Keeping close tabs on a shredder's trouble spots can prevent costly downtime.
In today’s often-difficult business conditions, it is more important than ever to know how your recycling plant is performing. It is also vital to avoid sudden expensive breakdowns and to keep plant downtime to a minimum. This is particularly difficult in the scrap metal recycling industry, where auto shredding machinery must be capable of handling large vehicles with a high throughput.
At shredder yards, if the shredder is working well, then the plant is productive; and if the shredder is not working, then the plant is inoperative.
Under these circumstances, it is vital to be able to monitor the condition of the shredder motor and the shredder mill. There are two kinds of monitoring that can be helpful – online monitoring of productivity (motor run time and power consumption), and condition monitoring of the machinery itself.
MOVING BEYOND TRADITION
The traditional approach to condition monitoring has been to make use of handheld vibration analyzers, with data being taken once or twice a month. The drawback of this approach is that it does not detect problems that can develop rapidly, and the quality of data taken with these analyzers tends to be dependent on the process conditions.
This type of service gives information about machine vibration only, and it can be difficult to correlate the vibration with existing service conditions.
Recently, a major shredding plant in California (SimsMetal’s Redwood City plant) fitted its Alstom motor and Texas Shredder mill with a Motornostix Web-based online condition monitoring system. Vibration and temperature sensors were mounted at both ends of the shaft turning the rotor.
The Motornostix system makes use of a local data logger called a Canary unit. The Canary units are locally networked to a personal computer (PC), which acts as a bridge to the Internet. The data gathered by the Canary is hosted on a central database from where it can be served to users via a simple Web browser interface. Motornostix has a central database in Cincinnati that stores data from customers in the U.S., U.K. and Australia.
Because of site conditions at the shredder yard, SimsMetal would have had to perform extensive excavation of concrete to lay cable, so it was decided that a wireless link would be used to connect the Canary unit to the bridge PC. The wireless unit, based on a 2.4GHz spread spectrum radio and running a proprietary Motornostix protocol, was used to link the Canary unit to a PC in an office building about 100 yards away. This simplified the installation of the system.
GAUGING RESULTS
The new monitoring system has already proven itself to be of considerable benefit to the owners of the plant, both as a management tool and as a condition assessment system.
Because of the high cost of electricity during the day, actual production at this plant is carried out primarily on the night shift. The monitoring system allows SimsMetal management personnel to securely view all production parameters (e.g. motor run time, motor current, bearing vibration and bearing temperatures) from any location in the world using the Internet and a Web browser.
The monitoring software, while being primarily designed for condition monitoring, includes a number of management tools that can be extremely useful in cases like this. An example of the use of these tools involves the production of graphs demonstrating motor performance over a 24-hour period.
The graphs are designed to show the speed and current power consumption of the shredder motor for a 24-hour period, with a threshold analysis performed on each set of data.
Using a threshold tool in the software to set the threshold slightly above the no-load current for the machine, we see the motor has run for 47.8 percent of the period, which almost corresponds to the expected plant uptime of 50 percent.
However, if we perform the same analysis on the current and we set the threshold at 275A (the no-load current of the shredder system), the runtime is 40.6 percent of the period. Thus, for seven percent of the total time, or 15 percent of the actual running time, the system was idling under a no-load condition—no material was being fed into the shredder.
BAD VIBRATIONS
A second type of monitoring can show the vibration of the shredder mill bearing that lies closest to the motor. In one sample, vibration measurements for four days (four overnight shifts) showed that during the fourth shift the vibration had suddenly increased dramatically.
Monitoring showed that the primary vibration peak is at about 8.6 Hz, which is the running speed of the motor. The presence of this peak indicates a mechanical out-of-balance condition. The size of the peak indicates that it is of concern, and the increase from one day to the next suggests that the situation is deteriorating.
Using the information provided by the monitoring system, the plant engineers were alerted in suitable time to the imbalance state, and were able to open the hammer mill and correct the imbalance. Users of Motornostix software are also able to select, view and modify images available online, using only Internet Explorer as the software interface.
An online monitoring system for a shredder plant can offer improved plant performance and management information, as well as the opportunity to use remote condition monitoring.
The author helps design monitoring systems for Cincinnati-based Motornostix USA. He can be contacted via e-mail at jont@motornostix.com.
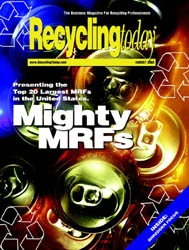
Explore the August 2002 Issue
Check out more from this issue and find your next story to read.
Latest from Recycling Today
- ReMA board to consider changes to residential dual-, single-stream MRF specifications
- Trump’s ‘liberation day’ results in retaliatory tariffs
- Commentary: Waste, CPG industries must lean into data to make sustainable packaging a reality
- DPI acquires Concept Plastics Co.
- Stadler develops second Republic Services Polymer Center
- Japanese scrap can feed its EAF sector, study finds
- IRG cancels plans for Pennsylvania PRF
- WIH Resource Group celebrates 20th anniversary