases," Cress says. "[We strive for] designs that make the machinery more dependable, which really means more bottom line profit for whoever buys them."
Miller says he thinks that recent advances in shredder safety, maintenance and transportation are the result of competition within the industry. "People are looking for some competitive edge," he says. Customers should certainly benefit from this competitive approach.
The author is assistant editor of Recycling Today and can be contacted via e-mail at dtoto@RecyclingToday.com.
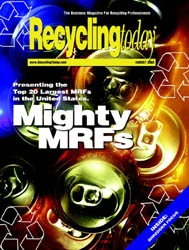
Explore the August 2002 Issue
Check out more from this issue and find your next story to read.
Latest from Recycling Today
- Athens Services terminates contract with San Marino, California
- Partners develop specialty response vehicles for LIB fires
- Sonoco cites OCC shortage for price hike in Europe
- British Steel mill’s future up in the air
- Tomra applies GAINnext AI technology to upgrade wrought aluminum scrap
- Redwood Materials partners with Isuzu Commercial Truck
- The push for more supply
- ReMA PSI Chapter adds 7 members