Richard Jaross has been a shipbreaker since 1969. Just don’t call him a shipbreaker.
"We are recyclers, not shipbreakers," says the president of Esco Marine. "We’re an environmental firm first and a scrap dealer second. Environmental and safety issues are our first line of business. We literally offer a ‘cradle-to-grave’ service."
From the firm’s main facility at the Port of Brownsville, the southernmost city in Texas, Jaross has overseen the dismantling of more than 500 ships. There, Esco has three 800-foot breaking slips, and 3,945.50 feet of frontage on the deepwater Brownsville Ship Channel gives it room to work on more than nine large ships (Esco’s approximate annual production) at the same time.
BEHIND THE SCENES. Impressive as it is, the site’s main work goes on unseen to most of the 400 employees. Esco’s success is in light of its highly trained workforce and management staff. Its CEO, Rafael Carrasco, handles overall management of the company. C.J. Mire, EH&S manager, oversees the highly skilled workforce tasked with environmental and safety matters. Kris Wood, contracts and logistics manager, oversees the administration of the dismantling contracts, including submission of required reporting as well as the operation of Esco’s tug and barge line. Mike Furgatch, yard operations manager, and Ronald Mills, shipboard operations manager, oversee the physical dismantling process. Andy Jaross, facilities and equipment manager, oversees all construction projects and maintenance of more than 130 pieces of equipment."Fully 100 of our employees are involved in environmental remediation," says Jaross. "That’s asbestos, PCBs, mercury and oils. We even have a lead program to deal with the traditional gray paint used in U.S. Navy ships. Of course, the air is constantly monitored."
While ships are towed to Esco with relatively empty fuel tanks, bilge tanks are not so clean.
"We have an oily water separation (OWS) facility," notes Richard. "In it go engine and hydraulic oils, rainwater and process water. We sell the oil product and the clean water goes into the local sewer system. We even filter the wastewater from our employees’ shower and laundry room prior to allowing it to be discharged.
The ever-in-motion Richard is quick to point out that not one torch is put to a ship until that vessel is completely clean. And once that remediation is complete and all hazardous material accounted for, the recycling process is relatively simple: large squares are cut in the hull for ventilation, the ship’s bridge and bow are removed and then it’s pulled up a dry incline where "we remove everything but the squeal."
Workers cut the ship apart, pieces are removed by scale-equipped cranes and the material is sorted and prepared in the yard. Every product is weighed again before shipping by virtually every possible conveyance. Besides using rail and truck, Esco owns eight barges and three tug boats—one of them ocean going.
"The cost of a tow can be a million dollars or more and can take up to 45 days from the West Coast," notes Jaross. "Last year we towed through three hurricanes."
A portion of the firm’s product goes by barge to mills in Texas, Louisiana and Alabama. Finished product (wire, coil, etc.) can be backhauled to Texas, allowing Esco to maximize use of its equipment. Esco also ships into mills in Mexico via rail.
"Maximum utilization of equipment" is critical to the firm, according to Richard’s son Andy, who oversees Esco’s yard fleet as facilities manager.
KEEPING THINGS MOVING. "We have to cut, prepare and ship material, and machines are used in every step. That process is disrupted if a machine goes down, and we certainly don’t underestimate the impact that can have on the business," Andy says.To minimize problems, Esco relies on the general theory of "use new machines and maintain them." Much of its almost exclusive Caterpillar fleet was purchased through a barter deal with Caterpillar World Trade. Essentially, Esco receives new machines and pays for them with scrap.
"It’s a great program," says Andy. "We essentially trade scrap for machines. It’s allowed us to keep production at its maximum while at the same time reducing our maintenance costs."
Esco’s fleet includes Caterpillar material handlers, the largest of which is a 385B equipped with a 1,200-ton Genesis shear, wheel loaders, hydraulic excavators, trucks and a track-type tractor. But, as Andy emphasizes, having quality equipment is one thing, keeping it productive is another.
"We have a maintenance program that provides us not only great uptime, but maximum resale value. We handle daily lubrication and fluids, but use our Caterpillar dealer (Holt Cat) to do regular preventive maintenance on the machines. It’s the best of both worlds: maximum production, minimum maintenance costs."
Machine availability is important to Esco. It allows it to maintain production of 5,000 tons to 10,000 tons of ferrous and approximately 200 tons to 300 tons of nonferrous materials monthly.
"U.S. Navy ships, which account for about 60 percent of our business, contain more nonferrous than a cargo ship," notes Richard. "Warships, such as a heavy cruiser we just recycled, had 8-inch-thick armor plating. That contained a high percentage of nickel."
Esco’s main clients are the United States Maritime Administration (MARAD) and, of course, the U.S. Navy. The Navy Sea System Command, in fact, maintains an office at the Esco facility. In addition to those sources, Esco Marine will buy two or three commercial vessels per year.
"Those come from constructive total losses (CTL), the oil industry and other commercial vessel operators who need to properly dispose of their vessels," says Richard.
He emphasizes "properly dispose" and says he sees the day when ship owners will have to recycle their ships in "green" yards. This will be a critical step for the industry, which now sees the bulk of ship breaking taking place in yards along the Gulf of Khambat in India. Ships there are beached at high tide and manually dismantled.
"MARAD and the Navy insist on adherence to the highest environmental and safety standards for their vessels," he says. "We have the management, the equipment and the trained workforce to meet those standards."
Like any recycling yard, Esco measures its production in the tons of material that leave the yard. But in the ship recycling business, there’s an added element: nautical items. Richard’s office, for example, resembles a mini-museum with artifacts removed from ships throughout the years. And any Navy veteran would feel at home in the company’s dining room, with its standard issue chairs and dishes direct from a Navy ship. But not all those items are just in the offices.
"We have a retail store where we sell anything that could bring above scrap value," notes Richard.
That store (store.escomarineinc.com) is actually a warehouse with an ample outside display area for a wide variety of items. Among the items shoppers can find are nautical antiques, rope ladders, bins of portholes ($10 an inch), gunner’s helmets and galley equipment, from dishes to mixers to cooking kettles to freezer doors. There’s even the original teak wood deck from the U.S. Navy heavy cruiser Des Moines, which ESCO recently finished dismantling.
EXPANDING FOCUS. Despite almost 40 years in the ship recycling business, Richard is not content to sit back and rely on ships alone. The company has six-acre "feeder yards" in Brownsville and Matamoros, Mexico (15 miles from Brownsville), along with a 12-acre yard in Donna, Texas, some 60 miles from Brownsville."From those yards we take over-the-scale materials, commercial, industrial and consumer scrap," says Richard. "We semi-process it on site and then ship it to the main yard here at the port for shredding, shearing or further processing before sale. This part of our business should increase significantly over the next year. And we recently installed a rail switch and spur so we can begin bidding on obsolete railroad cars for dismantling."
Also new to the yard is a shredder that adds up to 8,000 tons per month. The shredder is used to shred automobiles (which the company has been stockpiling), household appliances as well as light tin. Esco started up the shredder in August.
"We anticipate the shredder will provide a good and steady source of revenue," Richard says. "This metropolitan area has more than 1.5 million people and is in desperate need of a fully integrated ‘green’ scrap processor capable of handling the growing market of industrial and domestic scrap," he adds.
Richard loves to travel. He’s visited shipbreaking sites around the world, including those in India, and he travels the world consulting on the business. He’s also taken a few cruises. Magnet in hand, he’ll walk the ship, always awed by the large amount of plastic it contains.
Ask Richard if he spends time on the cruise ship wondering how he’d dismantle it, and you’ll get a pause followed by, "Well, a little. Hey, it’s what I do. It’s all I could ever see myself doing."
This story was submitted on behalf of Caterpillar Inc., Peoria, Ill. The author can be contacted at BarnettSolutions@hotmail.com.
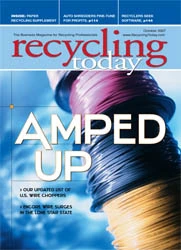
Explore the October 2007 Issue
Check out more from this issue and find your next story to read.
Latest from Recycling Today
- European project yields recycled-content ABS
- ICM to host co-located events in Shanghai
- Astera runs into NIMBY concerns in Colorado
- ReMA opposes European efforts seeking export restrictions for recyclables
- Fresh Perspective: Raj Bagaria
- Saica announces plans for second US site
- Update: Novelis produces first aluminum coil made fully from recycled end-of-life automotive scrap
- Aimplas doubles online course offerings