B&B Wrecking & Excavating, Cleveland, has been working since mid-January to demolish a portion of Elkem Metals Calcium Carbide Business Unit, Ashtabula, Ohio. Brian Baumann, vice president of operations for B&B, expects the project to take approximately five months and to yield significant quantities of structural steel, copper and aluminum scrap.

The demolition project includes five buildings and two water towers at the Elkem site on Lake Road, about half a mile from the plant’s main gate. Baumann says the combined structures that are part of the job measure 225,000 square feet. The structures housed a steel-making furnace at one time, Baumann says. "When it was built, at the time, it was the largest furnace of its type in the world," he adds.
Elkem has sold the property, Baumann says, and once the location is cleared it will be the site of an ethanol plant.
METALS HARVEST
"There are about 4,000 tons of steel and about 50,000 pounds of nonferrous copper and aluminum," Baumann estimates regarding the job. Most of the steel is structural, though there is some lighter material that can be baled, he says. The copper and aluminum come from the electrical components.
A crew of six – one truck driver, two laborers and three operating engineers – works on the Elkem project, processing approximately 100 tons of steel daily.
In terms of timing, B&B is enjoying the benefits of improved secondary metals markets. "We got an up market in February and March," he says. "April looks to be sideways."
B&B prepares about 30 percent of the steel from the Elkem demolition site, shipping it directly to steel mills. B&B ships the remaining 70 percent of the steel to two area scrap yards, Baumann says.
He says a shear is a necessity for the Elkem project. "You wouldn’t be able to do the job without a shear, really."
The shear in use at the Elkem project is a LaBounty MSD100 mounted on a Caterpillar 350 excavator. The Cat 350 is equipped with a 65-foot, high-reach demolition set-up, Baumann says. B&B also has two Komatsu PC-300 excavators equipped with LaBounty grapples on site, as well as a Komatsu PC-220 excavator with a LaBounty grapple and a Cat 235 crawler excavator outfitted with a LaBounty UP90 Universal Processor.
Baumann says he purchased B&B’s first LaBounty attachment because of the manufacturer’s reputation for quality and longstanding involvement in the industry. LaBounty is celebrating its 30-year anniversary in 2003. He says he bought additional LaBounty attachments because of their high production, reliability and spare parts availability.
|
"Everything breaks in this industry," Baumann says. "The important thing is that you can get spare parts quickly and at a fair price."
UP TO THE JOB
In regard to B&B’s LaBounty MSD100 shear, Bauman says, "I feel that the LaBounty MSD100 shear is durable, reliable and does not require a lot of maintenance. It was well engineered to work in the scrap and demolition industries."
The mobile shear is suitable for excavators in the 90,000-pound class. It has an opening of 38 inches, a depth of 39 inches and a reach of 11 feet, 6 inches. The shears are specifically designed for scrap processing, demolition work and bridge and road reconstruction, according to LaBounty literature. The MSD100 is capable of cutting H- and I-beams, plate, pipe, wire and rebar.
Baumann uses the MSD shear to cut straight I beams and sheet steel at the Elkem project. However, he needs a rotating shear for angled beams. This is where the UP 90 proves a capable tool.
The UP 90, categorized as a universal processor, is intended for use with excavators in the 100,000-pound range. Universal processors enable various jaw options for maximum efficiency. Shear, concrete pulverizer and concrete cracking jaws are available with this model with openings of 42 inches, 60 inches and 72 inches and cutting depths of 31 inches, 38 inches and 44 inches respectively.
"The UP 90 shear actually rotates and allows me to cut steel that has a lot of angles to it," Bauman says.
While the shear of the UP 90 is not intended for full-time scrap metal processing, the shear jaws are good for processing steel from demolition sites, according to Bauman. According to LaBounty literature, the UP can replace the bucket or stick of an excavator. It requires two hydraulic circuits to operate: one for opening and closing and one for rotation.
The LaBounty grapples B&B has on site at the Elkem project are models 140 and 120 from the HDR line. These grapples have a two-tine upper half and a three-tine lower half. The grapples are not specifically designed for scrap applications, though LaBounty does manufacture grapples that are. Baumann says he did not choose to purchase the scrap grapples because they do not fit most of his day-to-day applications. While these demolition grapples may not be as efficient as the scrap grapple in regard to the Elkem project, Baumann prefers the versatility they lend to a range of projects.
While Baumann stresses that each job varies somewhat, B&B recently completed a similar demolition job near the ISG steel mill in Cleveland (formerly LTV Steel) that involved tearing down storage facilities and furnaces and produced a similar material yield.
"I’ve got 10 jobs going right now," he says. "We just completed a bridge demolition in Elyria. We have a couple of schools; one is in Chillicothe and one is in Youngstown." Baumann adds that these jobs vary from the Elkem and ISG projects in that they yield more secondary aggregate construction and demolition debris. B&B is recycling the concrete from these jobs using portable crushers.
Getting back to the Elkem project, Baumann says, "It’s going really well. We’re very happy with the equipment, and we’re very happy with the customer. It’s definitely a good winter job."
The author is assistant editor of C&D Recycler and can be reached at dtoto@cdrecycler.com.
Get curated news on YOUR industry.
Enter your email to receive our newsletters.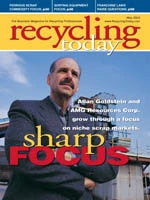
Explore the May 2003 Issue
Check out more from this issue and find your next story to read.
Latest from Recycling Today
- ReMA opposes European efforts seeking export restrictions for recyclables
- Fresh Perspective: Raj Bagaria
- Saica announces plans for second US site
- Update: Novelis produces first aluminum coil made fully from recycled end-of-life automotive scrap
- Aimplas doubles online course offerings
- Radius to be acquired by Toyota subsidiary
- Algoma EAF to start in April
- Erema sees strong demand for high-volume PET systems