
The story of the past several decades of scrap recycling in the United States—and indeed around the world—includes the growing presence of auto shredders. As ferrous shred became a desired grade for steelmakers, companies that operated shredders often found themselves with a sizable market share and market pricing advantage.
Not all scrap recyclers had the scale or the desire to operate shredders. The holdouts, though, often found their ongoing participation in the market subject to their ability to accept the terms of the nearest shredding plant operators (or of operators of large stationary shears). Depending on a scrap company’s geography, selling directly to a steel mill or iron foundry often was not an option—especially as those sectors consolidated.
Small scrap companies faced limitations not only in how far they could ship their scrap but also in how quickly they could process it. This caused them greater exposure to ferrous and nonferrous price swings.
The dilemma played out differently for some scrap firms compared with others. Some sold their companies, and others made the plunge into the shredding sector. Others, however, may owe their ongoing independence to an alternative processing machine: the shear/baler/logger (SBL).
One supplier of these machines, Sierra International Machinery of Bakersfield, California, and one of its recent SBL customers, B&S Scrap Recycling of Hudson, Maine, have shared their companies’ points of view as to how the SBL has played a role beyond that of mechanically squeezing and cutting scrap metal.
Taking the stage
The SBL was introduced in the 1980s, says John Sacco, president and co-owner of Sierra. He says Sierra played a key role in that introduction and has benefited from the 60 years of experience gathered by its sister company, Sierra Recycling and Demolition, also of Bakersfield.
The SBL “was a big game-changer for the industry because it was a machine that could shear, bale and log scrap, and it was the first of its kind that gained market acceptance,” he says.
A former chairman of the Institute of Scrap Recycling Industries (ISRI), Washington, Sacco expresses confidence the SBL extended the life of some of that association’s existing and potential member companies that may otherwise have found it difficult to maintain independence.
“The shear/baler/logger gave small and medium-sized scrap processors the ability to compete against big yards with its ability to process in three different forms,” he says. With their new processing options, these companies “were able to control their destiny by processing their scrap and going mill-direct instead of having to ship to the large processor, who was the only one who could afford the shredders or the big shears and big balers.”
Sierra’s current line of SBL machines includes 10 models described on its website, including the T556SLK model purchased by B&S Scrap Recycling in Maine. That model can take in auto bodies, appliances and “loose tin” (things made of sheet metal) and compress them into logs that can be cost-effectively transported to shredding plants.
“Before getting this machine, we had to wait for our buyers to come and crush, and this could take several weeks, making us very vulnerable to market swings.” – Joseph Pinkham, owner, B&S Scrap Recycling
The logs produced typically weigh 1,400 pounds and are 32 inches by 34 inches by whatever length the operator chooses to shear them. Sierra lists the T556SLK’s output as being in the 14-to-16-tons-per-hour range.
Beyond logging, the SBL can shear denser forms of scrap (such as pipe and beams) at a 12-to-16-tons-per-hour clip, and it can produce 900-pound bales at a rate of some 10 to 14 tons per hour.
A variety of advantages
Joseph Pinkham, the owner of B&S Scrap Recycling, says his company took delivery of its T556SLK SBL in January and “after several days of assembly and training, we started running material.”
Among the traits Pinkham likes about having an SBL is the variety of material that can be fed into it. “We have run light iron, car bodies, unprepared No. 1 heavy melting steel (HMS), as well as aluminum and stainless steel,” he says.
Whichever of the three functions he is using, Pinkham is grateful for the higher rates of output he is seeing compared with the equipment he used previously. “This machine has the ability to process material very quickly, so therefore we can turn quicker profits. This helps with cash flow. Before getting this machine, we had to wait for our buyers to come and crush, and this could take several weeks, making us very vulnerable to market swings.”
The automated SBL also has allowed Pinkham to deploy his workforce differently. “About 70 percent of the No. 1 HMS unprepared that comes in can be sheared or baled, freeing up our torch guys to do other things,” he says.
On a day in early April, Pinkham remarks, “A perfect example is today here in Maine we had heavy rain all day, so our guys who normally work outside worked in our warehouse processing nonferrous material. I personally sat in a material handler with the remote and processed several tons of material using the SBL.” He adds, “The remote control is a very important feature; it allows one person to operate this machine.”
The multiple functions of an SBL allow B&S Scrap Recycling to purchase a wide variety of materials while engaging in less torch cutting. Additionally, Pinkham says, the company can sell what it has prepared to a greater range of potential buyers.
“I liked the shearing feature the best at first, but after learning the capabilities of this machine, I realized a lot of the unprepared No. 1 HMS could be baled instead of sheared,” Pinkham says. “Shearing uses a substantial amount more fuel than baling, as well as [creating more] wear and tear on the shear blades,” he adds.
Although he has operated the unit for just a few months, he says the maintenance the SBL requires has not proved intimidating.
“As far as maintenance, pretty much keep it greased and the oil and filters changed as recommended,” Pinkham says. “Also, keep material cleaned out from around the machine, especially behind the main cylinder that pushes the material.”
As a small operator away from a large population center, B&S Scrap Recycling is unlikely to push the output limits of its SBL, but Pinkham says that will create yet another advantage for the company.
“We’ll process approximately 4,000 tons per year through this machine, which is a small amount of its capability,” he states. Importantly, though, he adds, “We expect to get 20 to 30 years of use from this machine.”
Get curated news on YOUR industry.
Enter your email to receive our newsletters.
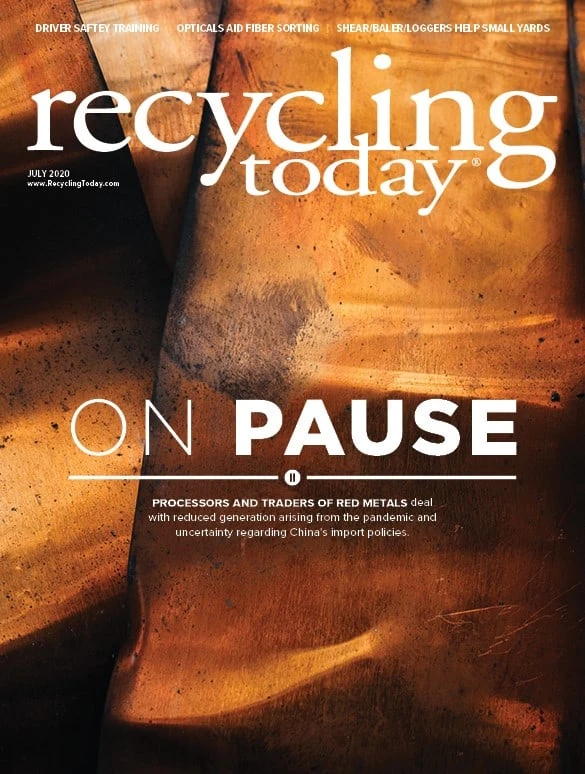
Explore the July 2020 Issue
Check out more from this issue and find your next story to read.
Latest from Recycling Today
- Nucor expects slimmer profits in early 2025
- CP Group announces new senior vice president
- APR publishes Design Guide in French
- AmSty recorded first sales of PolyRenew Styrene in 2024
- PRE says EU’s plastic recycling industry at a breaking point
- Call2Recycle Canada, Staples Professional expand partnership
- Circular Services breaks ground on north Texas MRF
- Tariff uncertainty results in choppy nonferrous scrap flows