
The global labor and regulatory landscapes have been constantly changing in the 21st century. Shifting circumstances have altered the way scrap processors and traders operate and conduct business.
Early in the century, mixed metals grades of all types could be shipped from North America to Asia—and to the People’s Republic of China in particular—with the quality or chemistry of the loads seemingly just as negotiable as the price.
In the most recent eight to 10 years that has changed significantly, causing buyers and sellers of mixed metals to let processors know investments in sorting will be needed to keep shredded nonferrous grades viable products.
Simplifying the complicated
The sorting tasks facing auto shredder operators have become more complicated in part because of the changing composition of automobiles and large appliances.
Automobiles, in particular, are now designed and built with an increasing array of not just plastic components but also additional wiring, printed circuit boards, small batteries and other electronic components, plus one or more air bags and additional emissions control components.
Their presence in automobile hulks complicates the material stream that remains after large drum magnets remove the ferrous scrap.
The increasing variety in the typical vehicle’s composition is occurring at the same time formerly common hand sorting of mixed metals grades in China has faded away. In tandem, China’s government has restricted nonferrous scrap imports to the purest of grades. While some other nations can still accept lower grade mixed metals, those markets are smaller in volume and have the potential to tighten restrictions.
The way forward for shredder operators and the nonferrous sorting specialists who serve them has been to introduce an increasing variety of automated sorting technologies. Not only are more magnetic, optical and sensor sorting devices available, but processors have been arraying them in greater numbers.
Among the devices increasingly common in downstream systems is the inductive sensor sorter. Germany-based technology provider Steinert describes its Induction Sorting System (ISS) as “the perfect addition to magnetic sorting and eddy current separation for recovering residual metals” and as being “especially suitable for stainless steels and composite materials, such as cables or circuit boards.”
In describing how its ISS works, Steinert, which has a U.S. office in Kentucky, writes that shredded material moves via conveyor over “an arrangement of sensors” that “analyze the material over the whole width of the conveyor belt by means of magnetic induction.”
Next, according to the company, “As soon as metallic particles are detected, electronic signals are sent to [a] central computerized control unit. Compressed air jets, individually controlled by the programming, push the detected metals over [a] diverter gate.”
Mick Erdos, the Ohio-based vice president of sales for Italy-based SGM Magnetics, says sensor sorters are most commonly deployed in downstream systems “to recover small bare copper wire and to separate between stainless steel and copper wire.”
Those tasks, and several emerging ones, have become increasingly important in an industry landscape where the tolerance for out-of-specification materials has risen globally.
Making the grade(s)
Processors and traders of mixed metals grades ultimately are trying to meet specifications for such grades developed and maintained by the Washington-based Institute of Scrap Recycling Industries (ISRI). (See the sidebar, “Speaking the language,” above.)
Bill Close, business development manager for Buffalo, New York-based Wendt Corp., says sensor sorters play a role in improving the quality of several of these grades, whether they are mostly aluminum, copper or stainless steel.
However, Close and Erdos say inductive sorting on its own cannot accomplish a more comprehensive upgrading process that also involves eddy current separator (ECS) units, two types of X-ray identification technology, laser-induced breakdown spectroscopy (LIBS) and other technologies that identify and sort metals based on their color or chemistry.
Sponsored Content
Labor that Works
With 25 years of experience, Leadpoint delivers cost-effective workforce solutions tailored to your needs. We handle the recruiting, hiring, training, and onboarding to deliver stable, productive, and safety-focused teams. Our commitment to safety and quality ensures peace of mind with a reliable workforce that helps you achieve your goals.
Sponsored Content
Labor that Works
With 25 years of experience, Leadpoint delivers cost-effective workforce solutions tailored to your needs. We handle the recruiting, hiring, training, and onboarding to deliver stable, productive, and safety-focused teams. Our commitment to safety and quality ensures peace of mind with a reliable workforce that helps you achieve your goals.
Sponsored Content
Labor that Works
With 25 years of experience, Leadpoint delivers cost-effective workforce solutions tailored to your needs. We handle the recruiting, hiring, training, and onboarding to deliver stable, productive, and safety-focused teams. Our commitment to safety and quality ensures peace of mind with a reliable workforce that helps you achieve your goals.
“Sensor-based technologies like X-ray fluorescence (XRF) and transmission (XRT), LIBS and color and shape sorters have the ability to separate metals depending on atomic number, density, metal composition, color and shape, respectively,” Erdos says.
Close says Wendt Corp., which distributes sorting equipment made by Europe- based Tomra, has a new XRT sorting device at its Buffalo showroom “that can sort metals down to 5 millimeters (0.2 inches) in particle size.” He says shredded materials can be tested using the device and the findings can be “shared remotely during these COVID days.”
Mechanical sorting methods have not disappeared, either. Wendt recently has entered into a partnership with Missouri-based Didion International Inc. to distribute Didion’s metal polishing drums. The Didion drums are designed to remove dirt, debris, surface contamination and oxidation from shredded metal pieces.
The two companies say a “domestic drum” can be used in coordination with an XRT device or heavy media plant to upgrade shredded aluminum and stainless steel grades, including zorba and zurik. They say an “export drum” has been built to meet recently enacted Chinese export requirements for zorba “by adding screening to separate the cleaned and polished zorba into three sized products” that can be fed “directly into a bagging system ready for export.”
Costs and benefits
The equipment to identify and sort metals comes at a cost. Equipment suppliers and recyclers continue to communicate to determine when the investment makes sense.
Erdos says, “When SGM works with shredder operators on greenfield installations or upgrades to their systems, the most important aspect of designing the right nonferrous system is knowing the volume of auto shredder residue created per month in order to prepare a return on investment for said customer.”
Close says Wendt “will look at the total process with our clients,” turning to sensor sorters as one of many potential upgrades.
Even with the economic impacts of COVID-19 and related restrictions, scrap processors seem convinced that investing in sensor sorters and other sorting technology remains an imperative. With demand for high-quality shredded metals grades growing steadily, scrap processors and equipment and technology providers likely will have plenty to talk about.
Get curated news on YOUR industry.
Enter your email to receive our newsletters.
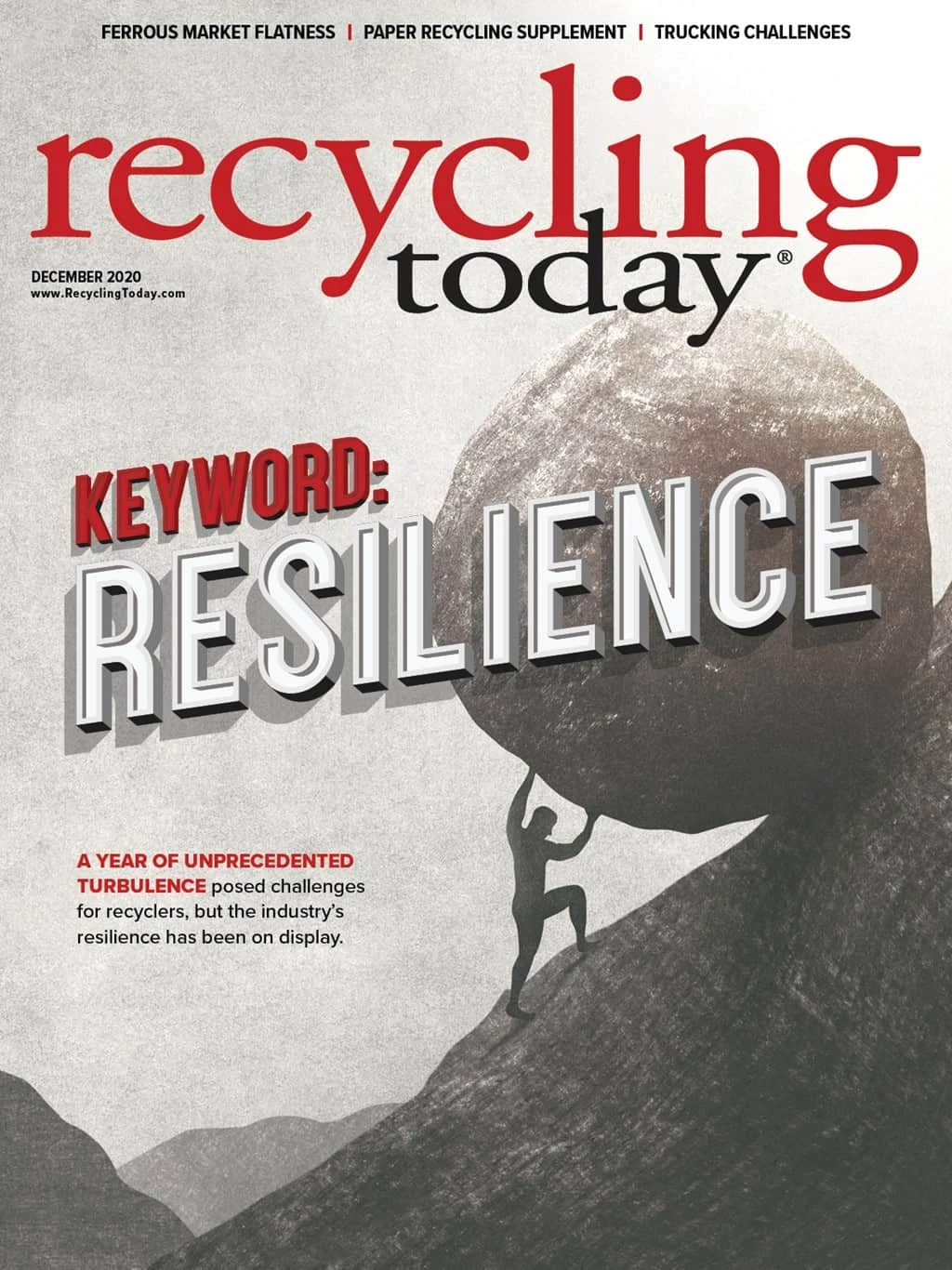
Explore the December 2020 Issue
Check out more from this issue and find your next story to read.
Latest from Recycling Today
- British Steel mill’s future up in the air
- Tomra applies GAINnext AI technology to upgrade wrought aluminum scrap
- Redwood Materials partners with Isuzu Commercial Truck
- The push for more supply
- ReMA PSI Chapter adds 7 members
- Joe Ursuy elected to NWRA Hall of Fame
- RRS adds to ownership team
- S3 Recycling Solutions acquires Electronics Recycling Solutions