After being in the mixed C&D debris recycling business for six years, Central is obsessed with the notion of separating out the garbage, because management feels it is the key to success in marketing its many products.
“That is what separates us from other C&D recyclers,” says Robert C. Hosier, vice president. “We make a concerted effort to pull out the trash by making a positive pick for it. Then what you have left over are commodities that can be sold.”
To that end, the company has recently opened its new facility in Des Moines designed specifically to produce clean products. At the site, Central C&D makes products from, or separates for further processing into products, asphalt shingles, concrete and asphalt, gypsum, metals, old corrugated containers (OCC), and wood. In fact, the company makes two levels of wood products, including infeed for a nearby particleboard plant making furniture.
The Central C&D Recycling plant boasts a 90% recycling rate at 50 tons per hour, and makes no alternative daily cover and little cogeneration fuel.
BUILDING A BETTER MOUSETRAP
Hosier, along with company president Steve Corell, decided to develop a new plant that would make the products they wanted to sell. “We knew we had to step to another level with the new plant,” says Corell.
Hosier says the company sat down with the potential equipment suppliers separately and told them, “One thing you are going to take out of this conversation is that we don’t want the trash. I don't care if we miss a little wood or concrete. We need the trash out. As soon as we have the trash in there, then we are selling trash.”
Hosier and Corell settled on a combination starscreen/air separation/picking station/float tank system. Here’s how the system works at the 50-acre site.
First, incoming trucks are weighed and the drivers interviewed about the contents of their trucks. Clean gypsum, brush, and asphalt shingle waste are directed toward separate areas for processing. The rest is dumped in a corrugated metal building with a concrete floor (10 acres are paved with concrete), several doors and a ceiling high enough for all trucks to tip within.
The material is inspected and some minor presorting done. Then a wheel loader pushes it in place to be fed into the sorting system. More presorting is performed, concentrating on the plastics, especially the long sheets. Big pieces of concrete, wood, and steel are set aside because “you don’t want to drop 200 pounds of concrete on the transfer points in the system,” Hosier says.
A wheel loader feeds the sorting system, the majority of which is from Lubo USA, Stamford, Conn. A four feet, seven inches wide by 19 feet, eight inches long vibrating feeder starts the material up a nearly five-foot wide belt to the first sorting platform, manned by two of the best pickers at the plant. They remove large bulky items, such as carpet and long, stringy items that won’t go through the starscreen, which is the next step.
The starscreen is the same length and two inches wider than the vibrating feeder. The star diameter is two feet, two inches, and the stars are arranged in a pattern that allows 18 inches or so fall through. The actual setting varies from day to day and is easily adjustable. Overs from the screen proceed to an 85-feet-long sorting conveyor for further picking for “A” (better quality) wood, metals, cardboard, and then the trash toward the end. Aggregate is left on the line.
The unders from the first starscreen fall onto a conveyor making a 90-degree turn, and then the material takes another 90-degree turn into a second starscreen that screens out the 3/8-inch minus. This star diameter is 6.4 inches. The fines are sent to a separate pile and later sold as a non-structural fill for about $2 per ton. The overs go to a second picking line 61-1/2 feet long by three feet, three inches wide. Between the picking line and the second starscreen is an air separation system that removes the light fraction, such as small pieces of plastic and is integral to the cleanliness of the final product. A magnet also is on the secondary picking line.
Both picking lines are enclosed, and the secondary line feeds into a float tank made by Flo-Cait, Holland, Mich., to separate the wood from the aggregate. The wood is sent to the proper pile for later processing. There are two sizes of aggregate, small and large fraction. The small is used as is as a choke rock for temporary roads. The larger fraction is mostly sent to Corell Recycling, Steve Corell’s concrete and asphalt recycling operation at another site.
The air system is key to getting things clean, Hosier says. “It gets a lot of the plastics, cuts down on labor costs, and gets us a higher end product we can get more money for.”
There are 12 pickers on the line at the plant, 10 in the picking house and the two pre-sorters before the starscreens. Two loader operators move infeed and product around. Other personnel include a scale house person, and one person on pre-sort before feeding into the system. Currently the plant is operating six days a week, two shifts.
What those workers are making is a wide variety of products besides the extra-clean wood. Gypsum is processed and mixed along with clean wood to make an animal bedding product that farmers love, Hosier says.
The wood is made into chips with twin 300-hp electric grinders made by Terex Recycling, Myerstown, Pa. The chips must meet a tight spec for a particleboard manufacturer, says Hosier, and must have the correct percentage of long pieces and fines to work in the finicky particleboard plant.
Asphalt shingles are ground by a Beast grinder made by Bandit Industries Inc., Remus, Mich., for a couple of different applications. Most are put down on gravel roads as a dust suppressant. There has also been some headway with a local asphalt plant for use in their mixes, but they already have a large amount of their own recycled asphalt pavement to use, so shingle use is not high on their priority list.
Metals and OCC are also diverted and processed.
Central C&D’s management also wanted to get beyond the “trash mentality” for C&D it sometimes sees elsewhere, according to Hosier, who was named Iowa Recycler of the Year in 2000. “That’s why we spent the extra money to get this type of system. We spent the extra nickel to make an extra dime. We didn’t want to be like some folks who are doing the minimum; we needed to get out of the mentality of calling it trash by a different name.”
With its system, Central C&D Recycling is recycling 90% of the mixed C&D waste it takes in, processes more than 50 tons per hour, and sells a lot of its products for more than $10 per ton. “We have the ability to move a lot of volume with the least amount of cost, and get a high return on the product coming back out,” says Hosier. “We made the investment, and we think it is just a matter of time before the rest of the industry will have to, also.” RT
The author is executive director of the Construction Materials Recycling Association (CMRA), Lisle, Ill., and associate publisher of C&D Recycler magazine. A more comprehensive version of this article appears in the May/June C&D Recycler.
Get curated news on YOUR industry.
Enter your email to receive our newsletters.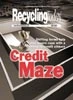
Explore the May 2001 Issue
Check out more from this issue and find your next story to read.
Latest from Recycling Today
- ICM to host co-located events in Shanghai
- Astera runs into NIMBY concerns in Colorado
- ReMA opposes European efforts seeking export restrictions for recyclables
- Fresh Perspective: Raj Bagaria
- Saica announces plans for second US site
- Update: Novelis produces first aluminum coil made fully from recycled end-of-life automotive scrap
- Aimplas doubles online course offerings
- Radius to be acquired by Toyota subsidiary