Boiler system for multilayer plastics separation. A patent awarded to RepetCo Innovations S.L., based in Madrid, describes a system and method for separating multilayered plastics commonly used in agriculture, industry and packaging.
Current methods of recycling multilayer plastics include steps such as size reduction, weakening the adhesive bond between layers and separating the layers physically and/or chemically. Drawbacks associated with these methods include their high energy requirements and the use of toxic chemicals and abrasive substances.
The patent describes a system with a boiler that introduces superheated steam vapor to a holding vessel containing multilayer plastic fragments. The incoming steam heats the vessel to a temperature between 212 F and 377 F, raising its interior pressure to between 1 and 12 bar for 10 to 60 seconds. The fragments then are carried to a discharge tank at a relative pressure between −0.7 and 0.1 bar and at a temperature between 59 F and 77 F for up to 5 minutes.
The superheated vapor causes heat shock that does not require heating the entire particle to a specified temperature, followed by the mechanical shock from the sudden pressure change to the plastic layers when the fragments are moved to the discharge tank. Together, these forces weaken and break the chemical bonds between the layers.

The multilayer fragments are later transferred to a mechanical separation unit where they are separated into fragments of single-layer plastic. Finally, the fragments progress to a mechanical sorting unit where they are sorted by material.
Time, temperature and pressure of the pressurization and vacuum cycles can be customized to the materials used in multilayer plastics—for example, polyethylene terephthalate (PET) and polyethylene (PE). However, the method is suitable for separating layers of any other plastic materials. The pressurization and vacuum cycles also can be repeated one or several times depending on the types of plastic and other properties of the multilayer plastic fragments, returning the multilayer plastic fragments through valves and other control means from the discharge tank to the vessel.
The temperature and pressure conditions inside the vessel and the discharge tank remain constant by means of the boiler, valves, pumps or other controls. This prevents energy losses and increases productivity. Steam that enters the discharge tank is extracted through a recovery valve, condensed and filtered, then the recovered water is reintroduced into the boiler. Because only vapor is heated rather than the entire mass of plastic fragments, energy is saved and no chemical products are required.
Patent 11858174; published Jan. 2, 2024.
Improved clarity in PET reclamation. Alpla Werke Alwin Lehner GmbH & Co. KG, of Austria, received a patent for a method of reclaiming thermoplastic materials for recycling that overcomes a common problem: PET becoming more yellow, cloudy or gray in appearance over progressive cycles of recycling.
Prepared thermoplastic flakes are exposed to an oxidative fluid and heat, which can range from 320 F to 464 F, for a range of 5 minutes to 10 hours.
Contaminants and agglomerates formed during the process can be taken up by the oxidative fluid and separated from the reaction space. Further separation of solid contaminants can be performed by sifting technologies, and standard sorting systems can be used to remove discolored solid contaminants or contaminants made brittle by the heat and oxidation treatment.
The patent says the process works well when used after steps such as washing flakes in alkaline solutions or cold-sorting to separate contaminants such as metal or other plastics. Agglomerates, adhesives, paints and varnishing or flakes that are stuck or crumbled because of exposure to the oxidative fluid are separated by sifting. The patent claims to enable the polymer chain length to be increased to the level of the original raw material.
The method works with thermoplastic materials including PET, polypropylene, polylactide, polyethylene furanoate, polypropylene furanoate and high-density PE.Patent 11794378; published Oct. 24, 2023.
Get curated news on YOUR industry.
Enter your email to receive our newsletters.
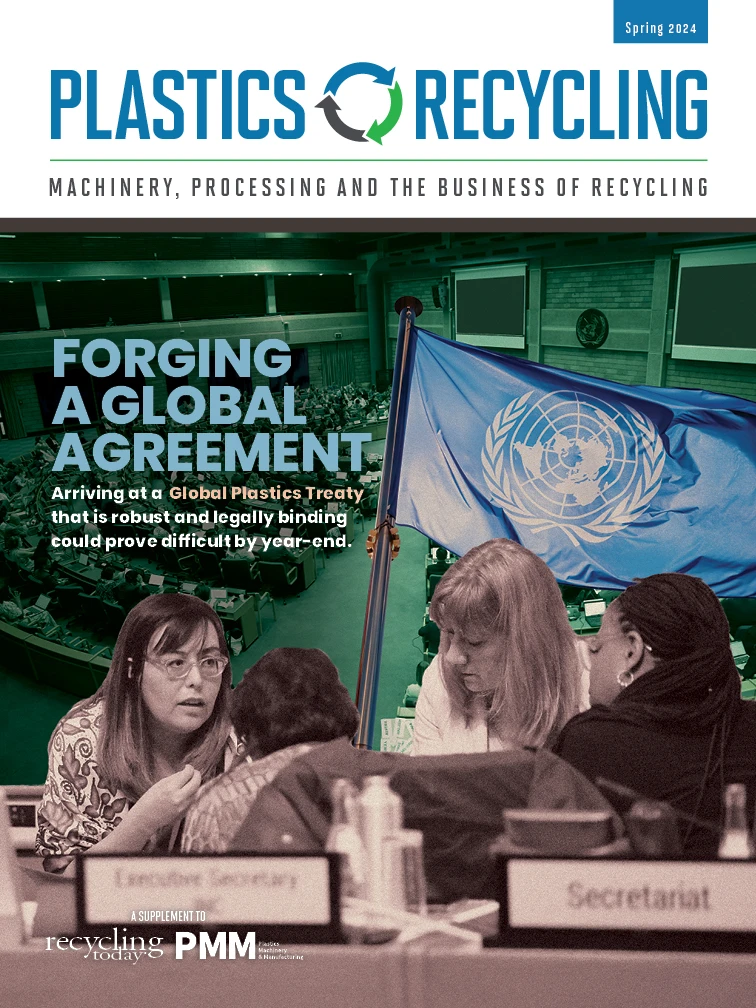
Explore the Spring 2024 Plastics Recycling Issue
Check out more from this issue and find your next story to read.
Latest from Recycling Today
- CP Group announces new senior vice president
- APR publishes Design Guide in French
- AmSty recorded first sales of PolyRenew Styrene in 2024
- PRE says EU’s plastic recycling industry at a breaking point
- Call2Recycle Canada, Staples Professional expand partnership
- Circular Services breaks ground on north Texas MRF
- Tariff uncertainty results in choppy nonferrous scrap flows
- CATL, Ellen MacArthur Foundation establish battery partnership