Today’s most popular applications for vibratory equipment such as finger screens and de-stoner/classifiers are within the municipal solid waste segment, in the post-auto shredding stage, and for construction and demolition (C&D) materials.
For the most part, vibrating equipment is used in dry classification of commingled materials, but it can easily be adapted to handle wet materials. The recovery of both ferrous and nonferrous metals is made possible by using it in conjunction with magnet drums and eddy current separators. Also, high velocity, low-pressure air streams are used in conjunction with vibratory de-stoner/classifiers to separate materials according to difference in bulk density.
The picking and sorting of “heavies” such as stones, bricks, dirt, metals and other heavy materials has become a popular application for vibratory equipment such as the De-Stoner/Classifier. Commingled materials such as nonferrous metals, paper and light plastic are also readily cleaned and separated, using finger screens that can be incorporated into vibrating conveyors or feeders.
What advantages does vibrating equipment offer in solid waste handling and recycling when compared to mechanical conveyors? Quite simply, its robust and inherently flexible operating principle makes it ideal for a wide range of material separation and sorting operations. Unlike mechanical conveyors, material on a vibrating conveyor is “live” and moves independently of the conveying unit.
Depending upon amplitude, frequency and other variables, these systems can provide a wide range of motion from gentle and smooth to an aggressive tossing action. These performance attributes enable vibratory equipment to screen, classify, align and turn material while it is conveyed. Vibratory equipment also has the inherent versatility to discharge material at more than one point, which lends itself to a wide range of material recovery facility (MRF) operating conditions.
The single knife “De-Stoner” is a dry classification equipment technology that was developed by General Kinematics Corp., Barrington, Ill. This patented equipment concept utilizes vibratory motion and high velocity air streams to fluidize and stratify material according to particle size and density.
“Heavies” such as ferrous metals, stones, and glass are removed in a dry system with no moving parts. The air fluidization section of the unit assists separation by stratifying acceptable materials such as aluminum and plastic. Single and dual knife systems are adjustable to adapt to a wide range of applications for the classification and separation of commingled materials. Typically, these include ASR (auto shredder residue), municipal solid waste, biomass fuel and refuse-derived fuel (RDF).
Vibratory finger screens are typically used to perform an initial “cut” or separation of mixed bulk materials that contain a variety of sizes. Finger screens can be considered (as can disc-type screeners or rotary trommels), and can help avoid the catching or hang-ups that frequently occurs in conventional wire-mesh screen equipment. Classification takes place when the incoming waste stream cascades over a series of slotted finger elements.
Special finger screen designs are available to sort commingled materials according to size without “fluffing,” or increasing the volume of paper or other light density materials. Finger screens also require less maintenance and system downtime because there are no rotating shafts to catch and wind material. Typical applications normally include solid waste sizing, paper classification, C&D waste screening and the recovery of metal from mass-burn bottom ash.
Metal scrap recovery has proven to be one of the most enduring applications for vibratory process equipment. The versatility and unique material motion of vibratory conveyors and feeders is often critical to downstream separation and sorting. Additionally, the heavy loading and abusive conditions encountered in most scrap recycling facilities are easily accommodated by the inherent ruggedness of vibrating equipment. A wide range of vibrating equipment designs have been developed to either feed or accept discharge from alligator and guillotine shears, or to uniformly feed commingled materials to magnets, eddy currents, or to manual sorting operations.
Trough design and installation is a critical factor in assuring the superior performance of shredder discharge conveyors. Typically, the conveyor is installed on supports to gain head room for servicing, with a slight decline to promote material travel. Units are constructed with flared troughs to relieve side pressure and minimize material jamming and potential shredder back up. Special attention must also be paid to the foundation below the shredder to help prevent jamming and promote serviceability. All these features combine to assure smooth, dependable flow of material to downstream conveying and separation equipment.
Vibratory feeders play an important role in improving the efficiency of most metals recycling facilities. They are typically used for material transfer, or as spreader units in front of magnets or eddy currents to help in the recovery of ferrous and nonferrous material.
When used with multiple magnets, vibratory feeders help to provide cleaner scrap, and require only a single discharge for ASR. Most important, the inherent “live” action of vibratory feeders provides superior magnet presentation due to the fact that material moves very smoothly and is evenly spread before the magnet drum.
A cleaner stream of recovered material is also possible when vibratory feeders are equipped with optional finger deck sections that help to remove unwanted fines prior to magnetic separation.
The author is the sales manager for General Kinematics Corp., Barrington, Ill.
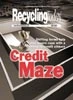
Explore the May 2001 Issue
Check out more from this issue and find your next story to read.
Latest from Recycling Today
- Magnomer joins Canada Plastics Pact
- Electra names new CFO
- WM of Pennsylvania awarded RNG vehicle funding
- Nucor receives West Virginia funding assist
- Ferrous market ends 2024 in familiar rut
- Aqua Metals secures $1.5M loan, reports operational strides
- AF&PA urges veto of NY bill
- Aluminum Association includes recycling among 2025 policy priorities