There are many different ways to recycle used tires. The key to success, however, is to produce the desired end product in the most cost-efficient manner. More often than not, the method for producing the specific size of the end product is carefully researched, while the process used to separate the tire materials is just given a cursory investigation. A substandard separation system can result in either a product that is too contaminated with fiber and steel or a system that is too costly to operate (or cost prohibitive for the customer to cover the expense of a redesign.)
In other words, careful research in the planning stage of the whole separation process is very important.
SEVERAL STAGES
Separating a tire into crumb rubber, fiber and steel with an ambient processing method usually begins after the tire has been shredded, and hopefully de-beaded. It is at this point that the tire has been reduced small enough to begin separating the various components.
There are several methods for reducing the tire chip. Three of the major processes used are:
• Mills that “pull” the fiber and steel out of the rubber.
• Reduction mills that grind all three: rubber, steel and fiber
• Reduction mills that reduce the rubber while liberating or separating the steel and fiber from the crumb rubber.
The Gabriel G2400 reduction mill is one that is designed to slice and chop the tire, passing the steel belt through the mill virtually intact. Some of the fiber will become fluffed, putting it in a state that tends to be easier to separate from the crumb rubber, especially when using gravity separators.
The steel belt wire is usually removed with a magnet or series of magnets, depending on the purity of the crumb rubber desired. A cross-belt magnet in conjunction with a vibratory feeder belt will typically pull out 80% to 90% of the steel belt if the crumb rubber has been reduced to 10 mesh or smaller.
A drum magnet can sometimes be more efficient and will run in the 90% to 95% range. The more times the crumb rubber is exposed to the magnets, the higher the purity. Again, the key is to carefully match the separation process with the degree of purity desired.
Separating the fiber from the crumb rubber is a little more difficult. Typically, the larger the fiber is by size, the easier it is to separate. Since the fiber cannot be removed by magnets, it must be separated by utilizing a size or weight differential.If the processing equipment fluffs or enlarges part of the fiber, a scalping screen can easily remove it. Since the crumb rubber is considerably smaller, you may remove as much as 50% of the fiber simply by screening. But from here on, it becomes increasingly difficult. A typical method to remove the remaining fiber is by using a vacuum gravity separator.
The vacuum gravity separator removes the fibers based on the density or weight differential between the crumb rubber and the fiber. This process has to be set up very carefully to remove as much fiber as possible, while still retaining most of the crumb rubber.
This often becomes a trade-off between how fiber-free the crumb rubber must be and how much crumb rubber has been lost because it becomes mixed in with the fiber. Once separated, the fiber usually has enough contaminants in it that it does not have much resale value.
END PRODUCT POSSIBILITIES
Another consideration is to determine the best way to conveniently and efficiently collect, transport and dispose of the separated products. Steel belt wire is a low-grade steel that has a value, if it is relatively free from contamination.
Examples of the most common reduction methods are:
• The type that pulls a significant amount of rubber and fiber with the steel, making it too full of contaminants for resale.
• The type that liberates the steel belt and minimizes its reduction, which is probably the most cost-efficient.
•The type that grinds the steel belt, or bead for that matter, which could waste a lot of energy and add unnecessary wear and tear to the reduction equipment.
Usually, the quicker the steel belt is liberated and separated from the rubber, the more efficient and cost effective the operation. After the magnets separate the steel belt, it can be easily conveyed into a container for disposal or resale.
The most important thing to remember, when setting up a processing system, is to match it to your needs. 99% wire and fiber-free crumb rubber made from whole tires is considerably more costly to produce than 90% or even 95% wire and fiber-free crumb rubber.
Designing the separation process along with the reduction process provides you with a tremendous advantage. Fortunately, there are proven systems that can produce crumb rubber cost-effectively at almost any production level—ranging from 2,000 pounds per hour up to 20,000 pounds per hour. Taking the time to investigate all the possibilities and to utilize all the knowledge and resources available in the industry today can result in a highly successful operation.
Reduction mills are providing recycled rubber and other materials for a variety of customers throughout the world.
The author is president of Gabriel International Group, Lawrenceburg, Ind., a designer and manufacturer of reduction mills and processing systems for rubber and other materials.
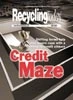
Explore the May 2001 Issue
Check out more from this issue and find your next story to read.
Latest from Recycling Today
- Magnomer joins Canada Plastics Pact
- Electra names new CFO
- WM of Pennsylvania awarded RNG vehicle funding
- Nucor receives West Virginia funding assist
- Ferrous market ends 2024 in familiar rut
- Aqua Metals secures $1.5M loan, reports operational strides
- AF&PA urges veto of NY bill
- Aluminum Association includes recycling among 2025 policy priorities