Governments and manufacturers of electronic products are increasingly coming under pressure regarding the safe disposal of electronic products once their useful lives have been completed. End-of-life (EOL) legislation for electronics is being contemplated in the European Union (EU), as well as North America, and being implemented in countries such as Sweden. Upcoming EOL legislation requires electronics manufacturers to dispose of their old electronic products safely.
A HIGH-VOLUME SYSTEM
Electronics recycling has been approached several ways, with re-use of entire machines and select components having developed into a significant industry. But even with re-use systems in place, a steady volume of computers, monitors, keyboards and printers—as well as entertainment appliances and telecommunications equipment—reaches the point of disposal or recycling each day.
Shred-Tech, located in Cambridge, Ontario, Canada, has engineered and manufactured a system that goes beyond the disposal of outdated computers and electronic scrap and offers the potential to recover some materials. The Shred-Tech ESR6000 system reduces, separates, and then recovers the component materials that make up these electronic products.
The system has the ability to process three tons per hour of assorted electronic scrap with minimal handling and disassembly. Lap and desktop, as well as mainframe, computers can be processed along with telecommunications switch racks, some medical devices and some military equipment. The system reduces and then separates component material such as plastic, aluminum, copper and steel as well as precious metals. These materials can then be sold as commodities.
The precious metals recovered by the system are present in the dust and fines and may contain three or more ounces of precious metals per ton of material processed. The fines and dust must be then shipped to a smelter, such as the Horne smelter operated by Noranda Metallurgy, Toronto, for final recovery and refining of the precious metal.
Two ESR-6000 systems have been installed, one in Canada and one in the U.S. The Canadian system operates in Toronto, Ontario, and the U.S. system in Roseville, Calif. A joint venture exists between Noranda’s subsidiary Micro Metallics and Hewlett-Packard Co., Palo Alto, Calif., with respect to the California operation. The system processes and recovers base and precious metals as well as other recyclable materials from stockpiles of HP electronic hardware.
The Shred-Tech system combines electrical and mechanical technology into two key stages. In the first stage, obsolete electronic products enter the automatic feed system for reduction. Primary and secondary shredding equipment reduces large and small items. A tertiary shredder reduces the shredded material further. This allows for free-flowing materials, without encapsulating the various metals that make up electronic scrap.
The result is clean, consistently sized material, ready for second stage separation of the base components. A series of proprietary devices as well as rare earth magnets, electro magnetic separators and vibratory separators are used in the separation process. Separated materials are then shipped off-site for further refining or recycling.
An integrated computer system controls the system operation while remote video cameras monitor system functioning. Electrical controls include touch screens for man-to-machine interface. The system also incorporates software driven self-diagnostics and links to technicians and engineers via a direct phone modem. The system occupies approximately 17,000 square feet of floor space and requires an additional 33,000 square feet for receiving and storage.
Proponents of shredding obsolete electronics say such systems can offer several advantages by:
•Reducing, with minimum disassembly, all types of electronic waste.
•Efficiently processing high volumes of electronic scrap.
•Recovering base metals such as aluminum, copper, steel, stainless steel, and zinc.
•Recovering high value precious metals such as gold, silver, platinum and palladium.
•Providing secure destruction of used equipment thus eliminating security breaches.
By reducing and separating electronic equipment back to its original materials, the system can ensure that post-consumer electronic products are efficiently and economically recycled.
Shred-Tech was awarded the Financial Post Gold Award for Environmental Technology in 1998 based on the successful design and installation of the ESR System at the Hewlett Packard/Micro Metallics facility in Roseville.
The company has supplied equipment to companies such as BASF, Boeing, IBM, Alcan, Norsk Hydro, and the US Armed Forces, helping them to meet their specific environmental challenges.
The author is vice president of sales and marketing for Shred-Tech, Cambridge, Ontario, Canada.
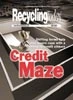
Explore the May 2001 Issue
Check out more from this issue and find your next story to read.
Latest from Recycling Today
- Magnomer joins Canada Plastics Pact
- Electra names new CFO
- WM of Pennsylvania awarded RNG vehicle funding
- Nucor receives West Virginia funding assist
- Ferrous market ends 2024 in familiar rut
- Aqua Metals secures $1.5M loan, reports operational strides
- AF&PA urges veto of NY bill
- Aluminum Association includes recycling among 2025 policy priorities