Municipalities and waste haulers are taking an in-depth look at single stream recycling as a way of streamlining collection and processing to reduce overall operating costs of their recycling programs. While the savings can be considerable, one must not underestimate the importance of a well designed and well managed process within the material recovery facility (MRF).
WORKING IN COORDINATION
If single stream recycling is going to be successful, municipalities must be willing to spend some time and money educating the home owner (and commercial generators) in regards to quality issues. Education will be crucial to the success of the program.
The term single stream has taken on different meanings over the years, so let’s first define the term. Those who have been in the industry for a while may have a tendency to relate the term single stream processing to a mixed waste processing facility (known by some as a “dirty MRF”), which attempts to sort quality recyclables from garbage. Many of these facilities did not get good marks from consumers because of their limited success in putting together clean shipments of recyclables.
The term that relates more accurately to the technology being developed and marketed today for processing is “single stream recycling.” This term would describe a recyclable mixture containing both fibers and containers commingled in the same stream.
There are pros and cons to single stream recycling. However, with the proper set-up and good process management, the pros will easily outweigh the cons.
Some of the benefits to single stream recycling are lower collection costs, higher diversion rates due to easier participation by the homeowner, one tipping floor, and one residue stream to manage.
Some of the skepticism about this process relates to paper mill buyer reluctance, increased residue, additional capital costs and perhaps the attitude that “it didn’t work before so it won’t work now.”
But MRF technology today has improved dramatically due to advanced equipment and layout knowledge. These advancements have reduced labor costs while improving product quality at higher levels of productivity.
The (Electric) Eyes Have It |
Progress is being made in using optical sensors to identify and sort plastic containers at MRFs. By Felix A. Hottenstein While state-of-the-art automated optical sorting systems for plastic containers have been embraced by many plastic processors worldwide, this is not the case yet for material recovery facilities (MRFs) here in the U.S. There is certainly no shortage of empty plastic containers being generated. Due to the increased use of plastics in packaging applications, particularly PET, the actual percentage of plastics recycling has declined. Significant price swings over the past few years have contributed to a reduction in the number of cities collecting recyclable materials. Currently in the U.S., beside basic mechanical separation technology, material sorting at MRFs primarily is a manual task. In contrast, in Europe automation of this process has been implemented more widely. In MRF applications, material properties of plastic-like material are sensed and identified by near-infrared reflection sensors as compared to transmission-type sensors that are mostly used in plastic processing applications (e.g. PET color sorting). There are two main reasons for this: a) most of the objects are opaque and could not be identified with transmission sensors, and b) the sensor module should not touch the material it is sorting, since contaminants and waste are in the stream. MSS Inc., Nashville, Tenn., has introduced the new Sapphire™ sorting module that is capable of identifying and sorting the following items by their specific ‘signatures’ (either one by one, or in any combination) from a mixed stream of solid waste: PET, PE (polyethylene), PP, PS, PVC, beverage cartons, paper, mixed plastics (all plastic-containing materials). The Sapphire separation system uses high-speed microprocessors to determine object shape, position, and resin type. Once an object is identified, the master control computer gives the signals to fire precise compressed air pulses through precision solenoid air valves to eject the selected object, which is ejected upwards into a catcher hood. -- Felix A. Hottenstein. The author is sales director of MSS Inc., Nashville, Tenn. |
Older single stream MRFs required much higher staffing levels to work the sorting lines. Most of these older systems utilized ballistic separators that broke a lot of glass, making the fiber difficult to market.
These separators were also extremely expensive to operate due to excessive down time and high maintenance costs. Newer separating systems such as the Mach One Separator by Machinex Industries Inc., Plessisville, Quebec, Canada, use a much simpler technology that drastically reduces glass breakage while improving flat/round separation. These newer primary separators will also separate #8 news from the fiber stream to further reduce sorting costs.
The implementation of a secondary screen such as the Mach One Finishing Screen has been successful in creating a cleaner container stream by removing a greater percentage of the fiber from the containers while at the same time screening out the fines.
This finishing screen helps reduce residue while providing a cleaner stream to the sorters. Separator screens need to be designed with built in flexibility to allow for changes in product and climatic conditions. Features such as variable angle screen decks, an easily adjustable screening surface with replaceable split discs and variable speed drives play a role in the efficiency of the separator.
Overall system design is another ingredient vital to the success of a single stream recycling process. It is important to understand what materials should be removed at the pre-sort and in what order other materials should be sorted. An equipment layout that uses self dumping bunkers and live floor bunkers can provide operational savings such as reduced vehicle movement on the process floor. This can reduce the need for a larger building size, as well as reducing the size of loaders required in the plant and allowing for a less demanding loader maintenance schedule.
A TYPICAL DESIGN
The modern single stream recycling plant process starts with a pre-sort area where larger contaminants are removed before the automated screening process begins. Cardboard can be removed automatically with an OCC (old corrugated containers) screen or can be picked off manually at the pre-sort area.
In a Machinex system, materials then flow onto the Mach One Separator, where containers are separated from the paper and a primary fiber sort takes place. The primary fiber sort carried out by the Mach One Separator automatically sorts ONP (old newspapers) from the mixed fiber. Two streams of fiber then flow along their respective sort conveyor lines for final sorting and inspection.
Unders from the Mach One Separator are transferred to the finishing separator, where fines are removed and the remaining fibers are returned to the mixed fiber line for sorting. As the commingled containers exit the separator, they are transferred to the container sorting line for a semi-automatic sort. All sorted materials are stored in their respective bunkers waiting their turn to be baled and shipped out to market.
There are a number of communities in North America that are using this technology and have realized great savings in their recycling program costs. The move to single stream recycling is on, and the benefits are attractive!
The author works out of the Toronto office of Machinex Industries Inc., Plessisville, Quebec, Canada.
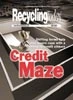
Explore the May 2001 Issue
Check out more from this issue and find your next story to read.
Latest from Recycling Today
- Magnomer joins Canada Plastics Pact
- Electra names new CFO
- WM of Pennsylvania awarded RNG vehicle funding
- Nucor receives West Virginia funding assist
- Ferrous market ends 2024 in familiar rut
- Aqua Metals secures $1.5M loan, reports operational strides
- AF&PA urges veto of NY bill
- Aluminum Association includes recycling among 2025 policy priorities