
Providers of auto shredding and accompanying downstream systems know repeat business is at stake when they undertake an installation or retrofit project. They thus put significant effort into ensuring the right machines are integrated into what can be very complex systems.
Buffalo, New York-based Wendt Corp. has been providing metal recycling equipment globally for more than four decades. The company develops its own equipment, forges alliances to market technology it judges as industry-best and keeps its door open to vendors who come to it with emerging technology.
Ethan Willard, business development manager of Wendt Corp., says the Shred1® ballistic separator developed and made by Eriez, headquartered in the neighboring state of Pennsylvania, has gained favor as a technology that can play a valuable role in many of its auto shredding installations.
“We’ve found adding the Shred1 solves a number of issues that our customers are facing, which I believe has led to its success,” says Willard. Those issues revolve around the need or desire to create a low-copper ferrous shred, says Willard, which he identifies as “a growing trend over the past five years.”
Willard continues, ”By installing the Shred1, we’ve seen great results in the quality of the finished ferrous shred. Specifically, the Shred1 allows our customers to easily achieve a low-copper shred.” The Shred1 delivers the improved chemistry in a labor-efficient manner, adds Willard.

“By concentrating the copper-bearing material into a single stream that is roughly 30 percent of the total ferrous volume, we are able to increase the picking efficiency on the ferrous downstream. This allows our customers to achieve low-copper shred and/or reduce their picking labor.” Adds Willard, “Combined with Wendt’s ferrous downstream polishing magnet, the Shred1 can reduce the need for a typical ferrous Z-box and cyclone.”
The Shred1 benefits have been clear enough to Wendt Corp. that it has been part of multiple installations. “We commissioned our first two Shred1s in March of 2015. This installation was a retrofit to a customer’s existing downstream. Since then, we have installed a total of 11 Shred1s as both modifications to existing downstreams and within new, greenfield projects,” says Willard.
Willard describes Wendt Corp. as “the leading North American manufacturer of auto shredding systems,” with three large (82- to 132-inch) shredder installations in the past three years and 20 of its modular shredders sold since the product line was introduced in 2013. He says Wendt Corp. is pleased with the Shred1 based on extensive experience.
“Measuring its effectiveness is quite simple: Did it satisfy the goals we set out to achieve? ... [T]he answer is yes,” states Willard. “Our customers have been able to achieve low-copper shred packages with the Shred1.”
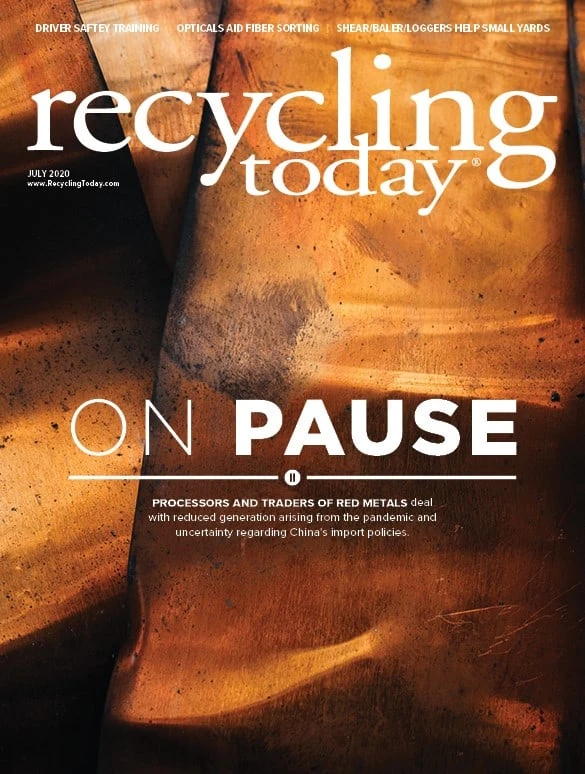
Explore the July 2020 Issue
Check out more from this issue and find your next story to read.
Latest from Recycling Today
- Aqua Metals secures $1.5M loan, reports operational strides
- AF&PA urges veto of NY bill
- Aluminum Association includes recycling among 2025 policy priorities
- AISI applauds waterways spending bill
- Lux Research questions hydrogen’s transportation role
- Sonoco selling thermoformed, flexible packaging business to Toppan for $1.8B
- ReMA offers Superfund informational reports
- Hyster-Yale commits to US production