Allan M. Goldstein grew up in New Jersey admiring the incredible work ethic
of his father, who serviced scrap metal generators working most of his life from
his scrap collection truck. His father’s hard work helped put Goldstein
through both college and law school, leading to a career as an attorney specializing in merger and acquisition law.
Having established a career as an attorney, Goldstein appeared to have left the scrap industry behind as a memory associated with his late father. But an acquisition deal in which he was involved in the late 1980s started Goldstein on a path that has seen him instead leave the legal world behind in favor of a renewed involvement with the scrap recycling industry.
AMG RESOURCES CORP. SNAPSHOT |
Corporate headquarters: Pittsburgh, Pa. Year established: 1988 De-tinning facilities: Pittsburgh; Baltimore; Gary, Ind.; United Kingdom (2) Additional scrap facilities: St. Paul, Minn.; Baltimore; Newark, N.J. (2); Milwaukee; Fort Dodge, Iowa; St. Joseph, Mo.; Lathrop, Calif.; United Kingdom (also a smelting operation in the U.K.) Brokerage Offices: Birmingham, Ala.; Phoenix; Shelton, Conn.; Brookline and Mill River, Mass.; Matthews, N.C.; Bethlehem, Pa.; Seattle; United Kingdom (2); there are also brokerage offices at all plants Additional services provided: Scrap management services for industrial generators; mill and foundry services; transportation (trucking and railcar) services; scrap substitute procurement; analyzing/quality control management |
OPPORTUNITY KNOCKS. Goldstein’s familiarity with the metals industry re-ignited when, in 1987 and 1988, he was involved with acquiring the de-tinning assets of Birmingham, Ala.-based Vulcan Materials Co. "When we began planning the deal, I didn’t think I would be running the company," recalls Goldstein. "But it was a long sales process, and many of the managers I thought I would have weren’t able to wait out the process and were not in place when the deal was completed."
With leadership of Vulcan’s three U.S. and two U.K. facilities defaulting to him, Goldstein found himself back in the metals industry, operating the Vulcan plants under the newly-designated AMG Resources Corp. name.
While he may initially have been a leader by default, subsequently he has helped turn AMG Resources Corp., Pittsburgh, into a large-volume scrap recycler with facilities throughout North America and the United Kingdom.
The company has grown and thrived in part because of Goldstein’s ability to make savvy acquisitions and also because of his willingness to pursue ideas proposed by research and development (R&D) professionals and other senior executives.
The combination of the two traits has let AMG acquire and establish facilities that use new technology to capitalize on what many would consider non-traditional or experimental scrap niches.
LEFTOVERS AS A MEAL TICKET. The shape that AMG has taken is constantly evolving, but much of its early history shows a track record of innovation.
|
De-tinning itself is what Goldstein calls "a niche market," and one that requires technical expertise. "Just for de-tinning, we already had a huge R&D department working on different methods for densification and processing," he notes. The chemical de-tinning process has long been used to create clean grades of steel scrap and high-purity secondary tin ingots from industrial tin-plated scrap.
AMG, however, has allowed its U.K.-based de-tinning researchers to experiment with the process so that its facilities can also accept and process post-municipal tin-plated steel cans for de-tinning.
"We developed a process that takes contaminated cans and produces a 98 percent pure ferrous product for de-tinning or as a feedstock," he comments. The product is consumed by both integrated mills and electric arc furnace (EAF) mini-mills.
Funding and encouraging R&D personnel has been a key in letting the company enter the other niche areas in which AMG has a presence, such as the handling of metallic scrap generated at incinerators and waste-to-energy plants. "We have migrated into what I call ‘first cousin’ areas," says Goldstein. "We build a presence in a lot of these niche areas rather than running large, traditional scrap yards."
The company’s model plant that obtains its feedstock from waste-to-energy plants is located in Minnesota, a state that Goldstein indicates "is at the forefront of good environmental practices." Several plants in the state produce fuel pellets made from residential trash. The waste-to-energy process also produces metallic scrap that is not suitable to be part of the pellets.
In a process developed and enhanced by AMG researchers, the residential trash is shredded, but before it is burned it is conveyed under an overhead magnet that attracts the ferrous portion. The result is heavily contaminated ferrous residue.
AMG developed and patented a unique shredder used at the plant not only to downsize material, but also to help separate ferrous and nonferrous metal from attached materials. A post-shredder air classification system helps separate metals from nonmetallics, while a magnet then separates ferrous from nonferrous metals.
The result on the ferrous side, says Goldstein, is "a steel pellet that one would think came from virgin steel, but it’s made from magnetized trash." Establishing the process, he adds, involved investing millions of dollars and "having faith that it works. If you saw what was coming in [residential trash] and then what was going out [a highly marketable product], you would need some faith."
But Goldstein says encouraging bright people leads to faith that is well placed. "When you look at our business—or any successful business—the most important thing we have is the people," he states. "They’re not listed on the balance sheet assets, but in a sense they are. We’ve been part of putting up plants in places as wide-ranging as the Czech Republic and Australia, and it is AMG’s people who are responsible. That’s where it begins and ends."
In AMG’s case, Goldstein is particularly receptive to individuals who "can think outside of the box—who could become ‘intrepreneurs.’ If I can find a good person with a bright idea, we’ll enter a new market and I’ll let that person run with that idea," he states.
A LOUDER VOLUME. While niche markets have helped AMG Resources stake out a substantial role in the scrap industry, Goldstein and other company leaders have also witnessed the rapid consolidation that has taken place.
Thus, AMG has set about the seemingly contrary task of being both a niche player and a large enough player to survive in a consolidating industry. Goldstein says he does not see these two goals as being at odds with each other.
"There are different ways of growing in this business, although I’ll say the method of just buying companies just for the sake of growing did not work," he comments. "What will work, I’d say, is trying to reduce your costs by concentrating on specific geographic regions. Or, you can grow along product lines or niche areas in which you can become dominant, which is what we have chosen to do."
LEADING BY EXAMPLE |
Allan M. Goldstein, chairman of AMG Resources Corp., Pittsburgh, is very clear on how influential his father has been in shaping his life. "In the hierarchy of my life, there is God and there is my father," he states. "He was a fantastic person." His father, Sidney Goldstein, "raised us without graduating from high, half-blind with cataracts," Allan recalls. "He drove his scrap collecting truck until the mid-1970s, and finally had a driver after that." Sidney Goldstein would collect scrap from machine shops and other smaller generators in New Jersey. "He could hold 32 barrels on that truck," Allan recalls. "His total volume per month was around 70 tons." In addition to learning about scrap metal from his father by riding along with him in the truck, Allan also received words of wisdom from his father regarding business ownership. "He had several rules, including: Don’t own equipment, because it breaks down; don’t own land, because you can’t sell it in tough times; and don’t have any employees, because they only cause problems," Allan comments. Ironically, Allan realizes, he is now in the position of having broken all three rules. "Some days I feel God is punishing me for breaking those rules," he admits. He is hopeful, though, that his father would understand, and that he would be extremely proud that his son is now earning a living and building on the knowledge of scrap metals he learned by riding along in the truck. Sponsored Content Labor that WorksWith 25 years of experience, Leadpoint delivers cost-effective workforce solutions tailored to your needs. We handle the recruiting, hiring, training, and onboarding to deliver stable, productive, and safety-focused teams. Our commitment to safety and quality ensures peace of mind with a reliable workforce that helps you achieve your goals. Sponsored Content Labor that WorksWith 25 years of experience, Leadpoint delivers cost-effective workforce solutions tailored to your needs. We handle the recruiting, hiring, training, and onboarding to deliver stable, productive, and safety-focused teams. Our commitment to safety and quality ensures peace of mind with a reliable workforce that helps you achieve your goals. Sponsored Content Labor that WorksWith 25 years of experience, Leadpoint delivers cost-effective workforce solutions tailored to your needs. We handle the recruiting, hiring, training, and onboarding to deliver stable, productive, and safety-focused teams. Our commitment to safety and quality ensures peace of mind with a reliable workforce that helps you achieve your goals. |
The company’s presence on both sides of the Atlantic Ocean has helped it pursue opportunities in two often different recycling markets (in terms of both pricing and standard practices) as well as giving the company the ability to serve multi-national scrap generators. "A lot of the generators we buy from are international," says Goldstein. "We can service them from both sides of the Atlantic, which is useful for them."
Turnkey scrap management for industrial scrap generators is another key area for AMG. The company designs and installs specialized equipment to reduce handling and to place the scrap in a more marketable form to appeal to the most logical consumers, according to Goldstein.
While the de-tinning and other specialized facilities cause AMG to focus narrowly on specific generators, by not being as restricted geographically the company is able to keep those customers serviced. "If manufacturing capacity is migrating from one area to another, we’re able to follow our customers," notes Goldstein.
The international presence, in turn, has enabled AMG Resources to begin acting on larger opportunities.
AMG has mill services operations are in place at the Bethlehem Steel Sparrow’s Point integrated mill complex in Baltimore. Similarly, AMG is the sole scrap supplier to a Ford Motor Co. foundry in Leamington, U.K., one of the largest iron and steel foundries in Europe.
Goldstein says the company chooses not to disclose all of its joint ventures, but these ventures—in combination with additional acquisitions—continue to change the face of AMG Resources.
FUTURE PLANS. The ‘first cousin’ opportunities continue to make themselves available. In the U.K., AMG has distinguished itself as a recycler of bi-metal cans, which are still used extensively in Europe.
With bi-metal cans having increased AMG’s presence in the aluminum recycling industry, the company also ventured further into aluminum with its purchase of Shardal Castings Ltd. in Birmingham, U.K. That subsidiary is one of the largest aluminum scrap processing and brokerage companies in the U.K.
"We’re always looking at acquisition opportunities, whether it is ferrous or nonferrous, as long as it fits our profile," says Goldstein. "Right now, aluminum fits our profile, and that could be on the scrap processing side or on the smelting side, but it has to have a relevance to our other operations."
Just 15 years after the company’s start, Goldstein is amazed at the amount of change he has managed in that short time. "I envisioned that we would grow, but certainly could not have seen how things would take shape," he notes. "If you go back after our first five years, the company looked totally different than at the start. And then the company has looked totally different again after each five-year cycle."
Goldstein believes it is likely that over the next five years, more changes are in store. "We always keep an open mind when looking for opportunities," he states. "If you’re too structured in terms of what you’ll do, you won’t exist. The only constant in this business is change."
The author is editor of Recycling Today and can be contacted via e-mail at btaylor@RecyclingToday.com.
Get curated news on YOUR industry.
Enter your email to receive our newsletters.
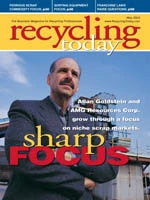
Explore the May 2003 Issue
Check out more from this issue and find your next story to read.
Latest from Recycling Today
- LumiCup offers single-use plastic alternative
- European project yields recycled-content ABS
- ICM to host colocated events in Shanghai
- Astera runs into NIMBY concerns in Colorado
- ReMA opposes European efforts seeking export restrictions for recyclables
- Fresh Perspective: Raj Bagaria
- Saica announces plans for second US site
- Update: Novelis produces first aluminum coil made fully from recycled end-of-life automotive scrap