These were separated from ASR by trommeling the ASR in a trommel equipped with a ¼ inch (6mm) screen. The fines constitute between 40% and 55% of the ASR weight but only a small percent of the ASR volume. In some samples, especially those containing less than 10% moisture by weight, over 50% of the fines were smaller than 1/16 inch, or about 1.5 mm. Wet ASR does not separate as well as the dry ASR does, and fines in wet ASR have a tendency to agglomerate.
We considered using the fines as a source of iron oxide for the cement industry. We also considered using the fines for producing reduced iron. Therefore, we conducted chemical analysis of the fines to establish their composition and to determine whatever upgrading of the fines is necessary so that they can meet the specifications for raw materials for these industries.
Both industries prefer maximizing the iron content and reducing the levels of contaminants. Therefore, upgrading the fines for such applications by further separation to increase the iron content and to reduce the concentration of undesirable materials was necessary. The cement industry is also concerned about the presence of hardened steel pieces which may damage the crushers, and which may not distribute themselves evenly in the mix. Excluding any particles larger than 6 mm from the fines minimizes the chances of having such hardened pieces in the fines.
Chemical Composition
Elemental analysis of several samples of the total fines was conducted using the inductively coupled plasma (ICP) technique. The procedure involved igniting the sample at 750oC and then analyzing the residual material using the ICP technique. Using the elemental analysis data, we calculated the oxides content of the fines. As expected these fines are rich in iron and silicon.
The iron source is primarily the rust off the cars and some finely shredded steel. The silicon is from glass, sand and mud on the cars and from the property where the material was shredded and stored. Both iron units and sand are used as raw materials in the cement making process.
The fines also contain elevated levels of alkali metals (sodium and potassium) and zinc. The cement industry likes to maximize the concentration of the iron units and lower the concentration of the alkali metals and zinc because these affect the quality and the curing time of some types of cement.
If the fines are to be used to produce reduced iron pellets, that industry also likes to maximize the iron concentration and reduce the concentration of everything else, especially zinc because the zinc will increase the production of electric arc furnace (EAF) dust that is a hazardous waste.
Another concern is the lead content of the fines, which is about 0.25%. Normally, batteries are removed before shredding the cars. However, there are other parts in cars containing lead, such as lead weights as part of the seat belt locking mechanism in some vehicles. Some of these parts may not be readily identifiable by dismantlers. Michael Day, from the Canadian Research Council, suggested that some of the lead in the ASR is from the dirt picked up from the roads. He suggested this dirt is contaminated with lead from the exhaust of cars when cars used to burn leaded gasoline that contained tetra ethyl lead.
The data, along with the requirements of the two industries, therefore determined further purification of the fines is necessary before the fines can be used as raw materials.
To upgrade the fines, we magnetically separated them into two fractions: magnetic and non-magnetic. The magnetic fraction is obviously the product.
Post-Magnetic Composition
About 50% of the fines’ weight could be separated as a “magnetic fraction” using magnets. Elemental analysis of the magnetic fraction was conducted using the ICP technique.
Typical results achieved with proper separation show the concentration of the iron units has increased significantly while the concentration of essentially everything else has decreased upon magnetic separation, including the concentration of the alkali metals and the zinc.
Of particular interest is also the significant drop in the concentration of combustible materials. This is important in controlling the generation of pollutants. For example, the cement industry introduces the iron units in the kiln at high temperatures that may not be high enough to allow complete combustion of the organics. Therefore, the presence of organics will result in elevated pollution levels.
Our discussions with the industry suggest the organics concentration should be kept below 5%, and this is achievable by efficient magnetic separation. Lower concentrations can also be achieved by sink/float techniques. Separation of the residual PVC requires higher densities, and therefore a heavier media will be required. Therefore, washing and maybe some drying of the fines after separation will be required. Obviously, this will increase the operating cost.
A Harvest Waiting
Fines are a rich source of iron and iron oxide. They also constitute about 50% of the ASR weight, and thus about 50% of the fines can be magnetically separated into an iron-rich stream.
Therefore, they should be seriously considered for recycling as a source of raw materials. Careful analysis of the fines at each shredding facility should be conducted to determine further purification requirements of the fines to meet the specifications of the end user.
The author is a principal investigator with the U.S. Department of Energy’s Argonne National Laboratories and wrote the paper on behalf of the Salyp ELV Center in Leper, Belgium.
A more detailed version of the report can be made available by contacting the Salyp ELV Center via e-mail at info@salyp.com, by visiting the Salyp Web site at www.salyp.com, or by calling 00 32(0)57 22-80-44.
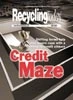
Explore the May 2001 Issue
Check out more from this issue and find your next story to read.
Latest from Recycling Today
- Magnomer joins Canada Plastics Pact
- Electra names new CFO
- WM of Pennsylvania awarded RNG vehicle funding
- Nucor receives West Virginia funding assist
- Ferrous market ends 2024 in familiar rut
- Aqua Metals secures $1.5M loan, reports operational strides
- AF&PA urges veto of NY bill
- Aluminum Association includes recycling among 2025 policy priorities