Electronic scrap appears ready to emerge as a new feedstock for recyclers and shredder operators.
When speaking about electronic scrap, why not borrow a term from the high-tech industry? The "new new thing" is a term popularized in a book about Jim Clark, founder of Netscape, which reflects the next best wave of change or opportunity.
I feel this label may fit the electronic scrap opportunities of today. But in writing this, it makes me think about what came before. After all, "new" implies something old. So what was old, and what may have been like this?
THE TIRE DILEMMA OF THE 1980s
Having been in the recycling/processing business for more than 24 years, it reminds me of the emerging scrap tire industry in the early to mid-1980s. Although the term the "new new thing" would not be coined for a few years, it was an opportunity fresh for innovation and gain.
Witnessing this earlier evolution and looking at the developments in electronic scrap, I see many similarities and a lingering reminder that not all tire processors have been successful. So, what might this mean to the emerging electronics recycling industry?
With tires, the need for processing began when tire generation exceeded standard means of disposal. Early tire disposal meant sending them to the landfill, dumping them along roadsides or, more commonly, stockpiling them in empty lots and ravines. The concern about scrap tires became of public interest after several large fires. There was also the concern for disease, as tires were considered breeding grounds for insects and vermin.
In either case—fire or disease—both were difficult to control. As such, environmental concern for tire disposal resulted in local and state governments creating regulations, which helped to support the development of a new industry.
Similarly, used electronics are being stockpiled. And although the health risk concerning electronics may not be as much a concern as tires, local and state governments are studying what part they can play to be sure that materials are handled and disposed of properly. This concern is not just driven by what is here today, but what is on the way.
A STOCKPILE IN WAITING
Consider the prediction for obsolete computers as stated in "The1999 Electronic Product Recovery And Recycling Baseline Report," prepared by Stanford Resources Inc. for the National Safety Council. According to this study, there are an estimated 50 million obsolete computer units being stored somewhere right now.
In addition, cell phones, stereo equipment, car components, TVs, and industrial and military components add annually to this amount. Like tires, electronic scrap, with the pent-up inventory and ongoing supply, creates opportunity. But converting this opportunity into profit is not a simple task.
Fortunately, electronic scrap is a more diverse commodity and has a greater demand for its sorted products. However, there is no assurance of success, and electronic scrap processing will likely find a path similar to the one scrap tire processing found.
FINDING THE DIRECTION
Borrowing from the experiences of the past, there are a few basic questions a would-be electronics recycler must ask: What sector of the market should one be in? What is the source of material? What product condition will receive the highest value?
As with tire recycling, the source of material is generally the easiest to answer. However, understanding this sector of the market and the required end products is essential to achieve success.
First, what market(s) do you plan to service—product destruction, volume reduction, recycling of whole electronics goods or all of the above? The market being serviced will largely drive the end product requirements, as well as the system or process required to support the business.
• Product destruction focuses on contracting with manufacturers to ensure that their off-spec/obsolete/returned goods are destroyed and don’t find their way back into the marketplace.
• Volume reduction is important for people who have a long way to haul their goods in order to get rid of them. This is a common market for electronics de-manufacturers who have a large volume of thermoplastic monitor housings and bulky terminal frames that have a lot of airspace in them.
• "Recycling" in the electronic scrap industry really means material liberation and separation. By reducing whole electronics down to their individual elements—separating the glass, steel, aluminum, copper and other materials high in precious metals content—recycling is quickly becoming the future of the electronics processing and recovery business
The key in this business is not to produce waste – everything is to be sold for a profit. Electronic scrap, as received, is like an un-mined ore. To retrieve the ore, it must be disassembled. Complete hand disassembly would yield the highest recycled value, but the cost per piece to do so would be prohibitive and ultimately stifle growth. Processing automation is the obvious alternative, and if designed correctly will provide the next best yield.
Recent advances in processing and separation technology have allowed for the introduction of mechanical equipment to address all segments of e-scrap processing.
GETTING THE JOB DONE
Complete recycling systems are now capable of producing well-liberated and separated materials at high enough production rates to service entire metropolitan areas. Integral to such systems are components such as shear shredders like those made by SSI Shredding Systems Inc., Wilsonville, Ore. These types of machines can provide a comparatively low-cost, high-volume, reliable solution.
How do you make such a system work for you? In the early years, tire processing systems development and equipment selections were often based on low entry-cost alone. Then unscheduled down time, high maintenance costs, loss of production and associated expenses caused many failures in scrap tire processing. The processing system is where the value is added.
It’s important to work with an experienced, qualified manufacturer or systems integrator who has a track record of successful installations. As each operation will be unique, it is vital that you fully understand your own expectations of the material to be processed, the throughput/capacity of the system, and the condition of the output materials. Allow for growth and flexibility; as with any emerging market, conditions will change and you will want to be prepared.
After all, getting a saleable product to the buyer—and off your floor in a cost-effective manner—is what pays the bills.
In the end, the "new new thing" isn’t really anything that new, is it?
Incidentally, the "new new" buzzword in the high-tech industry is nano-technology, where someday there will be nano-forges that will produce products atom by atom on a molecular scale. Where will recyclers be then?
Thomas J. Garnier is the founder and president of SSI Shredding Systems Inc., Wilsonville, Ore.
Get curated news on YOUR industry.
Enter your email to receive our newsletters.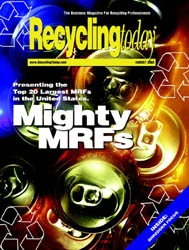
Explore the August 2002 Issue
Check out more from this issue and find your next story to read.
Latest from Recycling Today
- Athens Services terminates contract with San Marino, California
- Partners develop specialty response vehicles for LIB fires
- Sonoco cites OCC shortage for price hike in Europe
- British Steel mill’s future up in the air
- Tomra applies GAINnext AI technology to upgrade wrought aluminum scrap
- Redwood Materials partners with Isuzu Commercial Truck
- The push for more supply
- ReMA PSI Chapter adds 7 members