
Image courtesy of Huhtamaki

The packaging industry has evolved rapidly as consumer spending habits, as well as sustainability concerns, have changed, and one of the industry’s leading initiatives has been developing mono-material flexible packaging over more traditional multilayer options.
In a study released last year, Chicago-based research firm PreScouter says mono-material has become a buzzword in the packaging industry, particularly as it pertains to flexible packaging. Obviously, the use of fewer materials in packaging products is ideal for mechanical recyclers because of the difficulty of separating the different film layers in multimaterial packaging, and Akron, Ohio-based data analysis firm Smithers adds that many countries often don’t have the necessary recycling systems in place to recycle complex laminates.
However, mono-material packaging, while preferred by recyclers, poses its own challenges for brand owners that must provide a level of structural integrity and compliance to meet the needs of their customers.
According to the PreScouter report, research and development teams are focusing on eight key challenges in developing mono-material packaging:
- heat-sealability;
- adhesion;
- printability;
- achieving high transparency;
- surface enhancement;
- food-contact compliance;
- increasing stiffness; and
- reduction of used material, not reducing productivity.
“Multimaterial packaging was seen as a necessary compromise to ensure other key functionalities of the package, such as providing protection, making the packaging sealable, making it possible to print information on the package and other key functionalities,” says Katri Saarenheimo, head of communications and sustainability, flexible packaging, at Finland-based global packaging producer Huhtamaki.
In late April, Huhtamaki launched what it says is a “groundbreaking” mono-material technology—Blueloop—that meets the demands of its customers and consumers. Blueloop packaging has three options: paper, polyethylene (PE) and polypropylene (PP) retort. Its PE option contains up to 95 percent PE, while the PP and paper applications have at least a 90 percent mono-material share.
Marco Hilty, president of flexible packaging at Huhtamaki, said at the time of the launch, “What we’ve done, quite simply, is redesign the future of flexible packaging by setting new industry standards in mono-material solutions.”
Sustainable innovation

When it came time to develop its mono-material packaging, Saarenheimo says Huhtamaki dedicated years of work to the initiative as its in-house packaging experts worked with machinery and material suppliers.
She describes Huhtamaki’s testing and validation process as internally and externally “rigorous.”
“We conduct testing on all new material structures systematically, including barrier properties, durability, performance on production machinery and many others,” Saarenheimo says.
In the food packaging industry and other sectors with contact-sensitive, safety-critical applications, Huhtamaki conducts its testing in collaboration with customers to ensure the products fulfill their various requirements. The company also works with third parties to test packaging performance with current recycling technology and to certify recyclability.
“Further testing and development always continue when working with customers for specific applications to make sure switching from one solution to a new one goes as smoothly as possible,” she says.
Huhtamaki’s goal in developing its latest Blueloop solutions was to achieve the highest percentage of mono-material while not compromising protection and keeping the product affordable. Saarenheimo describes Blueloop’s combination of protection, full recyclability and affordability globally as “game-changing.”
“We believe the choice of packaging must always be guided with the principle of best fit for purpose,” she adds. “We find the optimal balance between minimizing the impact on the environment while protecting what’s inside the package.
“We are able to provide all [those] benefits … with the highest share of mono- material content, meaning we significantly improve the performance of the packaging in today’s recycling processes.”
Saarenheimo says “affordable sustainability” is important to Huhtamaki, adding that it was possible to achieve global affordability with a less-is-more approach. “Simplified, high-performance mono-material structures make this a resource-efficient alternative,” she adds, noting that Blueloop packaging was designed to be produced globally at scale using existing machinery.
“While we are dependent on packaging in our way of living, we must do everything we can to find solutions that make it more sustainable and increase circularity.” – Katri Saarenheimo, head of communications and sustainability, flexible packaging, Huhtamaki
The recycling piece
Saarenheimo says Huhtamaki’s mono-material packaging is designed for recycling, with the goal of easing the recycling process by using the highest possible percentage of mono- material to drive a higher yield and increase quality and value of postconsumer recycled (PCR) material.
“Our target is to support increased efficiency and ramp-up of recycling streams,” she says. “Today, the efficiency of recycling streams varies between countries, and the recycling of plastics is a challenge still to be solved in many regions. … We are eager to find ways locally to develop awareness of recycling streams and to better inform customers how the package should be recycled; [but], here, we need to take into account regional differences in recycling practices.”
Huhtamaki’s mono-material packaging does not contain PCR or postindustrial recycled (PIR) content as Saarenheimo says current regulations for contact-sensitive applications such as food and pharmaceutical packaging “do not make it possible to use mechanically recycled content.” The use of PCR or PIR requires close collaboration with customers as well as with recyclers to ensure quality and availability, she adds, but the company is seeking ways to reuse any production scrap to support Huhtamaki’s and its customers’ sustainability commitments.
Saarenheimo says Huhtamaki is eager to find ways locally to develop awareness about recycling streams and to better inform consumers how packaging should be recycled. “We strongly believe in doing our share by feeding the streams with material that performs with existing recycling technology [and] sharing information about correct disposal,” she adds.
The future of mono-material

Mono-material packaging is a very important trend in flexible packaging, Saarenheimo says, noting a “strong shift” from those in the packaging industry and brands to provide only recyclable, reusable or compostable packaging and to address the circularity challenge of packaging by minimizing the use of unnecessary resources.
Sponsored Content
Labor that Works
With 25 years of experience, Leadpoint delivers cost-effective workforce solutions tailored to your needs. We handle the recruiting, hiring, training, and onboarding to deliver stable, productive, and safety-focused teams. Our commitment to safety and quality ensures peace of mind with a reliable workforce that helps you achieve your goals.
Sponsored Content
Labor that Works
With 25 years of experience, Leadpoint delivers cost-effective workforce solutions tailored to your needs. We handle the recruiting, hiring, training, and onboarding to deliver stable, productive, and safety-focused teams. Our commitment to safety and quality ensures peace of mind with a reliable workforce that helps you achieve your goals.
Sponsored Content
Labor that Works
With 25 years of experience, Leadpoint delivers cost-effective workforce solutions tailored to your needs. We handle the recruiting, hiring, training, and onboarding to deliver stable, productive, and safety-focused teams. Our commitment to safety and quality ensures peace of mind with a reliable workforce that helps you achieve your goals.
Sponsored Content
Labor that Works
With 25 years of experience, Leadpoint delivers cost-effective workforce solutions tailored to your needs. We handle the recruiting, hiring, training, and onboarding to deliver stable, productive, and safety-focused teams. Our commitment to safety and quality ensures peace of mind with a reliable workforce that helps you achieve your goals.
Sponsored Content
Labor that Works
With 25 years of experience, Leadpoint delivers cost-effective workforce solutions tailored to your needs. We handle the recruiting, hiring, training, and onboarding to deliver stable, productive, and safety-focused teams. Our commitment to safety and quality ensures peace of mind with a reliable workforce that helps you achieve your goals.
“At the same time, we must acknowledge globalization has made societies dependent on packaging,” Saarenheimo adds. “While we are dependent on packaging in our way of living, we must do everything we can to find solutions that make it more sustainable and increase circularity.”
In Europe alone, many companies, including SABIC, Mondi, Borealis and others, have worked to develop mono-material solutions to replace multi-material laminates, vinyl-based materials and composite carton packaging.
“We want to see a global food supply chain using only packaging that truly fits with recycling streams for plastics and paper,” Saarenheimo says. “We need to make circularity a standard part of everyday life by designing and delivering on it.”
Huhtamaki has invested in new production technologies in key sites, Saarenheimo says, to continue to bring mono-material solutions to the global market at scale. She notes the company has several ongoing investments to scale up production volumes, including plastic film-making capabilities and advanced technologies related to the barrier properties of Huhtamaki’s material structures.
Saarenheimo says production capacity will ramp up globally throughout this year and Huhtamaki’s Blueloop packaging is available via export to the U.S.
“The reason that sustainability and innovation go together is that we want to drive a systemic change from using renewable or recycled content to securing products’ end-of-life recycling,” Saarenheimo says. “Innovation for us means both in-house innovations as well as partnering and [collaborating] with our customers, suppliers, startups and others across the value chain.”
Get curated news on YOUR industry.
Enter your email to receive our newsletters.
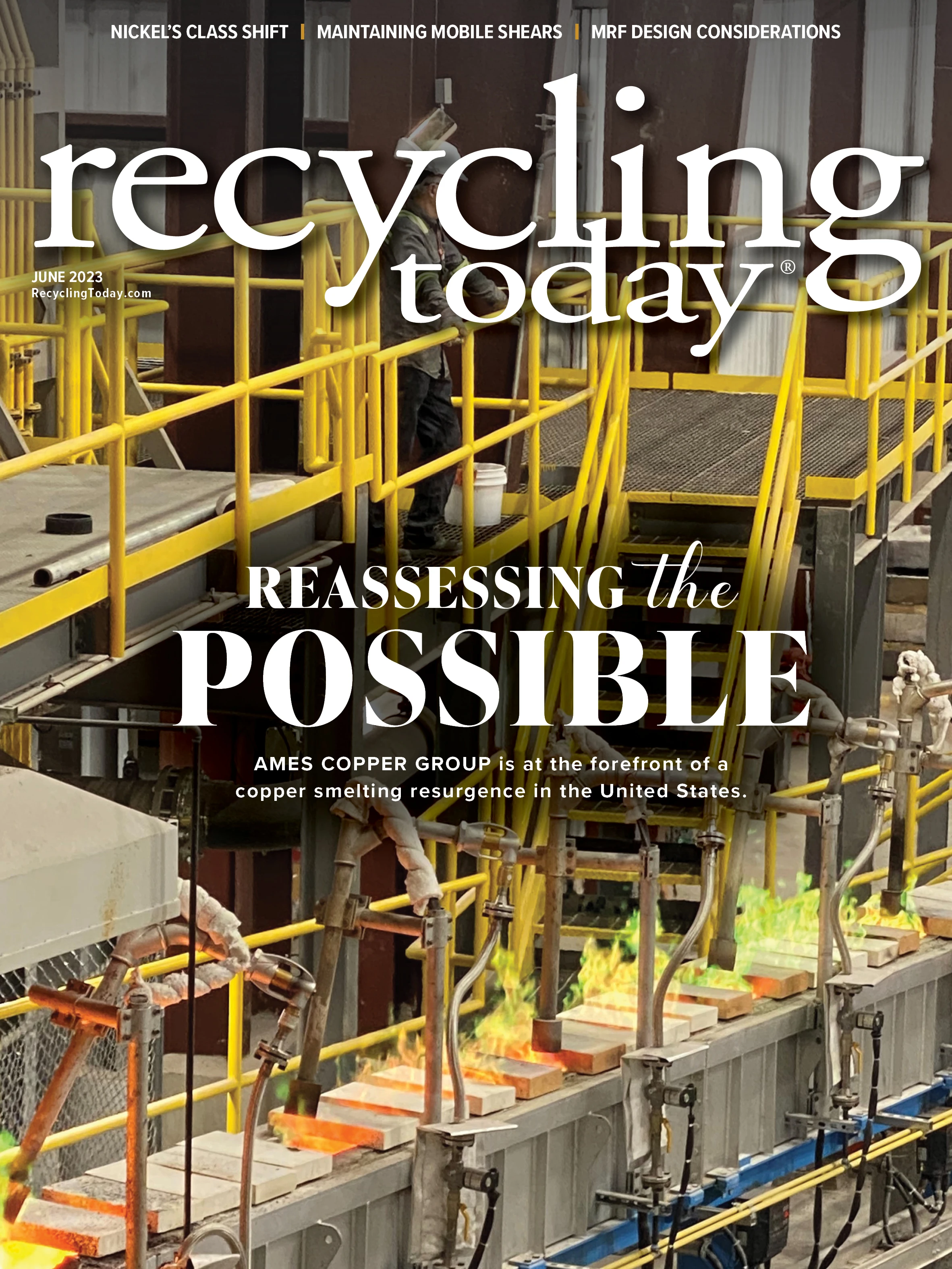
Explore the June 2023 Issue
Check out more from this issue and find your next story to read.
Latest from Recycling Today
- Athens Services terminates contract with San Marino, California
- Partners develop specialty response vehicles for LIB fires
- Sonoco cites OCC shortage for price hike in Europe
- British Steel mill’s future up in the air
- Tomra applies GAINnext AI technology to upgrade wrought aluminum scrap
- Redwood Materials partners with Isuzu Commercial Truck
- The push for more supply
- ReMA PSI Chapter adds 7 members