Iron foundries feel the heat from competing aluminum operations as both metals chase the automotive market.
As hot and irresistible as molten iron pouring from a ladle into a mold, two trends will drive the automotive foundry business in the coming seven to 10 years. Those trends will push aside everything in their way and will set the tone for recycling opportunities in coming years.
First, most auto manufacturers will outsource as much of their foundry operations as they can, retaining only key components in house. Second, the mix of materials coming out of auto-related foundry operations will continue to move inexorably from iron to aluminum.
Many iron and aluminum recyclers, especially in the industrial North and Great Lakes region, live and die with automotive production. There has been a gradual shift among automakers from producing material in-house to outsourcing foundry jobs.
"Over time, we all expect there to be less captive foundry operations and more outsourcing," says Mike Lessiter, marketing director for the American Foundry Society (AFS), Des Plaines, Ill.
A Mixed Blessing
It’s a mixed blessing for recyclers. If you are one of the fortunate ones who has a tight relationship with a GM engine plant or Ford casting operation, your fortunes may ride on the health of the auto market, but at least you can be fairly sure of seeing a steady flow of outbound material.
Shifting Sands |
At DaimlerChrysler, the issue of sand for the foundry is more immediate than concern over either scrap iron or possible encroachment of aluminum into the market. “It’s always been a challenge getting good quality sand,” Bowers says. “We are aggressively looking at re-using or recycling our sand.” Sand for use in the foundry comes from the dunes area of Lake Michigan. The dunes area is environmentally fragile. “We want to be a good customer and a good neighbor,” Bowers says “It is a concern to both the environmental officials at the plant and at corporate headquarters.” Not only will recycling the sand be the right thing to do environmentally, but it also promises to save DaimlerChrysler big money, Bowers says. “Being in the forefront of this is an absolute must if we are going to stay in business and do the right thing,” he adds. |
When a manufacturer outsources foundry work to several plants in a region, there is increased opportunity for recyclers to find more business. However, the competition to ship scrap to these scattered operations can be intense and requires a lot more work.
The growing presence of aluminum in autos means shredder operators will need to keep preparing to see more aluminum and less ferrous material.
According to the AFS, the typical vehicle in 1980 included 650 pounds of gray iron. By 2001, that figure had dropped to 280 pounds. "We believe it could go down another 100 pounds over the next 10 years," Lessiter says.
The big winner will be aluminum. The "average" engine block currently being built is 30 percent aluminum. By 2009, the AFS forecasts the typical block to be 74 percent aluminum.
Cylinder heads already are 85 percent aluminum. By 2009, aluminum will make up 98 percent of all cylilnder heads—virtually the entire market.
This percentage varies by product line and by the manufacturer, and is likely to continue to vary for the foreseeable future. At General Motors, for example, blocks currently average 25 percent aluminum and 75 percent gray iron.
Robert Bowers, plant manager at the Indianapolis DaimlerChrysler foundry, is not too concerned about aluminum for the short term – a period he defines as running through the rest of the decade – at his operation.
"We don’t see that in our product portfolio for the next five to 10 years," he says. "Gray iron is in our product portfolio for the next 10 years." He admits that there is concern about losing ground to aluminum castings. "Ever since aluminum was introduced, it was a concern that gray iron would be minimized," Bowers says. "It’s not an overwhelming concern right now." However, he says everyone at the foundry is aware of the potential for aluminum.
For the auto manufacturers themselves, foundry production hinges on sales. "The last two years of record-breaking vehicle sales have kept the business relatively stable at GM foundries," says J. Michael Williams, GM Powertrain Manufacturing Manager, Component Operations.
Finding the Foundries |
(States with the leading percentage of foundry product shipments, 2000) Ohio 15.0% Alabama 11.6% Wisconsin 11.4% Indiana 11.2% Michigan 8.0% Source: American Foundry Society. |
Changes at Ford
Historically, a company does not simply build or tear down a foundry to meet the ebb and flow of the marketplace. But even that seems to be changing. Ford Motor Co. deployed a brand new aluminum center in 2000: a precision sand casting operation. Surprisingly, the operation, known as the Cleveland Aluminum Casting Plant in Brook Park, Ohio, is already slated to be closed.
By the end of 2003, the Cleveland area will see the closing of Ford’s Walton Hills Stamping Plant, the Aluminum Casting Plant in Brook Park and an assembly plant in Lorain, Ohio. And, Ford says it will close its Vulcan Forge Casting Plant in Dearborn, Mich.
Ford recently sold its Canadian aluminum operations to Nemak, which now is known as Nemak-Canada, located in Windsor, Ontario. The Ford-Nemak relationship is a long-standing one. Ford appears to have decided that a foundry-specific group can do a better job of producing parts than it could do in a captive plant.
The announced closing of the year-old Brook Park operation shocked many in the business, but the auto company decided the plant was simply too small to be efficient.
More typically, auto manufacturers seem intent on keeping the manufacture of particular key parts in house. These generally are the components that the company feels give them some strategic advantage in the marketplace.
"We are focusing on producing key powertrain castings at our sites—cylinder blocks and heads, crankshafts, for example," Williams says.
This is typical of the strategy taken by most automakers. Foundries building engine blocks and heads usually are kept captive. Other components are more likely to be farmed out to independents. The top five states for foundry shipments are Ohio, Alabama, Wisconsin, Indiana and Michigan.
Lessiter notes that there have been some major investments by the Big Three recently, beyond the short-lived Ford aluminum operation. GM built a lost foam casting facility, for example. (This process keeps foam inside the mold as the hot metal moves in to replace it.)
Not all foundry capacity is new, however. DaimlerChrysler’s Indianapolis foundry has been in company hands for almost half a century and continues as an important location. Formerly American Foundry Co., Chrysler purchased the business in 1946 and operated it as a wholly-owned subsidiary. It was designated a Chrysler plant in 1959 and underwent major expansions in 1964, 1978, 1988 and 1996. It is one of only two foundries in the U.S. with Q14001 environmental certification.
The foundry produces cast iron blocks for engines ranging from the 2.0 Liter, I-4 to the 3.3/3.8 Liter, V-6 Engines and the big 4.7 liter, V-8 Engines used in company products. When the new 3.7 was introduced last year, production of the 2.0 liter engine was dual-sourced out of the Teksid operation in Brazil.
Bowers says the foundry melts 72 tons per hour or about 600 tons per day. "We produce about 5,300 blocks per day," he says. Everyone is optimistic about the 2003 model year. "We’re running close to maximum capacity but we could go up a bit as we move forward," Bowers says.
Use of scrap materials is a major part of the game plan at the Indianapolis plant. The materials consist of scrap, cast iron, as well as pig iron and their own prompt scrap material mixed in. "We get scrap iron and cast from outside," Bowers says. "We buy about 10 percent pig iron. We remelt some scrap castings into that," he continues.
Scrap quality is always a concern, but has not been a problem for Bowers. "We do evaluate scrap as we receive it," he says. "We audit the material as it comes in. It generally is pretty good. We have a good relationship with our dealers." Bowers says he does not see any shortfall of scrap in the near future.
Honda Scrap Forecast is Up
At Honda of America Manufacturing, Marysville, Ohio, North American production of vehicles for the current fiscal year is forecast to be up 5.5 percent. That will translate, roughly, into a 5.5 percent increase in scrap output, but not direct scrap consumption.
There should be some uptick of secondary metal consumption, though. For example, Chris Petersen, manager of Honda Trading’s Raw Materials Group, notes the company purchases aluminum castings made from spec metals. As a result of Honda’s increased demand, the smelters will be buying more scrap to meet the orders sent in.
"If the economy falls, that may change," says Petersen. Honda’s marketing philosophy is more conservative than that of the Big Three, says Petersen, and the company has not seen any big drop-off in sales.
Honda sources its raw material supply both in-house and from first and second tier parts makers. Aluminum, plastic, steel sheet and steel bar are among the key components.
Petersen says he sees no shift in the in-house production either away from or in favor of outsourced materials.
Wabash Alloys, Wabash, Ind., is the major supplier of aluminum to Honda’s Ohio operations. Aluminum casting is done at the firm’s engine plant in Anna, Ohio. Raw plastic pellets are purchased from a variety of sources.
Q&A with GM |
J. Michael Williams, the GM Powertrain Manufacturing Manager of Component Operations, offers his view on the automaker’s foundry operations. Q. Are GM foundries less busy from the high levels of 1999-2000? A. The last two years of record-breaking vehicle sales have kept the business relatively stable at GM foundries. Q. Is there a trend at GM to outsource foundry capacity or to keep it in house? For example: Producing blocks and heads in-house, and outsourcing axles. A. We are focusing on producing key powertrain castings at our sites, [such as] cylinder blocks and heads and crankshafts, for example. Q. What are the trends in materials? For example: Moving away from gray iron to aluminum. A. Yes, the trend is for movement from iron to lighter weight material, such as aluminum. This is driven by the need to improve vehicle fuel efficiency. Q. What is GM’s general overall view of capacity industry-wide? A. My perspective is that with the shrinking of the foundry industry, capacity is pretty well utilized. There is not excess aluminum capacity for strategic components. There is some iron excess capacity. Q. What is the percentage of GM’s use of cast iron and aluminum? A. This varies by product line. For example, blocks are currently 25 percent aluminum and 75 percent gray iron. |
"One commodity that is growing overall is plastics," Petersen states. He cites the need for lightweighting autos as the reason for the trend. "Plastics are displacing steel or aluminum in our autos," he says.
"My perspective is that with the shrinking of the foundry industry, capacity is pretty well utilized," says Williams. There is a bit of a difference between materials, however. "There is not excess aluminum capacity for strategic components," Williams says. "There is some iron excess capacity."
Part of that is due to the changing makeup of the automobile. Change, however, does not necessarily mean bad news. The AFS projects a modest rebound in castings sometime in mid-2002. The industry enjoyed an unprecedented run, culminating in a 19-year shipment high in 1999, followed by a 10 percent drop-off in 2001.
Given there is nothing in the political situation that sends the economy into a tailspin, the next couple of years look good for the foundry business and the scrap dealers who supply them. The Society projects "a series of boom years" in 2003 and beyond.
The author is a contributing editor to Recycling Today and can be contacted via e-mail at .
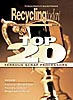
Explore the March 2002 Issue
Check out more from this issue and find your next story to read.
Latest from Recycling Today
- Balar Equipment to operate under Enviro-Clean Equipment name
- Li-Cycle reports 2024 financials
- Wisconsin Aluminum Foundry acquires Anderson Global
- PureCycle, Landbell Group working to advance PP recycling in Europe
- S&P Global launches mixed plastic scrap pricing for US, Europe
- Organizations call for coordination on product safety
- Circular Services acquires Waste Recycling Inc.
- Aqua Metals issues 2024 progress report