Different types of rotors can change the way an automobile shredder processes material.
The choices made by a company operating an auto shredding plant are numerous. Not only are there several different companies competing to sell
their brand of shredder, but even once a brand choice is made, there are several further considerations.
The more obvious ones include the size of the rotor and shredder housing, which types of hammers and grates to use, whether to run a damp, wet or dry shredding plant, and how much downstream sorting equipment to include as part of the overall system.
The rotor itself can also come in different varieties. Engineers and sales professionals at Lynxs Shredder Corp., Tulsa, Okla., created a "Shredder Selection Rotor Guide" to help customers understand the different rotor configurations and how they differ. Following are portions of the text of that guide.
The information in this story was edited from a guide produced by Lynxs Shredder Corp., Tulsa, Okla.
TOTALLY ENCLOSED BARREL ROTOR |
![]() Pros: • Discs of rotor are never exposed to scrap, resulting in longer service life • Minimum life expectancy of rotor is one million tons • Highest inertia of all rotor designs since the major mass of the rotor is at the perimeter • Better for light scrap such as cars and white goods Cons: • Not necessarily as good for number one scrap • Does not work in some shredder models due to their anvil location |
DISC ROTOR "WELDED" (HARD-FACED) |
![]()
Pros: • Moderate cost • Highly resistant to breakage • Very good for "all-around" or mixed variety of scrap feed Cons: • Higher maintenance costs per ton • Does not work in some shredder models due to their anvil location |
DISC ROTOR/"NO-WELD" | ||||
![]() Pros: • Resistant to breakage • Very good for "all-around" or mixed variety of scrap feed • Lower maintenance Cons: • High wear means very short life expectancy (100,000 tons) • Can have the highest cost per ton processed
|
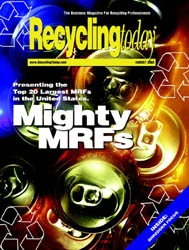
Explore the August 2002 Issue
Check out more from this issue and find your next story to read.
Latest from Recycling Today
- Athens Services terminates contract with San Marino, California
- Partners develop specialty response vehicles for LIB fires
- Sonoco cites OCC shortage for price hike in Europe
- British Steel mill’s future up in the air
- Tomra applies GAINnext AI technology to upgrade wrought aluminum scrap
- Redwood Materials partners with Isuzu Commercial Truck
- The push for more supply
- ReMA PSI Chapter adds 7 members