Recycling would probably seem downright easy if processors were presented with shipments and waste streams that were segregated by material.
Scrap processors who accept material only from industrial accounts try to minimize their need to sort and separate. But for those who take in obsolete scrap ranging from auto hulks to lawn furniture, the very word “processing” is almost synonymous with sorting and separating.
Municipal recyclers for years accepted materials separated in advance by residents, and then attempted to keep those streams separate for the sake of minimizing the work required between collection and shipment to consumers. But the need to cut collection costs and encourage greater participation from residents has triggered a shift toward commingled collection. With the commingled approach, volume goes up, but so does the amount of sorting and separating work required.
So now scrap processors, MRF operators and paper packers alike are paying close attention to any technological improvements offering an easier way to analyze, separate and sort the material flowing into their facilities.
Whether they are separating contaminants from marketable commodities or wringing out several commodities from one stream, processors are always seeking better ways to sort and separate. Fortunately for the processors, manufacturers in different parts of the world are allocating research dollars to upgrade existing sorting techniques and to develop new ones.
Today, recyclers have the ability to study systems that use air, water, gravity, density, optical scanning, magnets, vibrating conveyor systems and any other means conceivable of separating materials from one another. The willingness of recyclers to try new technology has encouraged entrepreneurs to introduce new systems for virtually any recyclable stream, from mixed C&D debris to auto shred, and from municipal solid waste to recyclable containers collected at the curb.
There may always be a need for sharp-eyed metals identification experts and trained conveyor line sorters. But as the century draws to a close, the equipment being made available to recyclers is allowing many of them to offer a mechanically-aided product quality guarantee to their suppliers that can only enhance the reputation of recycled commodities.
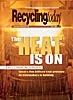
Explore the July 2001 Issue
Check out more from this issue and find your next story to read.
Latest from Recycling Today
- LumiCup offers single-use plastic alternative
- European project yields recycled-content ABS
- ICM to host colocated events in Shanghai
- Astera runs into NIMBY concerns in Colorado
- ReMA opposes European efforts seeking export restrictions for recyclables
- Fresh Perspective: Raj Bagaria
- Saica announces plans for second US site
- Update: Novelis produces first aluminum coil made fully from recycled end-of-life automotive scrap