As one of the country’s premier retailers, Brookstone Inc. of Merrimack, N.H., sets an amazing pace in distributing thousands of products. Remarkably, all of this happens through a single distribution center (DC). There, empty boxes flowing from order fulfillment lines never slow down operations. Thanks to intelligent planning and the right baling operation, this center sets a standard of efficiency that keeps Brookstone on a fast track.
Brookstone’s consumer product line includes home and office furniture, health and fitness equipment and apparel, travel and automotive convenience items, as well as Brookstone’s traditional hard-to-find tools. The company sells through 309 retail stores located across the country. Substantial sales are also generated from its direct-marketed catalogs and from an extensive e-commerce operation (www.Brookstone.com).
Without divulging specifics, Brookstone management describes an annual transaction volume in the hundreds of thousands. Since startup in 1965, all orders have been distributed through a single DC located in Mexico, Mo. Recently, that center underwent a remarkable transformation.
EXPANSION MODE. In 2004, Brookstone’s existing 180,000-square-foot facility was expanded to 400,000 square feet. Thanks to a highly efficient highway of conveyers and pick modules, workers can now quickly unpack and stock thousands of daily incoming shipments.
At the same time, Brookstone employees pick and repack hundreds of thousands of outbound shipments to the company’s retail stores and to individual catalog and e-commerce customers. The result is a streamlined process that generates an enormous volume of empty boxes—up to 400 tons of corrugated scrap annually.
Before the expansion, Brookstone used a single 40-hp baler to bale all corrugated scrap. Empty boxes typically needed to be pre-shredded or crushed before going to the baler. Once shaped, the loose bale had to be pulled out and tied by hand. The entire baling process was handled by a single, full-time operator.
Brookstone’s management team knew that this baling system could never handle the increased corrugated scrap of the expansion to come. It began planning for the baling upgrade, not just with one new baler, but with two new 40-hp balers that would each be directly fed by an overhead conveyer system.
Don Magnus, Brookstone’s DC facilities manager for the past six years, was put in charge of the baler evaluation and selection process.
Don Wheeler, a 25-year veteran of the recycling industry and dealer for American Baler, Bellevue, Ohio, proposed a unique alternate. After reviewing Brookstone’s packing and repacking processes and "conveyorized" flow of empty boxes, Wheeler recommended the company install three 30-hp, wide-mouth, auto-tie balers. In doing so, each of the two regular conveyer lines would feed directly into its own baler, while a separate conveyer line for oversized boxes would feed the third baler.
This new plan resolved Magnus’ concern of what to do with the stream of oversized boxes. Wide-mouth balers, with feed openings of 43-by-50 inches wide, proved to be the perfect solution for all box sizes. As an added bonus, pre-shredding and crushing would no longer be necessary. "There is no prep needed. Just throw the box on the line, and it gets baled. It really is that simple," Mangus says.
CONSIDERING AUTOMATION. To further automate the baling operation, Brookstone specified a touch-screen operator interface on all three balers. The touch-screen control is designed to simplify operator settings through color prompts and diagrams. The panel even provides visual diagnostics to help troubleshoot safety or mechanical faults.
Each baler was also specified with an automated wire tie system. As bales are pushed through the baler’s extrusion chamber, five wires are wrapped around the length of the bale. The tier automatically ties and cuts each wire when the bale reaches the operator-specified length. Magnus particularly likes the swing-away design of the American Baler auto tier that allows easy access to all tier components.
Style Matters |
Below is a set of parameters for each baler type describing how the unit works and detailing optimal markets: • Vertical Baler – The cylinder and platen move vertically to compress material into a bale that is tied manually. This baler is very labor intensive. • Closed Door Baler – The horizontal movement of the main cylinder compresses material against a wall or door. Some labor is involved in tying off the finished bale. It can be fed manually or by conveyor or air and is used in low-production facilities. • Open-End Baler – Horizontal movement of the main cylinder with a second cylinder providing resistance results in the compression of material. With open-end balers, customers are not tied to a fixed bale length, so the separation of grades is easier. Production capabilities range from very low to extremely high. • Two-Ram Baler – Typically used for non-fiber products where additional wires are needed to hold compressed material together. Two-ram balers are also used to compress municipal solid waste. The smaller versions are ideal for recyclers that process a multitude of grades, but whose volume is low. – Roger Williams, American Baler Co. sales manager |
By producing highly compacted bales, Brookstone will save thousands of dollars throughout the life of the balers because they are using less wire per baled ton.
Brookstone’s management was also pleased to discover that minimal labor was required to run the newly automated baling operation. "We now have three balers instead of one," Magnus explains, "but the new ones are so easy to operate and so reliable, we still only need one person to run them."
The new wide-mouth balers are designed to produce bales measuring 42-inches wide and 42-inches high. Bale length, however, can be easily programmed to create custom-sized bales. With a variable bale length, Brookstone would now be able to optimize truckload shipments to the recycling center.
Brookstone sells its bales of corrugated boxes to Batliner Paper Co. in Kansas City, Mo., one of the largest scrap paper brokerage and processing centers in the Midwest. Before the new balers were installed, Brookstone was having difficulty achieving the maximum shipping weight of 40,000 pounds. As a result, Brookstone was being assessed a surcharge by the recycler for each trailer that didn’t make this weight.
To help resolve the issue, the manufacturer programmed the PLCs for the balers to ensure that the bales would maintain a set 1,800 pound bale weight. Since the newly programmed PLCs were installed by Brookstone, spot checks have shown that optimum trailer weight is being met on a routine basis. Magnus also noted that the bales fit better and stack more neatly in the trucks.
"Brookstone’s DC operations have never run smoother," Magnus proudly states. Two multi-level pick modules, the oversized product line,and a returns line are run two shifts per day, seven days a week. All three wide-mouth balers are operating at the same time—16 hours per day, 365 days each year.
According to Magnus, the decision to buy balers based on dependability, ease of operation and maintenance, and manufacturer support, has really paid off. "Under the heavy work load at this center, the wide-mouth American Baler models have met the challenge and have exceeded our expectations in all areas. They really help us set the pace."
This article was submitted on behalf of American Baler Co., Bellevue, Ohio.
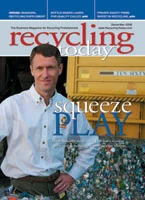
Explore the December 2006 Issue
Check out more from this issue and find your next story to read.
Latest from Recycling Today
- NWRA announces 2025 Driver of the Year, Operator of the Year winners
- The Scrap Show: Nanci Schuld of FE Trading Group LLC
- Call2Recycle Canada partners with RLG to advance battery collection
- Report delves into recovery opportunities for food-grade polypropylene
- Reimagining Supplier Payments in Metal Recycling: A Digital Leap Forward
- STEINERT Lithium Battery Detection and Removal from Waste Streams
- Driving the Future: Innovations in Waste & Recycling Technology
- Robin Wiener recognized for recycling leadership